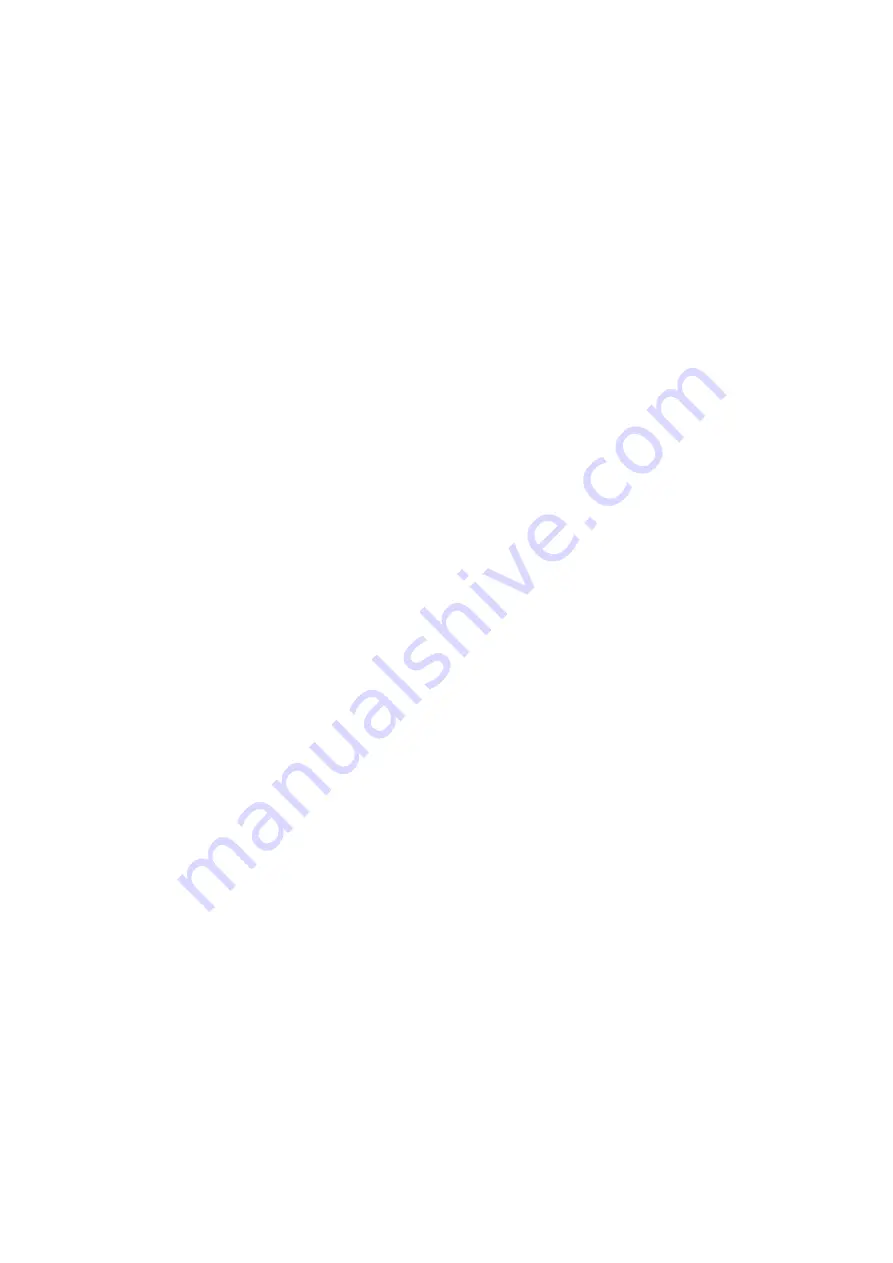
9 P-
I
selection
For position closed loops, initially select only P (SW6:2). For
pressure or velocity loops select
I
(SW6:4) initially and then P.
See paragraph 12 below for more detail. For a complete
discussion of P and
I
control, see the G122-202 servoamplifier
Application Notes (part no C31015).
