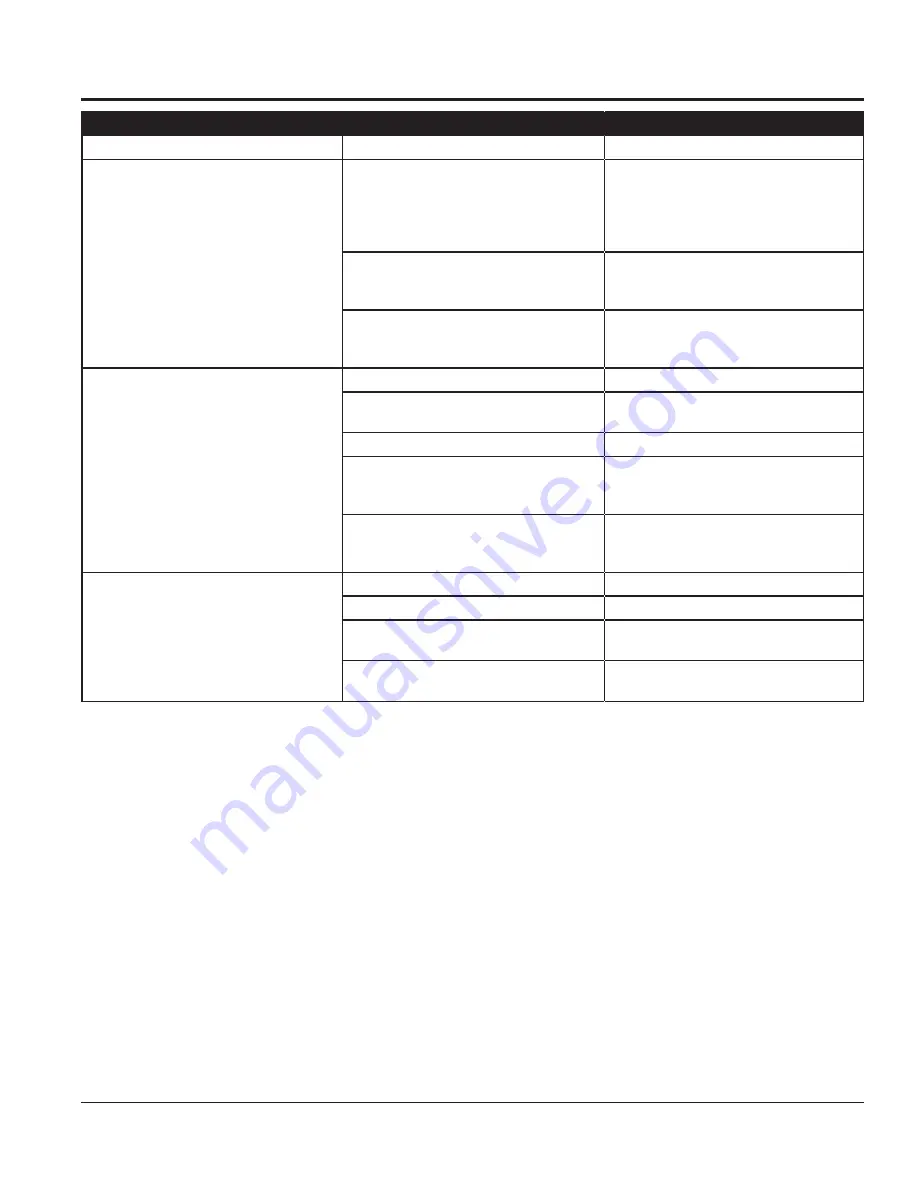
HDA SERIES WALK-BEHIND TROWEL • OPERATION MANUAL — REV. #0 (12/1/17) — PAGE 45
TROWEL TROUBLESHOOTING
Troubleshooting (Walk-Behind Trowel) - continued
Symptom
Possible Problem
Solution
Machine has a perceptible rolling motion
while running.
Main shaft?
The main output shaft of the gearbox
assembly should be checked for straightness.
The main shaft must run straight and cannot
be more than 0.003"" (0.08 mm) out of round
at the spider attachment point.
Yoke?
Check to make sure that both fi ngers of the
yoke press evenly on the wear cap. Replace
yoke as necessary.
Blade Pitch?
Check to ensure that each blade is adjusted
to have the same pitch as all other blades.
Adjust per maintenance section in manual.
Clutch slipping or sluggish response to
engine speed change.
Worn V-belts?
Replace V-belt.
Hand clutch out of adjustment?
Adjust per instructions in maintenance
section of this manual.
Worn or defective hand clutch parts?
Replace parts as necessary.
Worn bearings in gearbox?
Rotate input shaft by hand. If shaft rotates
with diffi culty, check the input and output
shaft bearings. Replace as necessary.
Worn or broken gears in gearbox?
Verify that the gearbox shaft rotates when
the input shaft is rotated. Replace both the
worm and worm gear as a set.
Trowel blades do not rotate.
Defective clutch?
Replace clutch.
Broken V-belt?
Replace V-belt.
Defective ON/OFF switch?
Check and replace ON/OFF switch if
necessary.
Defective centrifugal ON/OFF switch?
Check and replace centrifugal ON/OFF
switch if necessary.