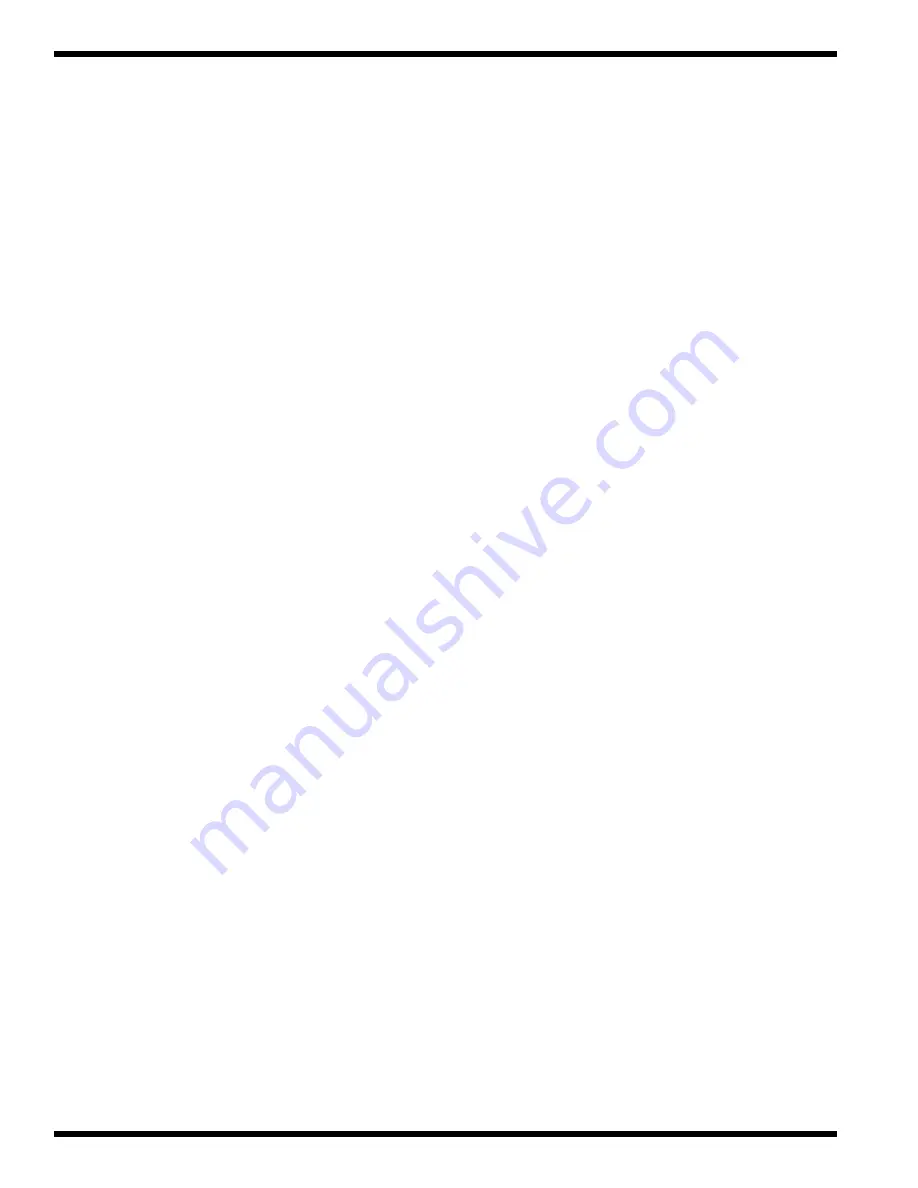
10
MAINTENANCE
MAINTENANCE
The efficiency and life of your machine is increased by regularly scheduled preventive
maintenance. A well maintained machine gives better results and service. An investment of a few
minutes of daily maintenance will be worthwhile.
The best maintenance you can provide is to keep your machine clean. Components that are not
regularly cleaned and flushed will clog and become inoperative.
Intervals shown in the following schedules represent an average length of time between necessary
maintenance. Maintenance intervals should be shortened whenever your machine is faced with
abnormal working conditions, hard water, or multiple shift operations.
Cleaning Schedule
•
Daily-Every 8 Hours
1. Depress
the
ON/FILL/OFF/DRAIN
switch to
OFF/DRAIN
position and close and
latch the door to drain the tank.
2.
Open the door and remove the upper and lower spray arms by unscrewing the knurled
fastener.
3.
Remove the scrap screen carefully to keep soil or waste particles from falling into the
sump. Remove any material caught in pump intake.
4.
Clean inside the tank with clean water. Backflush the scrap screen until it is clean. Do
not strike the screen against solid objects.
5.
Clean the wash arms to remove any debris from spray openings. Do not strike the
spray arms against solid objects.
6.
Reinstall the scrap screen and spray arms.
7.
Leave the door open overnight to allow drying.
8.
Report any unusual conditions to your supervisor.
•
Meal Periods
1.
Clean the scrap screen after every meal period and more frequently during heavy
usage. Do not allow the scrap screen to become clogged with soil or waste particles.
Summary of Contents for 401-HTM2 PLUS
Page 4: ...THIS PAGE INTENTIONALLY LEFT BLANK ...
Page 20: ...THIS PAGE INTENTIONALLY LEFT BLANK ...
Page 21: ...15 REPLACEMENT PARTS REPLACEMENT PARTS ...
Page 22: ...16 REPLACEMENT PARTS 12 12 12 11 10 00050 9 6 5 4 3 7 2 1 8 Figure 1 Track and Panel Assembly ...
Page 44: ...38 THIS PAGE INTENTIONALLY LEFT BLANK ...
Page 45: ...39 ELECTRICAL SCHEMATICS ELECTRICAL SCHEMATICS ...
Page 51: ......