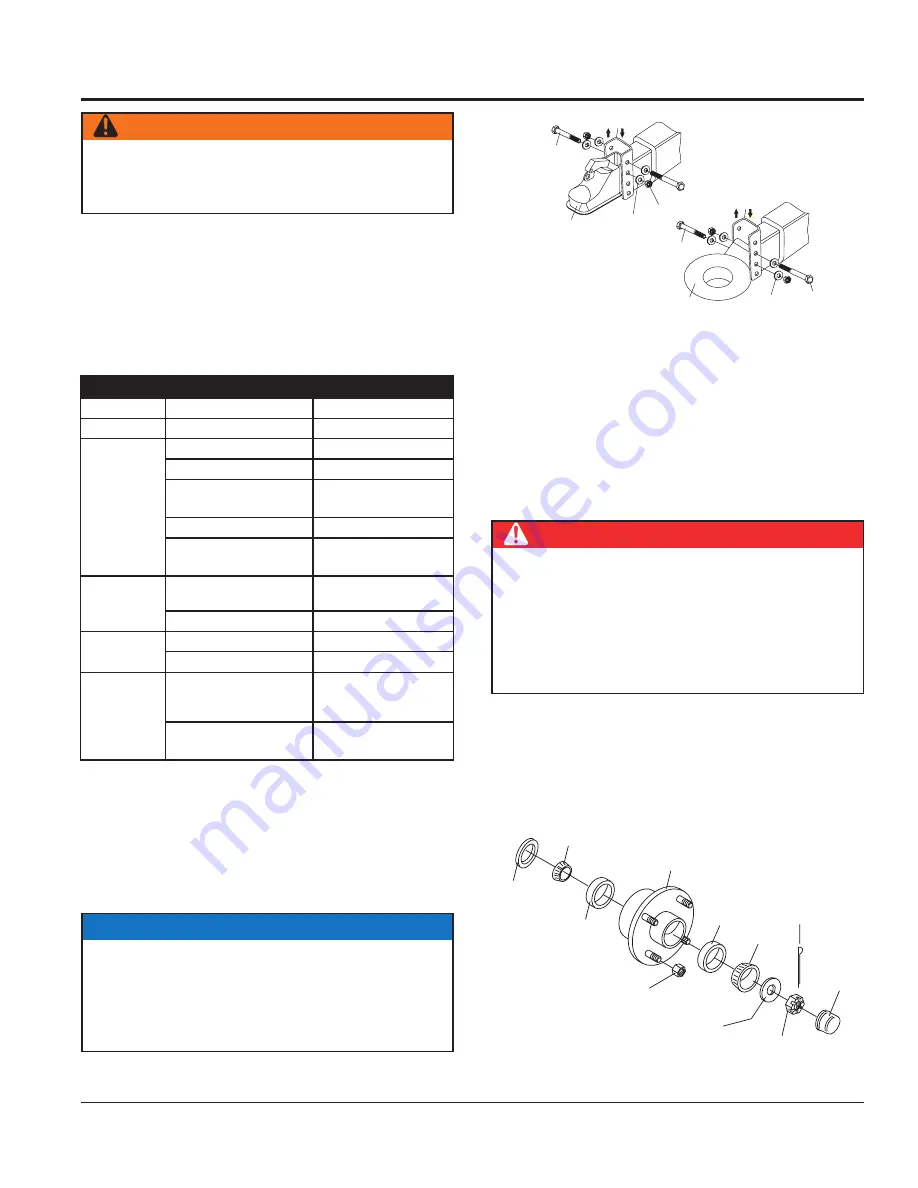
MAYCO LS300G CONCRETE PUMP • OPERATION MANUAL — REV. #2 (09/09/19) — PAGE 53
TRAILER MAINTENANCE
Periodically check the actuator mounting fasteners for
damage or loosening. Inspect the actuator for worn or
damaged parts. As you are towing your trailer, be aware
of any changes in braking quality. This could be an early
warning of brake or actuator malfunction and requires
immediate attention. Consult a certified brake specialist to
make necessary adjustment or repairs
ADJUSTABLE CHANNEL
Your trailer may be equipped with an adjustable channel
(Figure 58) that allows the coupler to be raised or lowered
to a desired height. Periodically check the channel bolts
for damage or loosening.
WARNING
Failure to maintain proper fluid level in the actuator
may result in loss of braking action which could cause
severe property damage, injury or death.
Table 8. Hydraulic Brake Troubleshooting
Symptom
Possible Cause
Solution
No Brakes
Brake line broken or kinked?
Repair or replace.
Weak Brakes or
Brakes Pull to
One Side
Brake lining glazed?
Reburnish or replace.
Trailer overloaded?
Correct weight.
Brake drums scored or
grooved?
Machine or replace.
Tire pressure correct?
Inflate all tires equally.
Tires unmatched on the
same axle?
Match tires.
Locking Brakes
Brake components loose,
bent or broken?
Replace components.
Brake drums out-of-round?
Replace.
Noisy Brakes
System lubricated?
Lubricate.
Brake components correct?
Replace and correct.
Dragging
Brakes
Brake lining thickness
incorrect or not adjusted
correctly?
Install new shoes and
linings.
Enough brake fluid or correct
fluid?
Replace rubber parts
fill with DOT 4 fluid.
NOTICE
When replacing channel mounting hardware (nuts,
bolts and washers),
NEVER
substitute substandard
hardware. Pay close attention to
bolt length
and
grade
.
ALWAYS
use manufacturer’s recommended parts
when replacing channel mounting hardware.
Figure 58. Adjustable Channel
Wheel Bearings
Wheel bearings (Figure 58) must be inspected and
lubricated once a year or every 12,000 miles to ensure
safe operation of your trailer.
If trailer wheel bearings are immersed in water, they must
be replaced.
If the trailer has not been used for an extended amount
of time, have the bearings inspected and packed more
frequently, at least every six months and prior to use.
Follow the steps below to disassemble the wheel hub and
service the wheel bearings. See Figure 59.
Figure 59. Wheel Hub Components
2" or 2-5/16" BALL
COUPLER
ADJUSTABLE
CHANNEL
5/8" FLAT
WASHER
5/8" X 11" X 5"
BOLT
5/8"
NYLOC
NUT
ADJUSTABLE
CHANNEL
5/8" FLAT
WASHER
5/8"
NYLOC
NUT
5/8" X 11" X 5"
BOLT
3" PINTLE EYE
RING
DANGER
If trailer wheels are underwater for a long period of
time, wheel bearings may fail. If this is the case, service
wheel bearings immediately.
The possibility exists of the wheels falling off causing
equipment damage and severe bodily harm or even
death!
WHEEL
HUB
BEARING
CUP
BEARING
CUP
BEARING
BEARING
OIL
SEAL
SPINDLE
NUT
SPINDLE
WASHER
COTTER
PIN
DUST
CAP
LUG
NUT
Summary of Contents for MAYCO LS300G
Page 2: ...PAGE 2 MAYCO LS300G CONCRETE PUMP OPERATION MANUAL REV 2 09 09 19 PROPOSITION 65 WARNING...
Page 5: ...MAYCO LS300G CONCRETE PUMP OPERATION MANUAL REV 2 09 09 19 PAGE 5 NOTES...
Page 73: ...MAYCO LS300G CONCRETE PUMP OPERATION MANUAL REV 2 09 09 19 PAGE 73 NOTES...
Page 85: ...MAYCO LS300G CONCRETE PUMP OPERATION MANUAL REV 2 09 09 19 PAGE 85 HYDRAULIC SYSTEM DIAGRAM...