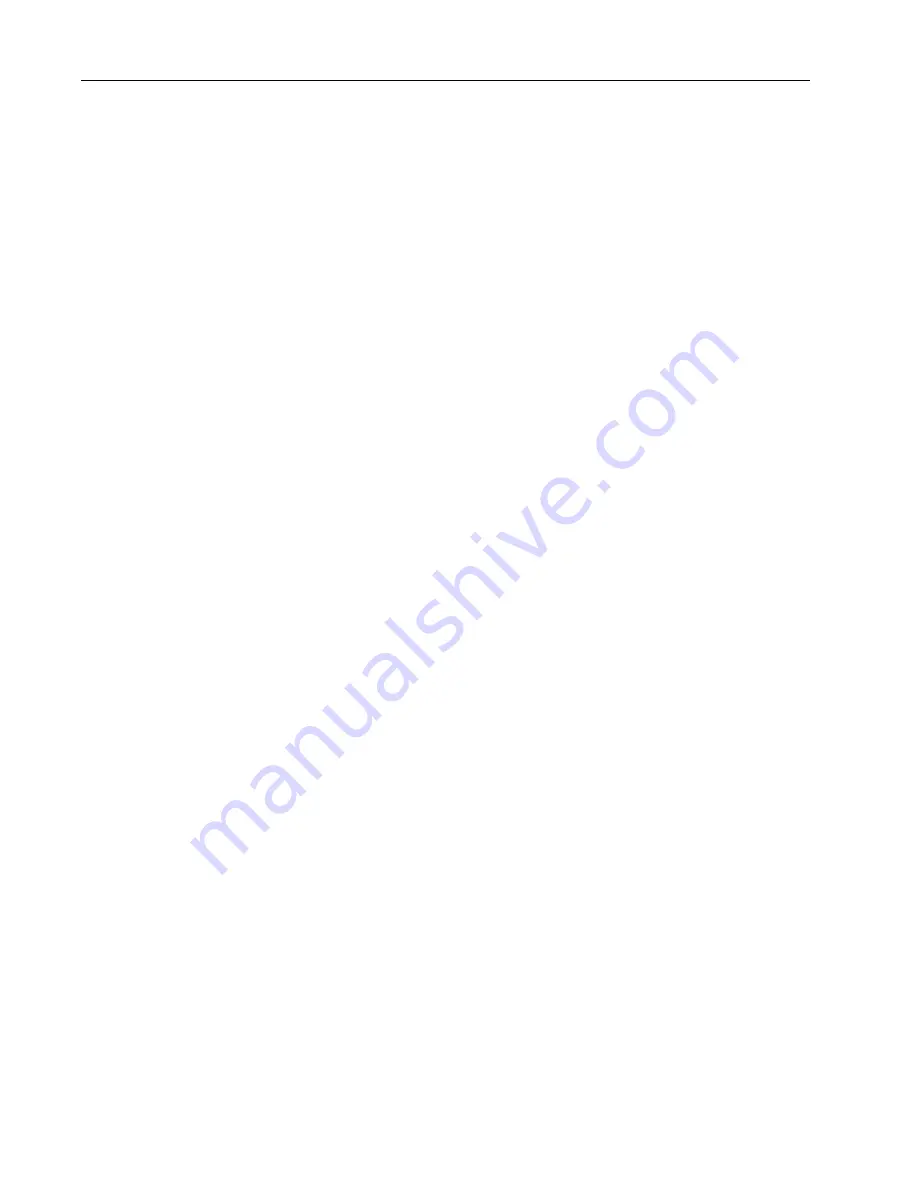
Section
140 • 180
Page 501
Dated
October 2011
140 • 180 SERIES
1.
General Instructions
HORIZONTAL FLEXIBLE COUPLED
PUMPS
A.
Inspection of Equipment
B.
Storage
C.
Placing Stored Pumps Into Service
D.
Application Considerations
E.
Recommended Spare Parts
When properly installed and given
reasonable care and maintenance,
regenerative turbine pumps should
operate satisfactorily for many years.
Because of the high differential
pressures expected in a regenerative
turbine pump, close running clearances
are used to reduce internal losses.
Abrasive particles, even microscopic
ones, in high enough concentrations,
can open up the close clearances
between internal components. For
critical services it is recommended that
you keep an identical pump for stand-by
use.
