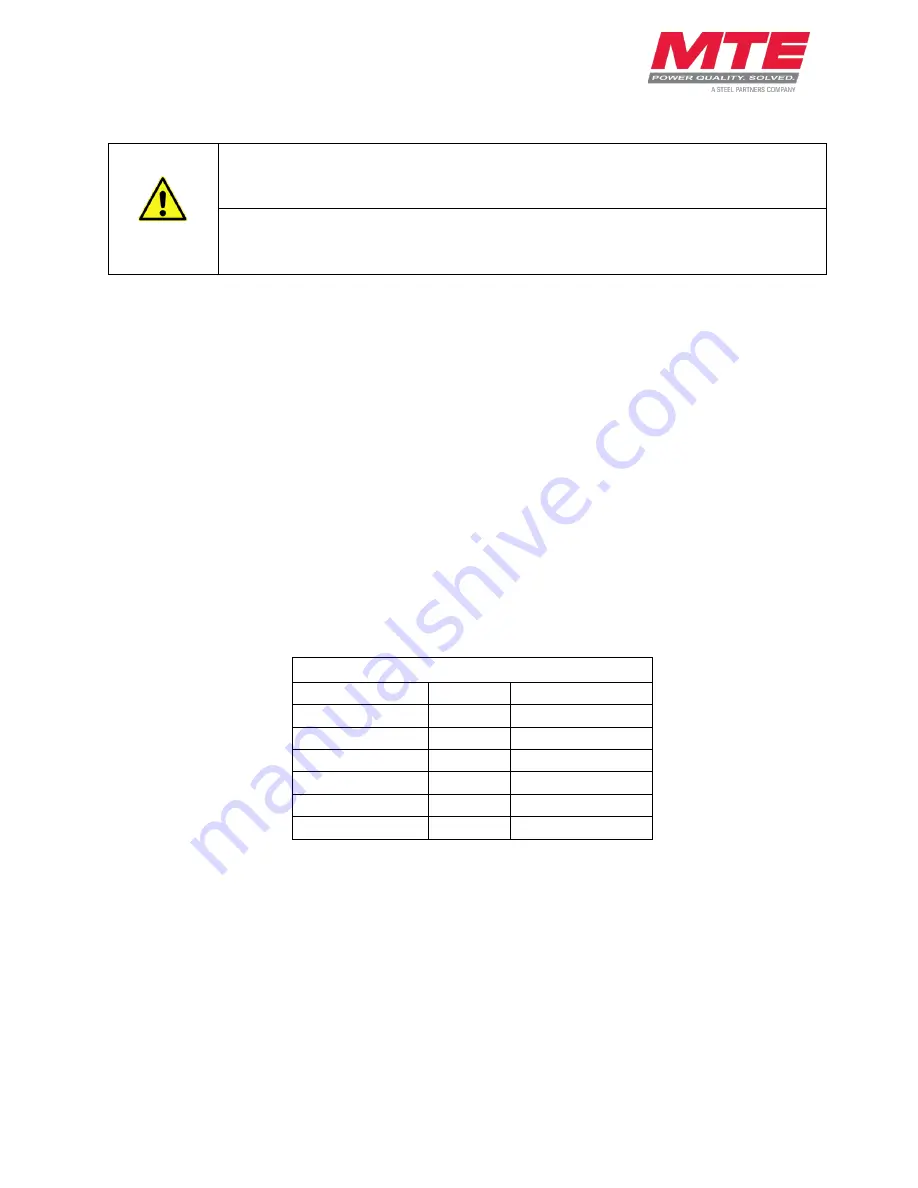
SineWave Nexus™ Technical Reference Manual 380V - 600V
Form: SWN-TRM-E February 2020 REV. 001
18
Grounding
NOTE: For cable shield grounding follow the drive manufacturer’s recommendations.
Grounding and Ground Fault Protection
Due to high leakage currents associated with variable frequency drives, ground fault protective
devices do not necessarily operate correctly. When using this type of device, its function should be
tested in the actual installation.
Overtemperature Interlock
An overtemperature interlock circuit should be used in conjunction with thermal switch to turn off the
drive to prevent filter damage due to abnormal operating conditions. The temperature switch is
normally closed and will open when an internal reactor temperature of 180°C is reached. See Table
5-1: Overtemperature Switch, below for contact rating information and the drive user manual for
interconnection information.
Table 5-1: Overtemperature Switch
NC Switch
opens at 180 Deg. +/- 5 Deg. C
Current Amps
Voltage
Contact Load
6
120 AC
Resistive Loads
3
120 AC
Inductive Loads
3
240 AC
Resistive Loads
2.5
240 AC
Inductive Loads
8
12 VDC
Resistive Loads
4
24 VDC
Resistive Loads
MTE highly recommends the use of the overtemperature switch to prevent damage to the filter in
rare instances of overheating from abnormal operating conditions.
WARNING
The filter must always be grounded with a grounding conductor connected to ground
terminals.
For modular units, ensure a 2” X 2” area is cleaned of paint and varnish on lower
mounting bracket for ground connection.