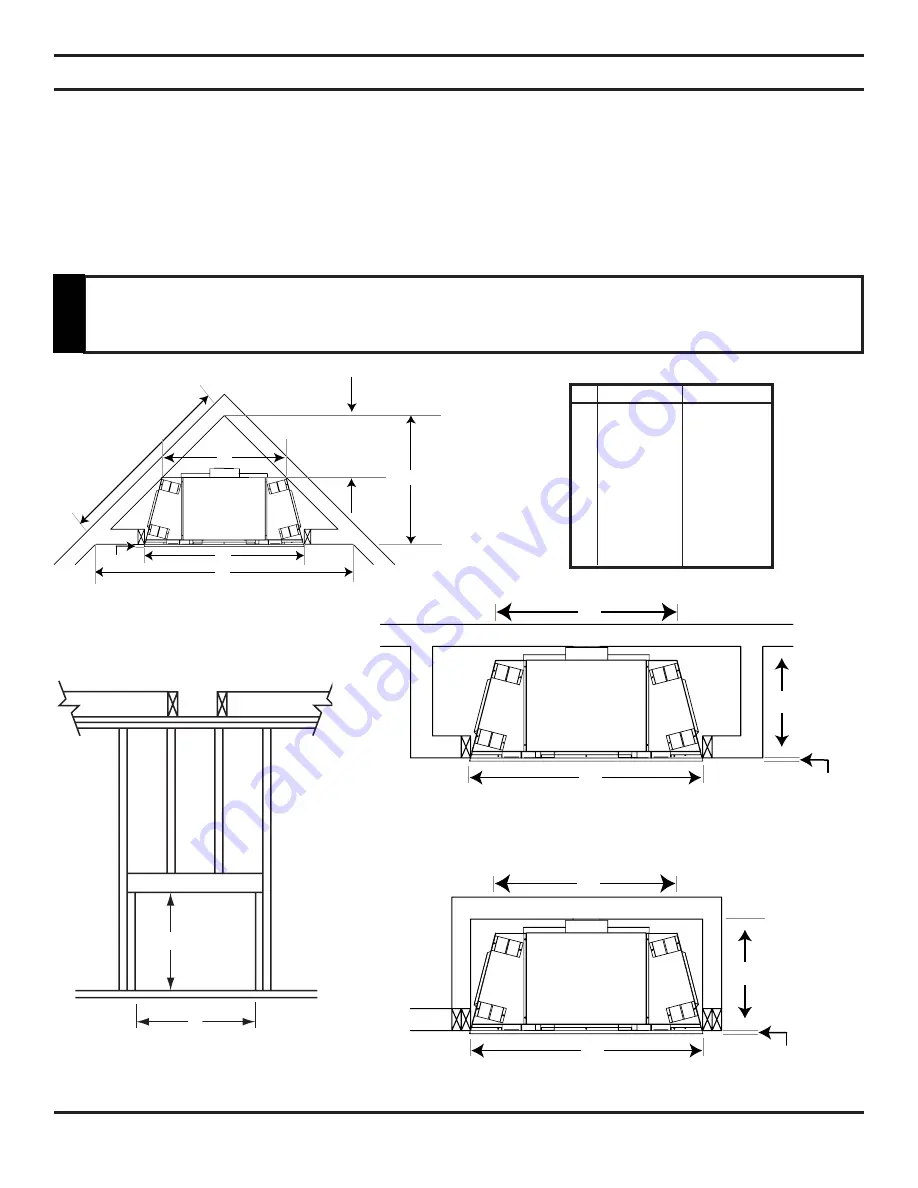
54D5031
7
B
A
D
F
H
A
E
C
1/2” or 5/8”
C
A
A
C
G
G
1/2” or 5/8”
1/2” or 5/8”
FIREPLACE FRAMING
Firebox framing can be built before or after the appliance is set in place. Construct firebox framing following Figure 2 and
the chart below for your specific installation requirements. See Figure 3 on Page 8 for firebox dimensions. The framing
headers may rest on the top of the firebox standoffs. Do not bring headers below top of standoffs.
The firebox may be installed directly on a combustible floor or raised on a platform of an appropriate height. When the
firebox is installed directly on carpeting, tile, or other combustible material, other than wood flooring, the firebox shall be
installed on a metal or wood panel extending the full width and depth of the enclosure.
Corner Installation
Stud Location
Inside Chase Installation
Figure 2 - Framing Dimensions
300 400
A
33
1
/
2
" 37
1
/
2
"
B
37
1
/
4
" 40
7
/
8
"
C
28
1
/
4
" 29
1
/
4
"
D
14
1
/
8
" 13
1
/
2
"
E
55
11
/
16
" 60
7
/
8
"
F
27
13
/
16
" 30
7
/
16
"
G
13
3
/
4
" 16
1
/
2
"
H
39
3
/
8
" 43
1
/
16
"
PRE-INSTALLATION INFORMATION
Do not
fi
ll spaces around
fi
rebox with insulation or other materials. This could cause
a
fi
re.
W
ARNING
Summary of Contents for Direct Vent Gas Fireplace HBDV300
Page 43: ...54D5031 43 1 2 3 5 6 7 10 4 9 11 REPLACEMENT PARTS FIREPLACE COMPONENTS ...
Page 51: ...54D5031 51 NOTES ...
Page 52: ...52 54D5031 NOTES ...
Page 53: ...54D5031 53 NOTES ...