1A Inspection of Equipment
Immediately upon receipt of the
shipment, inspect the equipment for
damage or missing components.
Check the shipping manifest and
report any damage or shortage to the
Transportation Company’s local agent.
Inspect the crate and any wrapping
material before discarding. Parts or
accessories are sometimes wrapped
individually or fastened to the skid.
Put the instructions that came with the
shipment in a safe place where they will
be available to those who will be using
them for installation and service.
1B Storage
If the pump is to be stored before use,
it should be inspected as described
in 1A, recrated and stored in a dry
location. Standard shipping containers
are not suitable for outdoor storage.
In some areas, it may be necessary
to cover the pump’s exterior surface
with oil or other rust inhibiting coating.
All units are tested at the factory with
a water/corrosion inhibitor solution,
some of which will remain inside the
pump upon receipt. If units are flushed
out prior to storage, this inhibitor will
be removed and proper care must be
taken to prevent product deterioration
from improper storage.
For storage beyond 30 days, a
corrosion inhibiting protective fluid
should be added to the internal pump
cavities. Fluids used in the pump should
be selected for compatibility with pump
materials. This is very important when
optional seal and gasket materials have
been used. Protective caps on the inlet
and outlets should also be used. Caps
alone are not sufficient protection.
1C Placing Stored Pumps Into
Service
Special care must be taken when
placing stored pumps into service. First
clean the outside and flush out the
inside with a process compatible fluid.
Try to turn the pump using the coupling.
Applying torque to the motor fan blades
is not recommended. If the impeller
does not break loose immediately, fill
the pump with a process compatible
fluid and try again in a few hours.
If this fails, read the disassembly-
reassembly instructions. With an
understanding of which are the bolts
used to clamp the entire assembly
together, loosen each of them exactly
three full turns. After filling the pump
with water again, up to 50 foot pounds
of torque may be applied to the coupling
without fear of ruining the impeller
vanes. It should begin to turn well
before this force is reached. Continue
turning the pump while the various
fasteners are returned to their original
positions.
If the unit still won’t turn over, DO
NOT apply further force. Refer to the
Disassembly/Reassembly Instructions
in Section 5 to determine the cause of
the problem.
1D Application Considerations
1D1 Electrical Wiring
All electrical equipment and wiring
should conform to local and National
Electrical Codes. Use the motor
manufacturer’s instructions for
connecting the motor. Note the correct
rotation and wiring diagrams on the
assembly. Make sure the motor rotation
and speed matches that required for the
pump.
1D2 Construction Materials
Wile it is reasonable to assume that
good judgement has been used in
selecting all the materials in the pump
for compatibility with process fluids,
actual conditions sometimes vary from
original specifications. Also, typical
material selection charts do not consider
all the temperature, pressure, and fluid
variables. The customer’s engineer
should be consulted for final judgement
on the best materials for critical process
applications.
1D3 Valves
The first valve to be considered for a
regenerative turbine pumping system
should be a pressure relief valve.
Because this type of pump has a
horsepower requirement similar to
that of a positive displacement pump,
constantly rising hp as pressure
increases, a relief valve can be
effectively used to limit horsepower.
This is helpful when a non-overloading
motor is specified. It can be of
critical importance if the system flow
rate can vary widely.
There are
almost no circumstances where
a flow modulating valve will work
successfully in a regenerative
turbine pumping system. The steep
pumping characteristic, typical
of these pumps, produces very
large pressure changes with small
variations in flow rate. As a result,
the modulating flow from the valve
introduces sharp pressure shock
waves that shorten pump life and
may cause damage to other pieces
of equipment in the system.
A swing check valve is recommended
in the suction line even when the pump
inlet is only slightly higher than the fluid
source. It should be the same size
as the pump inlet or sized based on
reasonable fluid friction losses.
A foot valve is recommended when
lifting fluid from a sump. This will save
wear and tear on any pump, even those
equipped with self- priming capability.
A Y-Strainer is recommended
immediately ahead of the pump on
any newly constructed system. This
is advisable due to the probability
that foreign material large enough to
damage pump clearances may remain,
even though the piping has been
flushed.
Valves in the outlet piping of a
regenerative turbine pump should
always be open as far as possible when
the pump is started. This will reduce the
start-up load on the pump and motor.