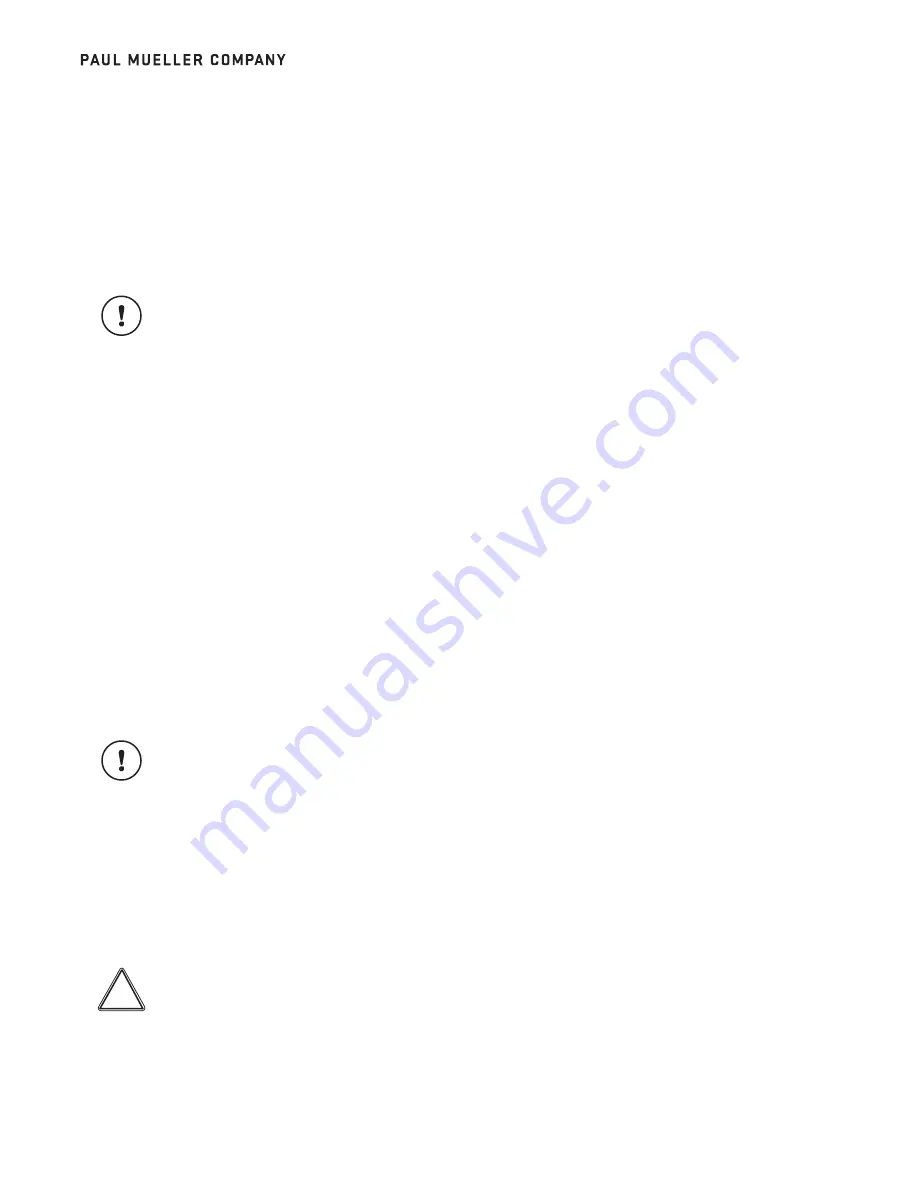
Mueller E-Star OESE 3.5 and 5 HP HFC Condensing Unit
Installation and Operation Manual, Part No. 8828747
Effective April 13, 2020
3.3
WEIGH-IN REFRIGERANT CHARGING (CONTINUED)
6. When the system pressure equalizes with cylinder pressure, energize the compressor.
7. Monitoring the weight of the refrigerant cylinder, weigh in the remaining refrigerant charge, in liquid state, at
the suction service valve (P2).
IMPORTANT: Liquid refrigerant must always be charged upstream of the accumulator heat exchanger, to
ensure the compressor is protected from liquid refrigerant slugging.
3.4 FINAL OPERATING CHARGE
The refrigerant charge should be fine-tuned for the best operating efficiency of the cooling system. The exact
charge will vary, depending on the evaporator size and the refrigerant line length.
1. With the milk cooler’s evaporator covered with milk/water or the chilled solution circulating through
the chiller, operate the cooler or chiller with the startup refrigerant charge until the product is cooled to a
temperature below 45°F (7.2°C).
2. Check the evaporator’s superheat, ensuring it is properly adjusted. The milk coolor’s evaporator superheat
should be set at 4–6°F (2.2–3.3°C), and the chiller’s evaporator superheat should be set at 10–12°F (5.6–6.7°C).
Refer to Section 5.0 for superheat adjustment.
3. Check the sight glass installed at the TEV inlet. If the sight glass shows vapor refrigerant (bubbles), go to step
4. If the sight glass is clear with liquid refrigerant, slowly recover refrigerant from the system at the high-side
service valve (P6), until an occasional bubble of vapor is seen in the sight glass.
4. Slowly add refrigerant at suction service valve (P2), until the sight glass becomes clear with liquid refrigerant.
5. Check the superheat a second time to ensure the proper setting.
IMPORTANT: Liquid refrigerant must always be charged upstream of the accumulator heat exchanger,
access port P2, to ensure the compressor is protected against liquid refrigerant slugging.
3.6 REFRIGERANT TESTING
When removing refrigerant from a system that has had a compressor failure, the refrigerant should be tested for
acid to ensure that it has not been contaminated by a burnout. If any contamination is found, recover the entire
refrigerant charge, replace the filter drier, triple evacuate, and recharge with new or recycled refrigerant to meet
ARI 700-88 specifications.
3.7
SAFETY ALERT
Technicians should wear side-shielded safety glasses and butyl-lined gloves when handling refrigerants.
Liquid refrigerant will cause frostbite.
When refrigerants come in contact with an open flame or a high heat source, dangerous gases will form.
This is characterized by a strong acidic odor. Immediately vacate the area and ventilate prior to reentry.
7
!