10 Integrator input
The servoamplifier has a unity gain input error amplifier
followed by two parallel stages, one a proportional amplifier
and the other an integrator. The outputs of these two stages
can be switched to the output power amplifier (see paragraph
7 above) which then drives the valve.
The input to the integrator stage can be switch selected
(SW4:1) from either the output of the error amplifier,
I
in = E,
or the output of the proportional stage,
I
in = P. The latter
arrangement is used in the G122-202. It is beyond the scope
of these Application Notes to detail the benefits of each
arrangement. If you have experience with the G122-202,
I
in = P would seem to be an easy choice.
11 P only gain
For position loops select only P control (SW6:2). Input a step
disturbance of 50% valve current with the step push button
(SW3). Adjust the P gain for the required stability, while
monitoring the front panel valve test point, or the feedback
signal. The gain range of the proportional amplifier can be
moved by changing the plug-in resistor R17. The value loaded
when shipped is 100k Ohms, which gives a 1 to 20 range.
Selecting 200k Ohms will give 2 to 40. The circuit will function
correctly with the value of R17 between 100k Ohms and
10M Ohms.
Note that as P gain is increased, the movement due to the step
push button decreases.
12 P and
I
gains together
If you are inexperienced with integral control the following
set-up method is a good starting point.
I
in = E: Initially select only
I
(SW6:4). Press the step push
button (SW3). Increase
I
gain until one overshoot in the
feedback signal is observed.
Next select P (SW6:2) and
I
(SW6:4) together and increase the
P gain to reduce the overshoot.
For the
I
in = E arrangement the P and
I
sequence could be
reversed. i.e.: adjust P first, followed by
I
.
I
in = P: For an
I
in = P arrangement, only the “P followed
by
I
” sequence of adjustment can be used.
For a more thorough discussion see G122-202 Application
Notes (part no C31015).
13
I
limit
The contribution from the integrator to the output amplifier
can be reduced by selecting
I
limit on (SW6:3). When this
switch is on the integrator contribution is reduced to
approximately 15% of the level when it is off. This feature is
useful in a position loop that may require integral control to
achieve the required steady state accuracy. The limited integral
control removes valve null error when the final position is
reached. It is also useful in a pressure loop to limit overshoot,
if the valve drive saturates.
14 Dither
The dither frequency is fixed at 200Hz and the level is
adjustable with the front panel pot to ±10% of valve drive,
regardless of the type and level of valve drive selected. It can
be turned on or off with ([SW1:3]). Dither is seldom needed in
a position loop but can be beneficial in pressure or velocity
loops. Increase dither until it can just be detected in the
controlled variable, such as pressure or velocity. Dither can
compromise valve life, so it should be kept to a minimum.
15 Enable
A relay on the circuit card needs to be energised to connect
the output stage to its screw terminal and to un-clamp the
integrator. The clamp prevents integrator wind-up when the
loop is not operating. Supply 24V to the appropriate terminal
to energise the relay. The enable switch ([SW1:2]) on the circuit
card can be set to permanently energise the relay and provide
a permanent enable.
16 In position
When the valve drive signal falls below ±10% of the selected
full scale signal, the “in position” signal goes true and provides
an opto-isolated current path between the + and – terminals.
This can be connected to a PLC to initiate the next step in a
control sequence. Do not apply more than 40V to the +
terminal and ensure the load on the – terminal is less than
20mA.
The “in position” signal is not relevant for a velocity loop.
17 Withdrawing the circuit card
from its case
The circuit card needs to be withdrawn from its case to set the
selector switches, change the plug-in resistors and operate the
step push button.
To do this, push one cover release tab with a pen or
screwdriver, while gently pulling on the top cover on that side.
The cover will release approximately one mm. Repeat on the
second tab on that side. Repeat on the other side and then
withdraw the cover and circuit card until the required switches
are exposed. The rigidity of the connecting wires will hold the
circuit card in position while changes are made.
Page 4 of 6: C70861 Rev E – 07.14