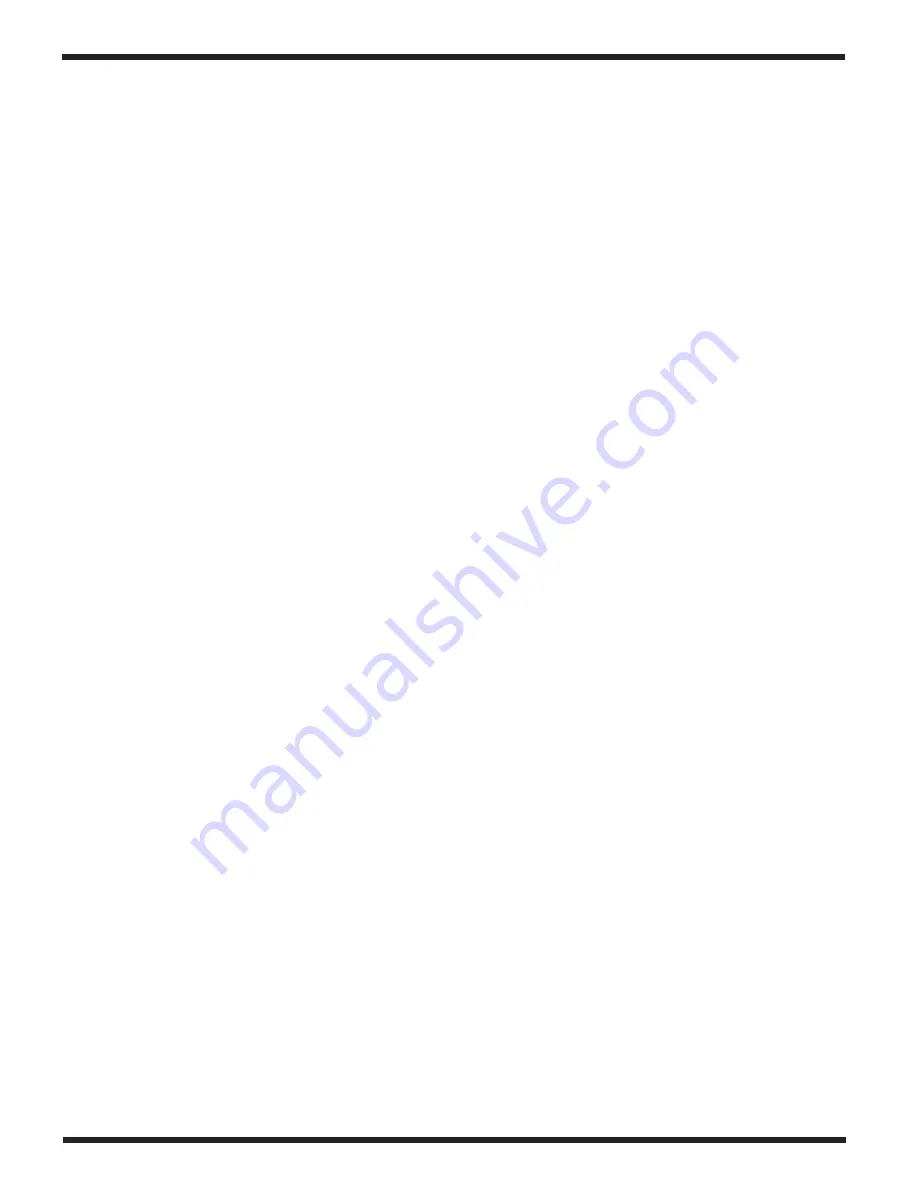
10
CONDITION
CAUSE
SOLUTION
Insufficient pumped spray
Clogged pump intake screen ............ Clean
pressure
Clogged spray pipe .......................... Clean
Scrap screen full ............................... Must be kept clean and in place
Low water level in tank .................... Check drain and overflow tube
Defective pump seal ......................... Contact service agent
Insufficient final rinse or no
Faulty pressure reducing valve ........ Clean or replace
final rinse
Improper setting on pressure
reducing valve .................................. Set flow pressure to 20-22 psi [138-151kPa]
Clogged rinse nozzle and/or
pipe ................................................... Clean with paper clip/delime
Improper water line size ................... Have installer change to proper size
Rinse cycle too short ........................ Check timer
Low final rinse temperature
Low incoming water ........................ Check the booster be sure the thermostat is set to maintain
180°F/82°C temperature. Check incoming water is set min.
140°F/60°C.
Check valve to be sure it is clean
and operating.
Defective thermometer ..................... Check for proper setting or replace
Defective thermostat ........................ Replace
Bad booster element ......................... Contact your service agency
High limit tripped ............................. Reset
Machine leaking
Leaking at chemical injector ............ Check or replace injector
Leaking at chemical hose ................. Replace hoses
Pump seal leaking ............................ Replace seal
Leaking at pump hose ...................... Contact your service agency
Water splashing out door
Nozzles/End caps missing ................ Replace caps
Wash nozzles blocked ...................... Clean
Arms not rotating ............................. Replace bearings
Door handle twisted (pass through) . Adjust or replace handle
Poor washing results
Detergent dispenser not
operating properly ............................ Contact detergent supplier
Insufficient detergents ...................... Contact detergent supplier
Food Soil concentration too
high in wash tank ............................. Drain tank, clean and refill every 2 hours of
operation or after each meal period.
Wash water temperature
too low .............................................. See condition “Wash Tank
Water Temperature” above
Wash arm clogged ............................ Clean
Improperly scraped dishes ............... Check scraping procedures
Ware improperly
placed in rack ................................... Use proper racks. Do not overload racks
Improperly cleaned
equipment ......................................... Unclog wash sprays and rinse nozzles
to maintain proper pressure and flow
conditions. Overflows must be open.
Keep wash water as clean as possible.
Electric elements
has soil/lime buildup ........................ Clean and delime
TROUBLESHOOTING
TROUBLESHOOTING (CONT.)