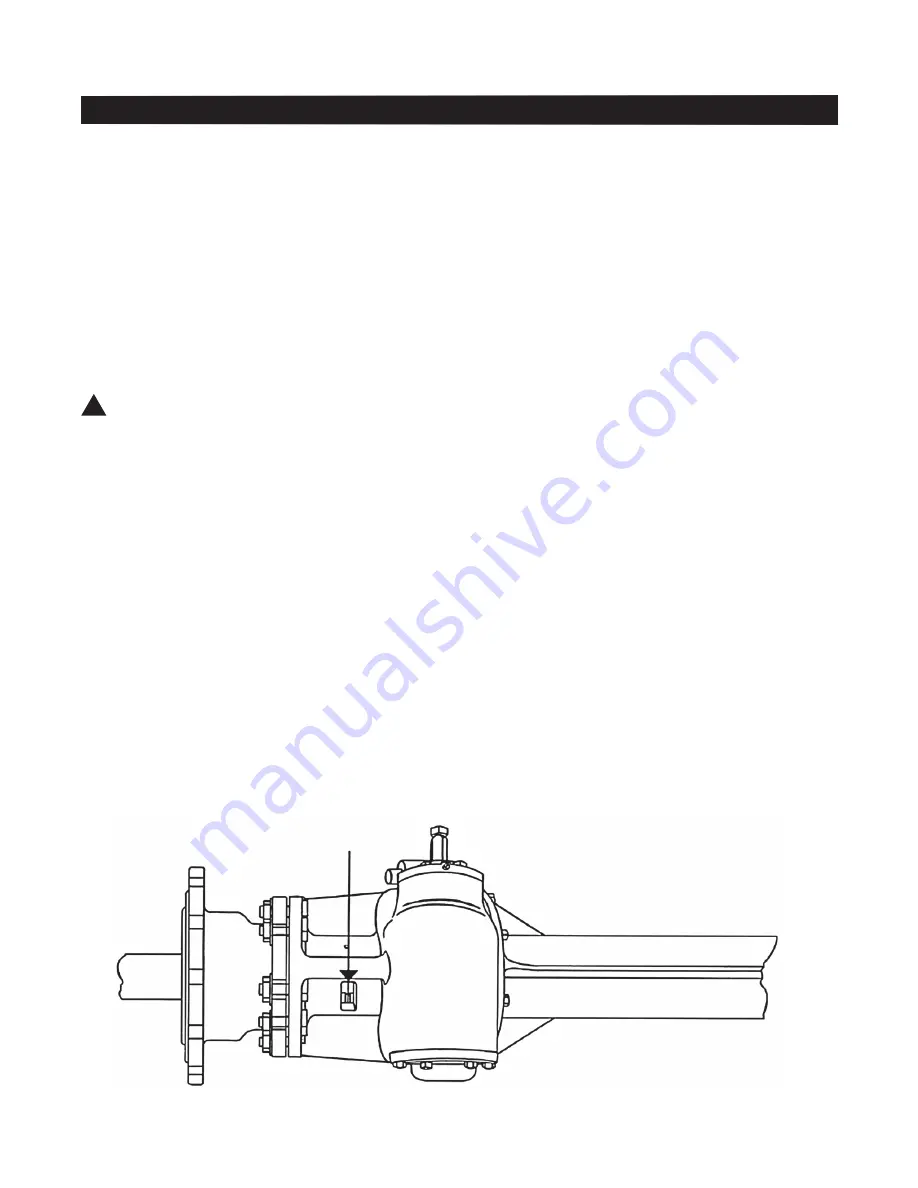
4
MUELLER
®
C1-36 Drilling Machines
Operating Instructions
5
18. Unbolt adapter from valve and
remove adapter and drilling machine
from valve as a unit.
19. Advance boring bar by rotating
feed crank counter-clockwise and
remove hub retaining bolt, (retaining
screw from cutter arbor or retaining
screws from shank of solid drill.)
Remove cut-out section of pipe, shell
cutter, cutter hub or cutter arbor and
pilot drill as a unit.
20. If cutting operation becomes
difficult, follow one of these methods:
a) If cutter has difficulty in cutting,
becomes dull or should stall
after the cut is started, withdraw
the cutter, close valve, remove
machine and sharpen or replace
cutter. Reassemble and proceed
in the regular manner.
b) If cut is well along, release
automatic feed and feed machine
by hand by holding back on
the feed crank at the rear of
the machine a little each half
revolution.
NOTE: Automatic feed should
be used whenever possible.
Automatic feed also provides
the correct tool feed.
14. Continue the cutting operation
until the cutter stops cutting or until
feed indicator reads the amount
shown in the travel chart. (See
pages 7–10 for travel chart).
15. Check completion of cut by
releasing automatic feed and
attempting to advance cutter by
rotating feed crank. If it does not
advance easily, the cut is not
completed and automatic feed
knob must be pushed in to engage
automatic feed for further cutting.
CAUtIoN: stop advancing
the boring bar when the limit line
becomes visible through the drive
box drain hole. see illustration at
bottom of page 5.
Watch the travel carefully when
making a 1
1
/
2
”/DN40 or 2”/DN50
cut. Make sure that the front end
of the boring bar, which is larger in
diameter than the drill, does not hit
the valve seat.
16. When cut is completed, release
automatic feed and withdraw cutter
to its rearmost position by rotating
feed crank clockwise.
17. Close valve securely.
IMpoRtANt: stop advancing
the boring bar if the limit line
becomes visible through drive
box drain hole. It will result in
extensive damage to the machine.
this applies to C1-36 machines
manufactured prior to september
1, 1995. C1-36 machines manu-
factured after september 1,
1995, or rebuilt after this date
and that have “ot” or Model 6
stamped on the name plate have
an overtravel protection feature
which is designed to prevent
damage should the boring bar
be inadvertently advanced too
far. Machines should never be
allowed to overtravel. Feature
does not prevent damage to the
feed screw that could occur as
a result of using dull drills or
cutters.
!
Limit Line