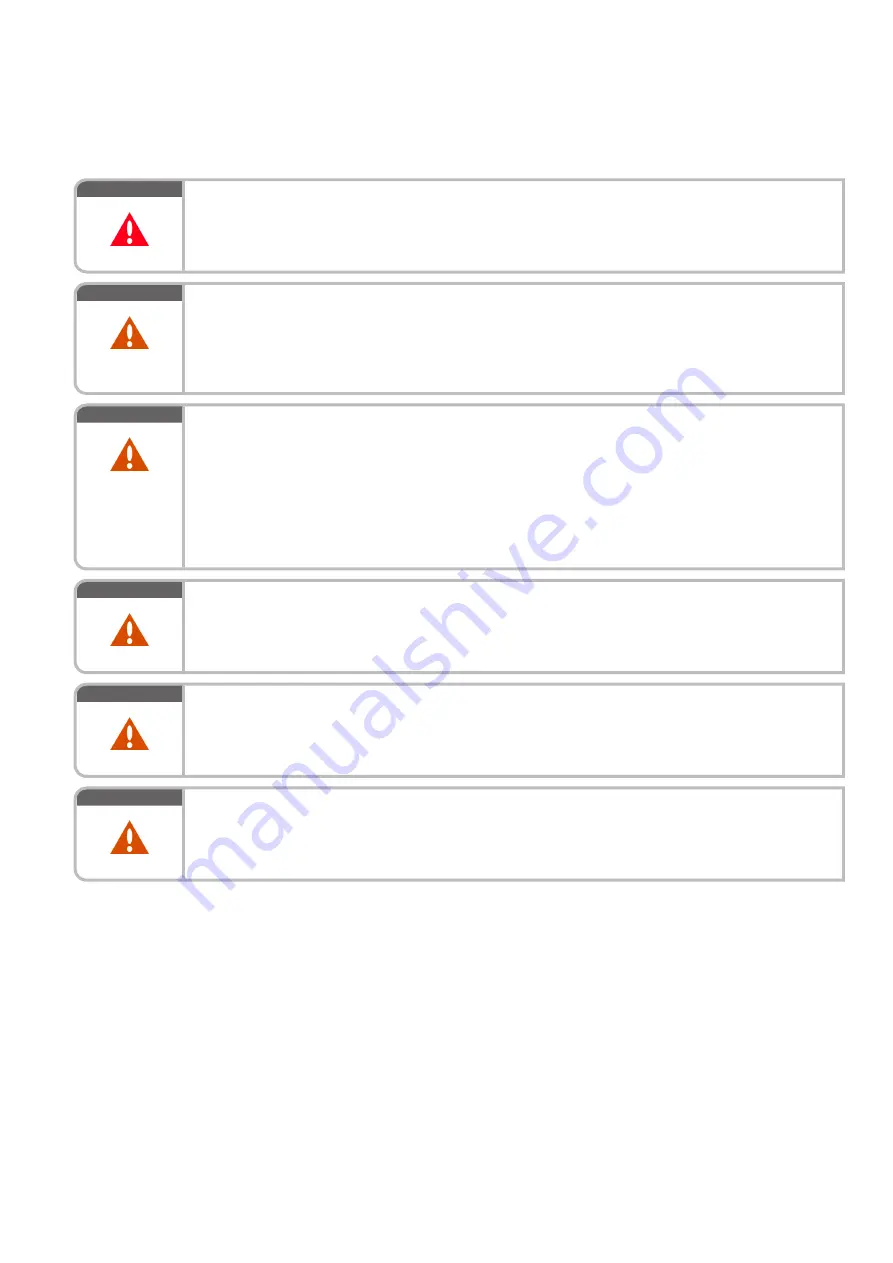
8.8.4 Fuel prefilter (switchable) – Draining
DANGER
Components are moving or rotating.
Risk of crushing, danger of parts of the body being caught or pulled in!
• Operate the engine at low load only. Keep clear of the danger zone of the engine.
WARNING
Fuels are combustible and explosive.
Risk of fire and explosion!
• Avoid open flames, electrical sparks and ignition sources.
• Do not smoke.
• Wear protective clothing, protective gloves, and safety glasses / facial protection.
WARNING
Liquid or gaseous media, e.g. fuel, are poisonous.
Escaping vapors of highly volatile media, e.g. fuel or ether.
Risk of fatal injury through swallowing; risk of poisoning through inhalation; irritation to eyes
and skin!
• Seek medical attention immediately; do not induce vomiting.
• Do not inhale vapors or mist.
• Wear protective clothing, protective gloves, and safety glasses.
• If contact is made with skin, wash off with water and soap.
WARNING
Exhaust gases are harmful to health and may cause cancer.
Risk of poisoning and suffocation!
• Keep the engine room well-ventilated at all times.
• Repair leaking exhaust pipework immediately.
WARNING
High level of engine noise when the engine is running.
Risk of damage to hearing!
• Wear ear protectors.
WARNING
Fuel in the prefilter can be pressurized.
Risk of injury through spraying fuel!
• Wear protective gloves and eye protectors/safety mask.
• Open screw-coupling slowly.
Preparatory steps
u
Pressure ratios in the fuel prefilter, see (→ Page 148).
• In case of low pressure, drain fuel prefilter according to version A, see (→ Page 145).
• In case of high pressure, drain fuel prefilter according to version B, see (→ Page 147).
Draining fuel prefilter with low pressure, version A
Note:
•
During engine operation, only the cut-out filter module must be drained!
•
At engine standstill, both filter modules can be drained!
1.
Provide a suitable container to collect the water.
MS15054/03E 2018-07
| Fuel Filter | 145
TIM-ID: 0000066393 - 005