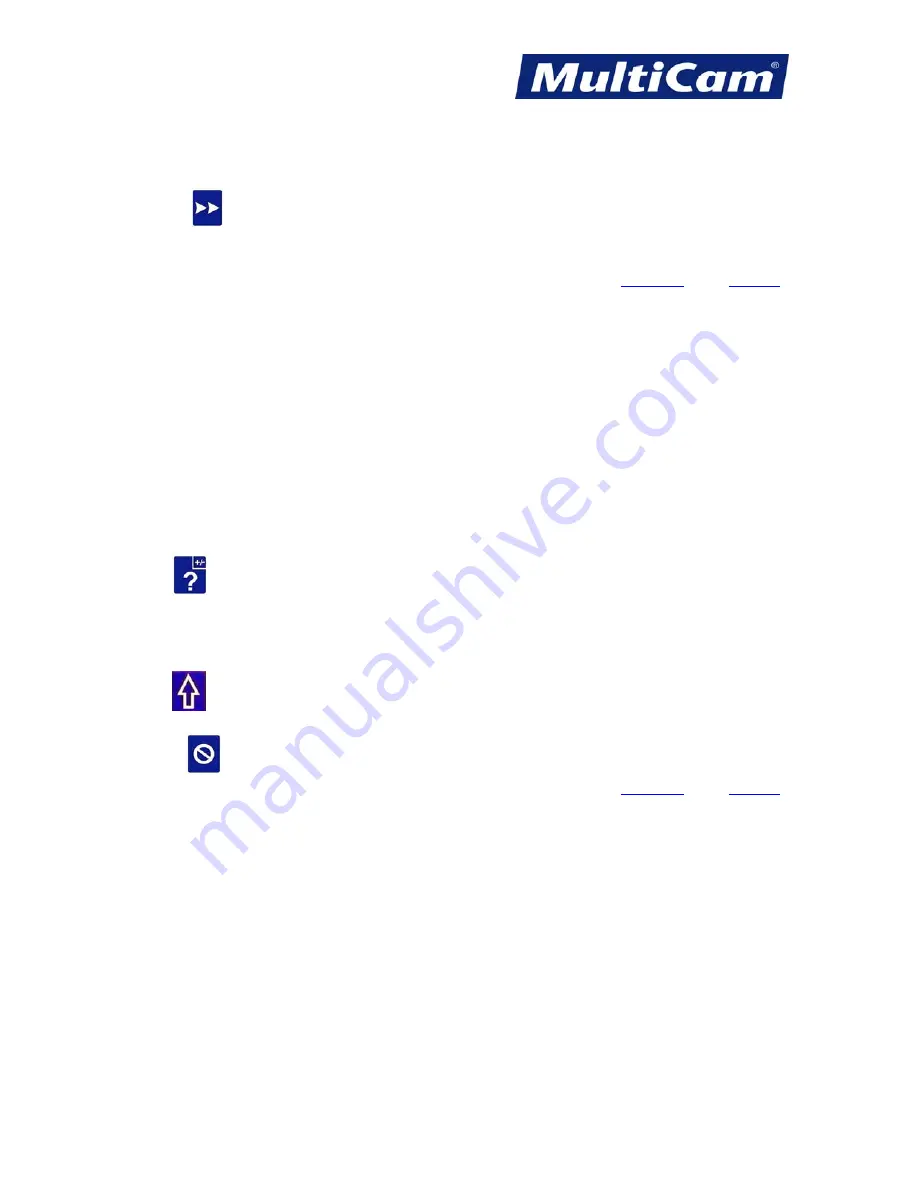
KF
16
Innovation. Quality. Performance. Best in Industry. Worldwide.
Jog Speed
Press
Jog Speed
to toggle between 3 different speeds at which the machine can Jog the
MultiCam
Plasma
System. The keypad display will prompt the operator with
Jog=
FAST
,
MED
, or
SLOW
. These words show the
rate at which the machine will Jog.
Help
The Help
function allows the operator to learn the functions of any Hot Key selected. There are 2 modes of the
Help function:
Normal
and
Shifted
. In
Normal
mode, the operator can review the standard function of any Hot
Key on the display. In
Shifted
mode, the operator can review the second or shifted function of that key on the
display.
1. Press
Help
to access the Hot Key Help Feature.
2. Press any key for a brief description of that key in
Normal
mode.
3. Press
Shift
and any key for a brief description of that key in
Shifted
mode.
4. Press
Cancel
twice to exit help.
Routers * Lasers * Plasma * Water Jets * Knife Cutters
www.MultiCam.com v. 03 13