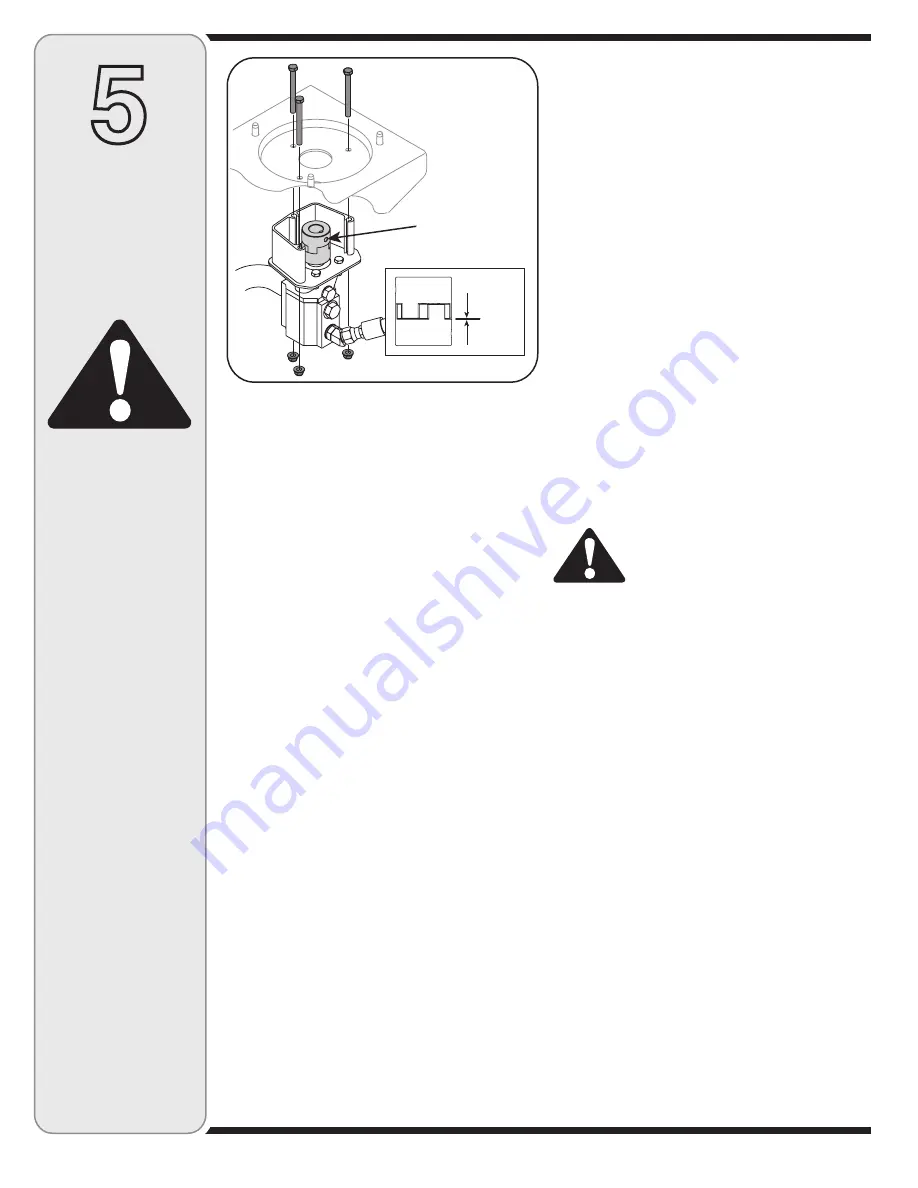
14
6. Install pump coupling half and key on pump shaft.
Rotate coupling half until set screw faces opening in
shield. Do not tighten set screw.
7. Install nylon “spider” onto engine coupling half.
8. Align pump coupling half with nylon “spider” by rotat-
ing engine using starter handle. Slide coupling half
into place while guiding three mounting bolts through
holes in pump support bracket.
9. Secure with nuts removed earlier.
10. Set.010” to.060” clearance/gap between the nylon
“spider” and the engine coupling half by sliding a
feeler gauge or matchbook cover between the nylon
“spider” and the engine coupling half and moving
pump coupling half as needed. Secure pump coupling
half with set screw. See Figure 5-3.
NOTE
: Make certain proper clearance/gap is obtained
before tightening set screw.
Tires
See sidewall of tire for recommended pressure. Under
any circumstances do not exceed manufacturer’s recom-
mended psi. Maintain equal pressure on all tires.
WARNING: Excessive pressure when
seating beads may cause tire/rim as-
sembly to burst with force sufficient to
cause serious injury. Refer to sidewall
of tire for recommended pressure.
WARNING
Figure 5-3
5
Maintaining
Your Log
Splitter
IMPORTANT
: Never hit the engine shaft in any manner,
as a blow will cause permanent damage to the engine.
1. Remove three nuts that secure the pump to the
coupling shield. Two nuts are at the bottom corners
and one is in the top center. See Figure 5-3.
2. Remove the pump.
3. Rotate the engine by slowly pulling starter handle
until engine coupling half set screw is visible. Loosen
set screw using allen wrench and slide coupling half
off engine shaft.
4. Loosen set screw on pump coupling half and remove
coupling half.
5. Slide new engine coupling half onto the engine
shaft until the end of the shaft is flush with the inner
portion of the coupling half. (There must be space
between the end of the engine support bracket and
coupling half). Tighten set screw.
Excessive pressure
when seating beads
may cause tire/rim
assembly to burst
with force sufficient to
cause serious injury.
Refer to sidewall of
tire for recommended
pressure.
.0600
.0100
Side View-Coupler
Set Screw