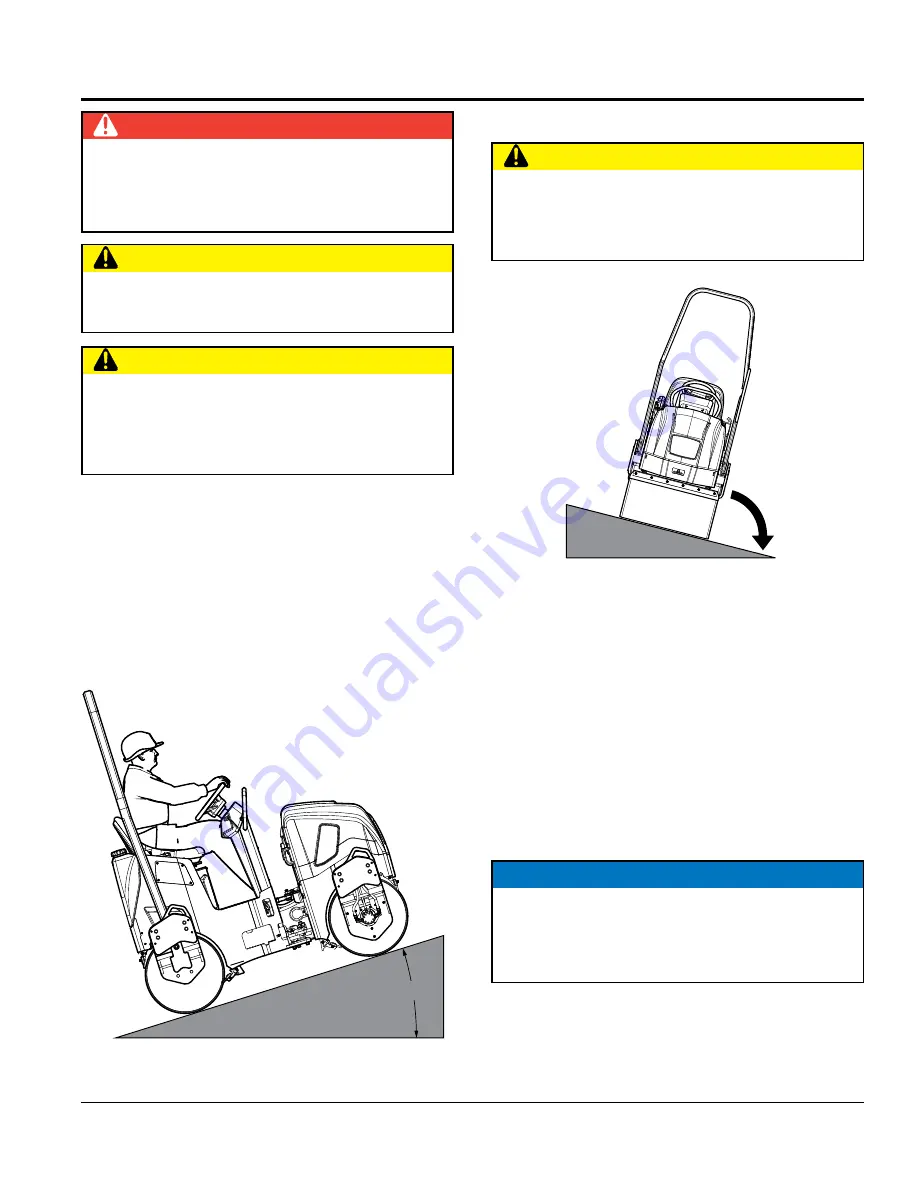
AR14H RIDE-ON ROLLER • OPERATION MANUAL — REV. #3 (09/06/19) — PAGE 13
GENERAL INFORMATION
OPERATING ON SLOPES
Special care must be taken when operating the roller on
hills or slopes. There exists the possibility of serious injury
to the operator and severe damage to the roller in the event
of a roll over.
ALWAYS
operate the roller up and down hills
rather than from side to side. For safe operation, hillside
slopes should not exceed 14 degree (25 % grade). See
Figure 2. Always wear seat belt when operating the roller.
Figure 2. Recommended Slope
DANGER
DO NOT
allow personnel to stand under or near any
suspended machine. Before operating the roller, make
sure that personnel and obstacles are free from the
roller’s path. Serious injury or death may result.
CAUTION
ONLY
use approved certified lifting devices capable of
lifting at least 4,000 lb. (1,814 Kg.).
CAUTION
When lifting of the roller is required, only use the
provided lifting eyes to lift the roller. Using other sections
of the roller for lifting purposes may cause severe
damage to the roller.
25%
IMPROPER OPERATION ON SLOPES
Figure 3. Improper Operation on Slope
In the event the roller does tip over, if at all possible, try to
shut down the engine by turning the ignition key to the
OFF
position. Extreme care must be taken to prevent damage
to the engine. When the roller has been tipped over, oil
from the engine crankcase can flow into the combustion
chamber, which can severely damage the engine the next
time it is started.
IMMEDIATELY
after a unit has tipped over, upright the
unit as soon as possible to prevent oil from leaking into
the combustion chamber.
CAUTION
NEVER
operate the roller on side slopes (Figure 3). The
possibility exists that the roller could tip over (roll over),
thus causing bodily harm, even death, and serious
damage to the equipment.
SIDE TO SIDE
OPERATION
NOT
RECOMMENDED
ROLL OVER
NOTICE
To prevent damage to the engine after a rollover, the
roller must not be started.
NEVER
start a roller after
a rollover. Contact your nearest authorized Multiquip
dealer for instructions or servicing.