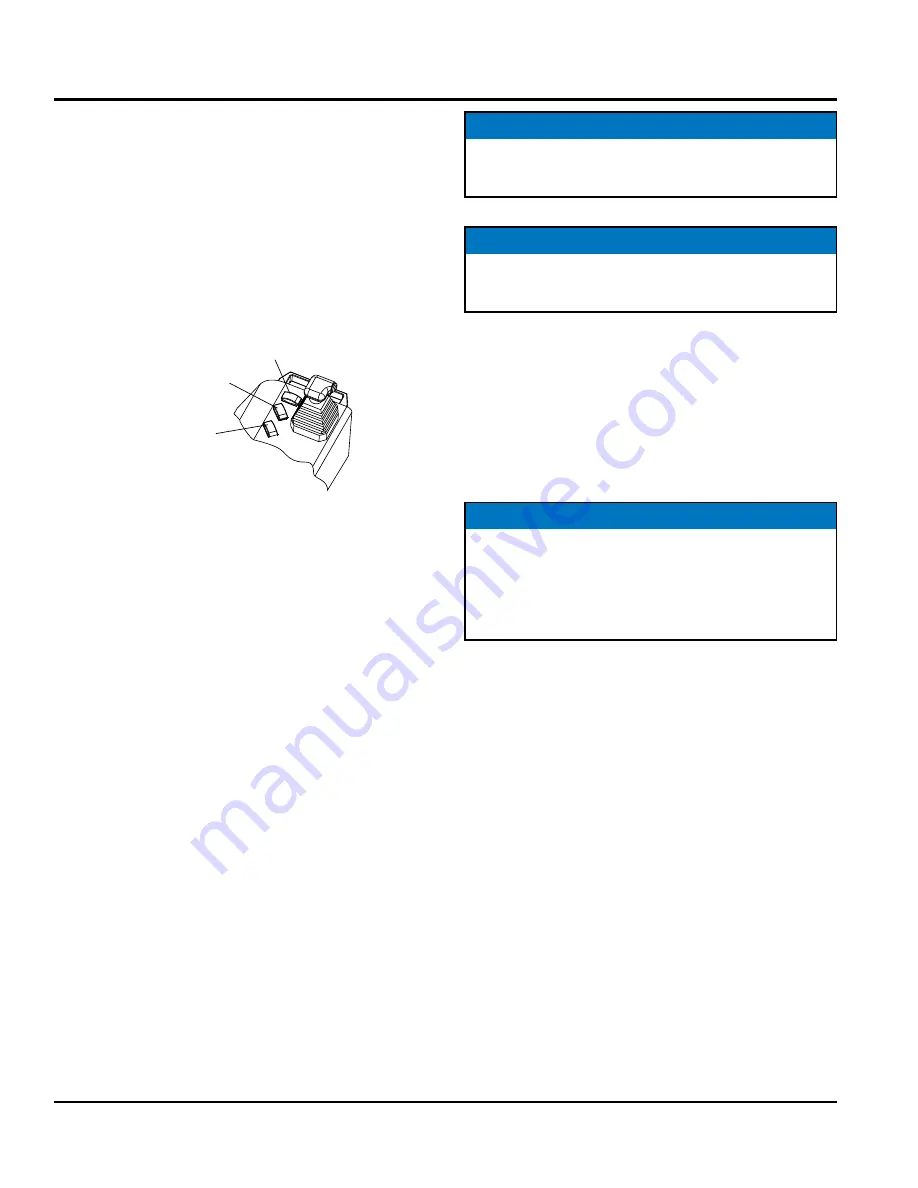
PAGE 28 — STXD6i RIDE-ON TROWEL• OPERATION MANUAL — REV. #2 (05/28/15)
OPERATION
BLADE PITCH CONTROL
There are two modes of operation of the blade pitch system
that can be set by the Pitch Mode Switch (Figure 20):
Smart Pitch™
Manual
The trowel blades can be pitched for various finishing
operations with the two rocker switches located on the left
control panel next to the left joystick control (Figure 20).
Figure 20. Blade Pitch Control
Smart Pitch™ Mode
When the Pitch Mode Switch is in the Smart Pitch™ position
(indicator light on), the twin-pitch and left-pitch switches
operate as follows:
1. When the Twin Pitch Switch (3-position, center off)
is pressed (up or down), the right and left hand rotor
pitch are changed and then the left hand rotor pitch is
synchronized to the right hand as follows:
a. The Twin Pitch Switch (up or down) causes the RH
Pitch (up or down) Coil and LH Pitch (up or down)
Coil and Pitch Dump Valve Coil to be actuated
changing the pitch of the blades.
b. When the operator achieves the desired pitch on
the right hand blades and releases the Twin Pitch
Switch, the LH Pitch (up or down) coil and Pitch
Dump Valve Coil are actuated until the calibrated
LH Pitch Position signal matches calibrated RH
Pitch Position signal (.010” by Default). During this
time the Pitch Mode Light will flash (.1 s on, .1 s off).
2. When the Left Pitch Switch (3-position, center off) is
pressed the pitch on the left rotor will be changed, while
the pitch on the right rotor remains constant. The Pitch
Mode Light will turn off, to indicate pitch function is in
the unsynchronized state
PITCH MODE
SWITCH
TWIN-PITCH
SWITCH
LEFT-PITCH
SWITCH
MANUAL Mode (Pitch Mode Light is Off)
1. When the Twin Pitch Switch is pressed (up or down),
the pitch on both rotors will be changed simultaneously
but non-synchronously.
2. When the Left Pitch Switch is pressed the pitch on the
left rotor will be changed, while the pitch on the right
rotor remains constant.
PANNING Mode
When both the Twin Pitch Switch and Left Pitch Switch are
pressed in the down position and held for preset period (5s
by default), the machine will enter Panning Mode.
1. The RH Pitch DN Coil and LH Pitch DN Coil will be
activated pulling the yokes upward against Retracted
Cylinder Stop, deactivating the pitch system, and
allowing the blades to float for panning.
2. The Pitch Mode Light will flash (.9 s on .1 s off) when
in this mode.
3. Machine remains in this mode until either the Twin
Pitch Switch or Left Pitch Switch is activated in the
upward direction.
NOTICE
Moving the switches forward increases the pitch while
moving them backward decreases the pitch.
NOTICE
Momentarily depressing the Twin Pitch Switch will re-
synchronize the pitch.
NOTICE
IMPORTANT!
To get blades absolutely flat for using
float pans, pitch them as follows:
Press and hold down both pitch switches until mode
light blinks before installing float pans.