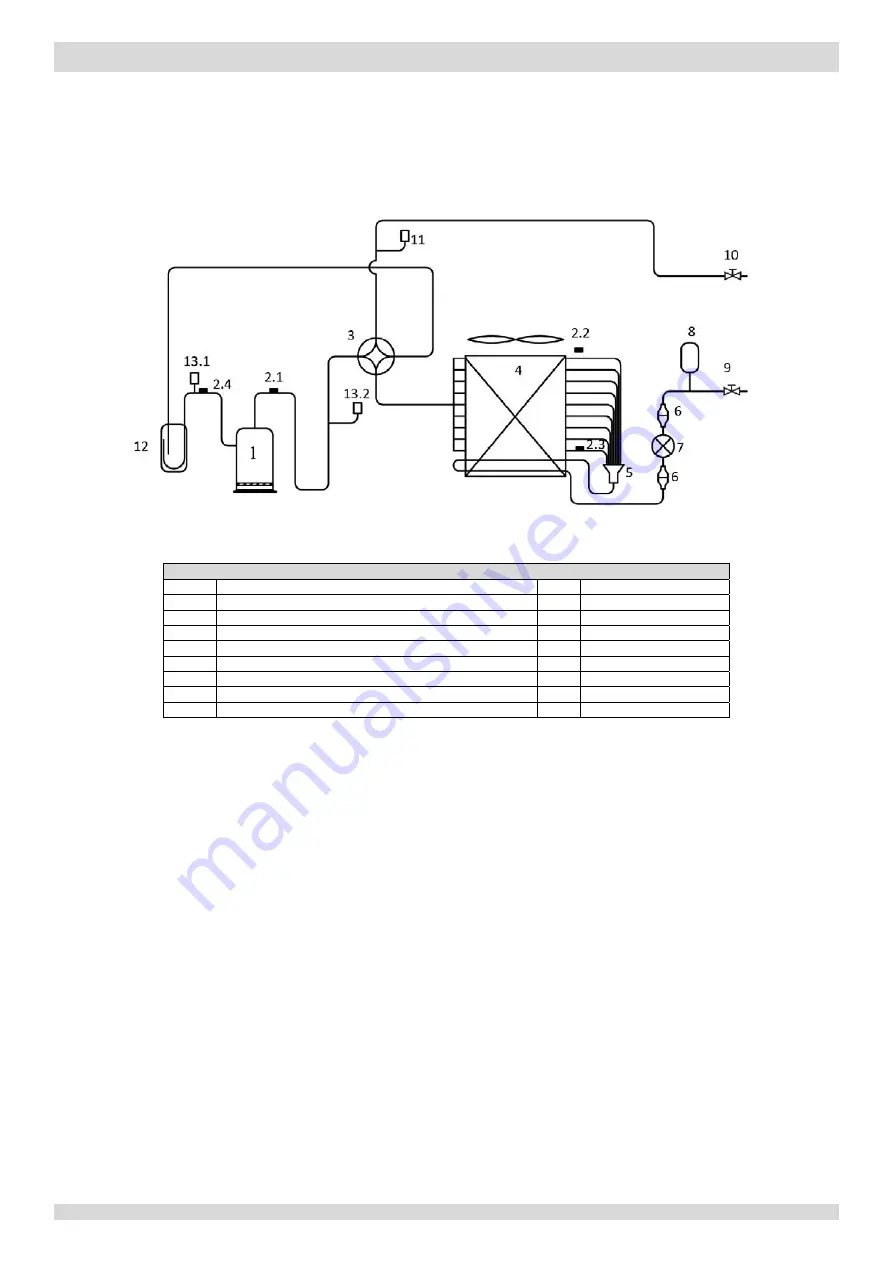
201703
9
P
art 2 - Component La
y
o
ut and R
e
frig
e
ran
t Cir
cuits
2 Piping Diagrams
2.1 Outdoor Unit Piping
Figure 2-2.1:
piping diagram
Legend
1
Compressor
7
Electronic expansion valve
2.1
Discharge pipe temperature sensor
8
Accumulator
2.2
Outdoor ambient temperature sensor
9
Stop valve (liquid side)
2.3
Air side heat exchanger refrigerant outlet temperature sensor
10
Stop valve (gas side)
2.4
Suction pipe temperature sensor
11
Pressure sensor
3
4-way valve
12
Separator
4
Air side heat exchanger
13.1
Low pressure switch
5
Distributor
13.2
High pressure switch
6
Filter
Key components:
1.
Accumulator:
Stores liquid refrigerant and oil to protect compressor from liquid hammering.
2.
Electronic expansion valve (EXV):
Controls refrigerant flow and reduces refrigerant pressure.
3.
Four-way valve:
Controls refrigerant flow direction. Closed in cooling mode and open in heating mode. When closed, the air side heat
exchanger functions as a condenser and water side heat exchanger functions as an evaporator; when open, the air
side heat exchanger functions as an evaporator and water side heat exchanger function as a condenser.
4.
High and low pressure switches:
Regulate refrigerant system pressure. When refrigerant system pressure rises above the upper limit or falls below the
lower limit, the high or low pressure switches turn off, stopping the compressor.
5.
Separator:
Separates liquid refrigerant from gas refrigerant to protect compressor from liquid hammering.
Models 4 to 8kW
MUNDOCLIMA AEROTHERM V17 - BIBLOC