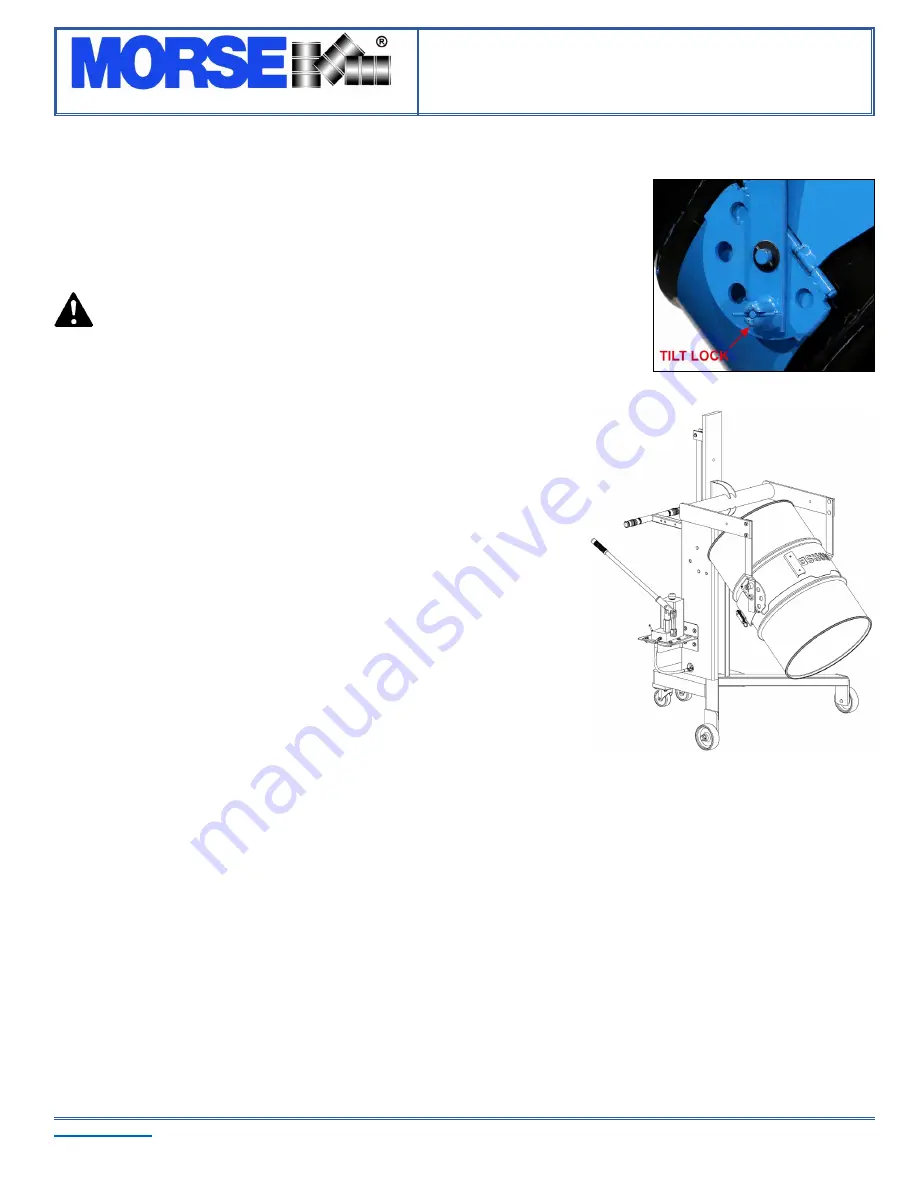
The Specialist In Drum Handling Equipment
Model 82A
Mobile-Karrier / Palletizer
Operator’s Manual for Model 82A Morse Mobile-Karrier / Palletizer
Serial Number 1016 to 0118 (MMYY)
morsedrum.com
Copyright 2022 - Morse Mfg. Co., Inc.
Form OM82A (1016-0118)
(Updated 14, Jul., 2022)
5
4. Either one of the two spring loaded plunger tilt locks (Figure 4.4) may be locked
to hold drum upright. Unlocking both will permit drum to be tilted. Drum pouring
angle may be varied or drum can be locked in various positions by inserting
one tilt lock. It is not necessary to lock both tilt locks. Before unlocking tilt lock it
is recommended that you steady drum and prepare to resist its tendency to tilt
toward its heavy end.
WARNING:
Keep hands and fingers clear of tilt lock holes, as a pinch
point will occur when drum rotates.
5. With tilt-locks unlocked, manually tilt the drum for pouring (Figure 4.5). The drum
pouring angle may be varied or it can be locked in various positions by one of the
tilt-locks.
6. After emptying, rotate drum back to vertical position and lower.
7. Before unloading drum, release tilt locks and return drum to upright. Lower drum
at a controlled rate.
8. To remove drum: Squeeze the ratchet release lever and open all the way to
unlock. Then release the tension on the strap. Allow enough slack in order to
remove strap loop from clevis. Swing both hinged bands to open position. Pull
unit away and park on level floor, out of traffic lanes when not in use.
9.
Adjustment for Shorter Drums: The drum holder assembly is factory set in
position for handling typical 55-gallon (210 liter) drums. For handling shorter
drums such as typical 30-gallon (114 liter) drums, relocate drum holder assembly
downward as follows: Detach by removing nuts that hold it to lifting assembly.
Reattach at alternate location 6” lower.
Figure 4.4
Maintenance
Periodic inspection for the general condition of structural and mechanical components is imperative for safe and efficient operation.
•
Periodically inspect all moving parts, framework, and contact areas for signs of wear, fatigue, or loosening. Tighten, adjust, or
replace parts as necessary to prevent failure and maintain proper function.
•
Inspect the hydraulic system for oil drips, hose damage, or other signs of wear. Inspect the level and condition of the hydraulic fluid.
Replace any parts that show signs of wear.
•
Grease wheel bearings periodically. Oil or grease all moving parts including: Tilt locks, fulcrum shafts, hinge pins, and the ratchet.
•
Worn or damaged parts must be properly replaced with the correct, genuine Morse parts.
•
Hydraulic pump is shipped filled with Noco Premium plus automatic transmission fluid d/m. Material safety data sheet (msds) is
available online. Change oil yearly, sooner depending on dirty conditions or outdoor use. Replace oil with Mobil dte 24 or equivalent
for indoor use (Mobil dte 13 for outdoor use).
•
The web strap should be removed from service or replaced if any of the following are visible:
•
Acid or caustic burns
•
Melting or charring of any part of the strap
•
Holes, tears, cuts, snags or embedded articles
•
Broken or worn stitching in load bearing splices
•
Excessive abrasive wear
Figure 4.5