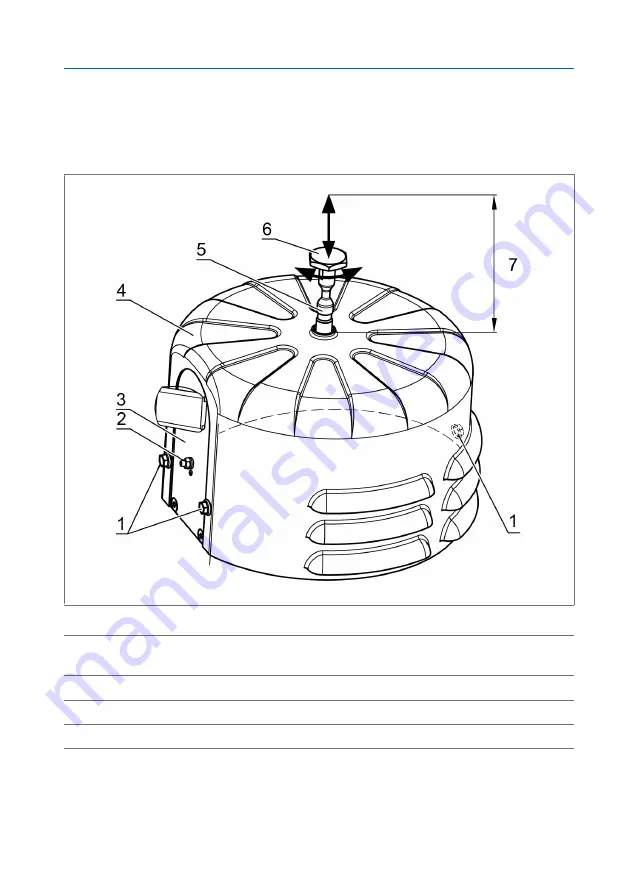
5 Mounting
27
BA5789879-01 EN
5.1 Mounting pressure relief device with standard protective
cover
In order to mount the device, you must open it. Only close it again once
mounted.
Figure 5: Mounting pressure relief device with standard protective cover
1 3 hexagon screws M6x10, wrench
size 10
2 Ground connection (only with plug
connection)
3 Stand plate
4 Protective cover
5 Signal pin, wrench size 12
6 Signal pin cap, wrench size 32
7 Clearance above: min. 100 mm [4"] / with semaphore 170 mm [6.7"]
Summary of Contents for MESSKO MPREC
Page 1: ...Pressure Relief Device MESSKO MPREC Operating Instructions BA5789879 01 EN ...
Page 58: ......
Page 59: ......