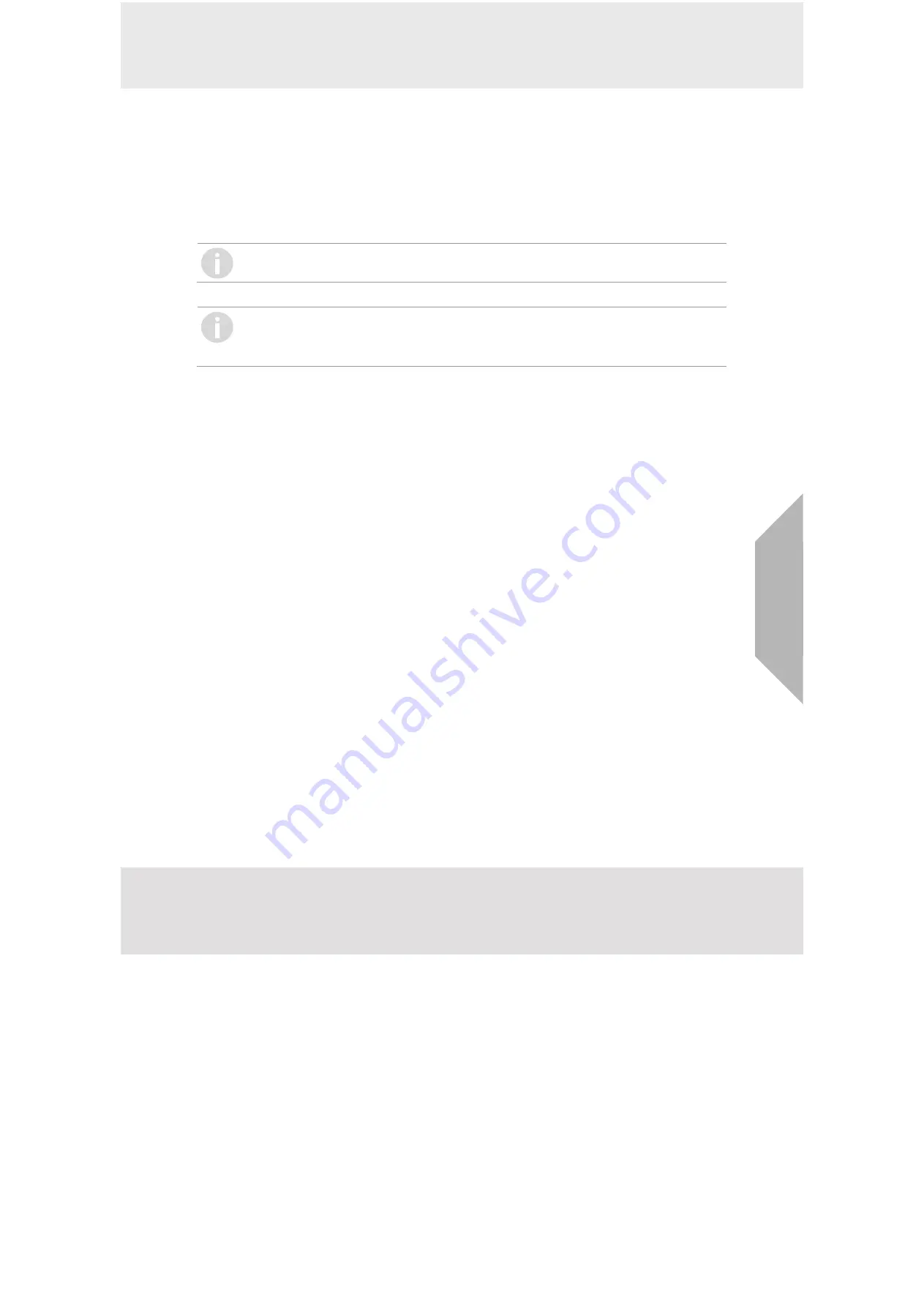
Maintenance and Cleaning
AirXpress One/AirXpress 2 Fire
25
GB
GB
Maintenance for the reducer
4.4.
Alarm whistle
(1)
Please check the warning device according to chapter 3.6.
High pressure seal ring
(1)
Check the seal ring between reducer and cylinder.
(2)
Change the seal ring if it’s damaged.
At least replace the seal ring once every year
Overhaul inspection
An overhaul inspection to the reducer and demand valve must be made every 9 years. This must be
done by the manufacturer or an authorized test center. During overall inspection, all the rubber parts
and all parts found with wearing or cracks must be replaced. A readjustment and lead seal should be
made after replacement.
Maintenance for the high and medium pressure hose
4.5.
User must pay attention to connections and surrounding areas and check if performance of high and medium pressure
hose is loss because of normal aging, improper working conditions, wrong operations or accident.
There are 2 different medium pressure hose: the medium pressure hose directly connected to reducer and demand
valve, and the medium pressure hose connected the reducer and demand valve with a coupling (Please refer to the
pneumatics system picture, Fig. 2 to Fig. 6).
Maintenance
(1)
Check the line for holes, splits, tearing or burst of reinforced layers, and crack of rubber.
(2)
Check the line for partial deformations, air bubbles and bulge under pressure.
(3)
Check if the line is soft or sticky.
(4)
If any of this defects appear stop to use the line.
Leak test
(1)
Open cylinder valve.
The cylinder pressure should be more than 270 bar.
(2)
Turn off cylinder valve.
The pressure should decrease less than 10 bar in a minute.