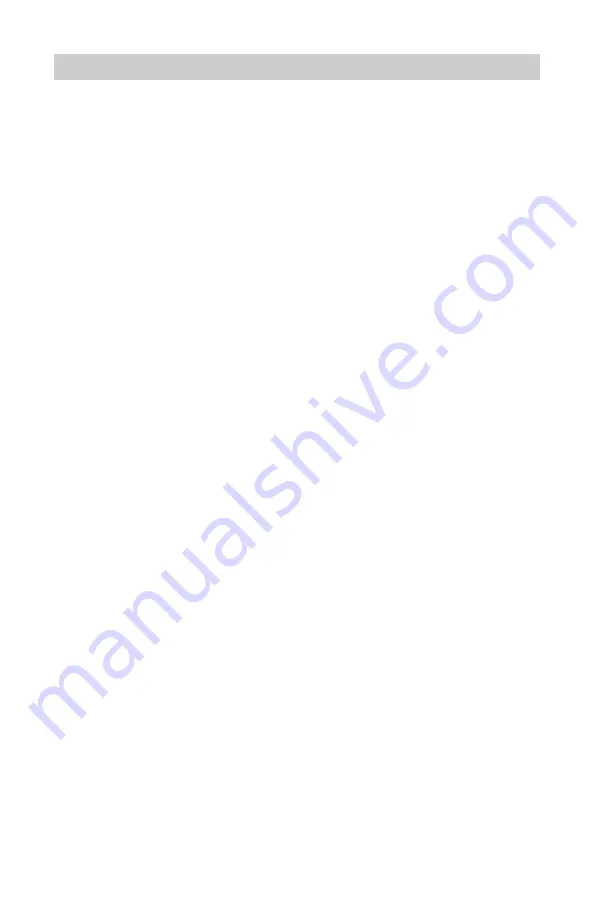
© 2001, Rose Manufacturing Company
Page 13
User Instructions
!
FP Pro Vest Style Harness
P/N 623244, Rev. D
12.0 FORMAL INSPECTION
12.1 FORMAL INSPECTION FREQUENCY
The FP Pro Harness must be formally inspected by a competent person other than the user at intervals of
no more than six months. (The qualifications of a competent person are established by OSHA.) If the harness
is exposed to severe working conditions, more frequent formal inspections may be required. The frequency
of inspection by a competent person should be established by the user’s organization based on such factors
as the nature and severity of workplace conditions, modes of use, and exposure time of the equipment. The
competent person should perform a methodical and thorough visual and tactile inspection by following the
inspection procedure in section 12.3. The inspection results should be recorded in the Formal Inspection Log
and retained for reference. In addition, if the harness passes Formal Inspection, the competent person should
punch the date (month / year) of Formal Inspection on the grid supplied with the labels on each harness. The
user should never punch this grid; however, the user should check it before each use to be sure a Formal
Inspection has been performed within the last six months.
12.2 CONTROL OF EQUIPMENT
The user’s organization should establish and enforce a policy and procedure whereby any harness that is
found to be defective, damaged, or in need of maintenance be immediately removed from use, marked as
“UNUSABLE” and immediately thereafter submitted to custody of the competent person responsible for
Formal Inspection. This has the benefits that: 1) defective equipment is secured from further use until proper
action is taken; 2) uniform standards are applied for determining whether the equipment is acceptable or not
acceptable for further use; 3) uniform methods of cleaning and other maintenance are applied; and 4) there
is a central point for evaluation of conditions that may be recurring and require preventive measures such
as coordination with the equipment manufacturer, selection of alternate equipment, additional training of
equipment users, or changes to the workplace conditions.
12.3 FORMAL INSPECTION PROCEDURE
The Formal Inspection Procedure is similar to the user’s inspection before each use described in section 11.
However, it differs in three important respects: (1) its performed by a competent person – other than the user
– who is trained and authorized to perform Formal Inspection for the user’s organization. (2) Its more detailed
and methodically recorded on a Formal Inspection Log kept on file for future reference. (3) It results in final
disposition of the equipment as either “acceptable” (indicated by the formal inspector punching the current
month/year in the Formal Inspection Grid on one of the product labels) or as “not acceptable,” followed by
destruction of the product. The described inspection record-keeping is needed in order to trace detected
defects to their causes.
Step 1
Record on the Log the Model Number, Serial Number and Date Made information shown of the
harness identification label. Record the inspector’s name and inspection date.
Step 2
Arrange the harness so the parts to be inspected are readily visible.
Step 3
Starting with the webbing category of parts shown on the Log, inspect each part (inspection
point) one at a time. Refer to the diagram for identification of each Inspection Point. Determine
whether the part (inspection point) is acceptable or not. Enter “Fail” if a defective condition exists.
Relevant comments on the condition may also be added for reference. If there is a question
whether the harness condition has materially changed since the last Formal Inspection, retrieve
and review prior Formal Inspection records for the specific harness.
Step 4
Repeat steps 2 and 3 for the stitching, metallic and plastic categories of part types.
Step 5
Determine disposition of the harness. If in step 5 it has been determined that the harness is not
acceptable, enter “Fail” in the Disposition space on the Log. In addition, a notation should be
made in this space as to whether the harness is to be destroyed, returned, etc.