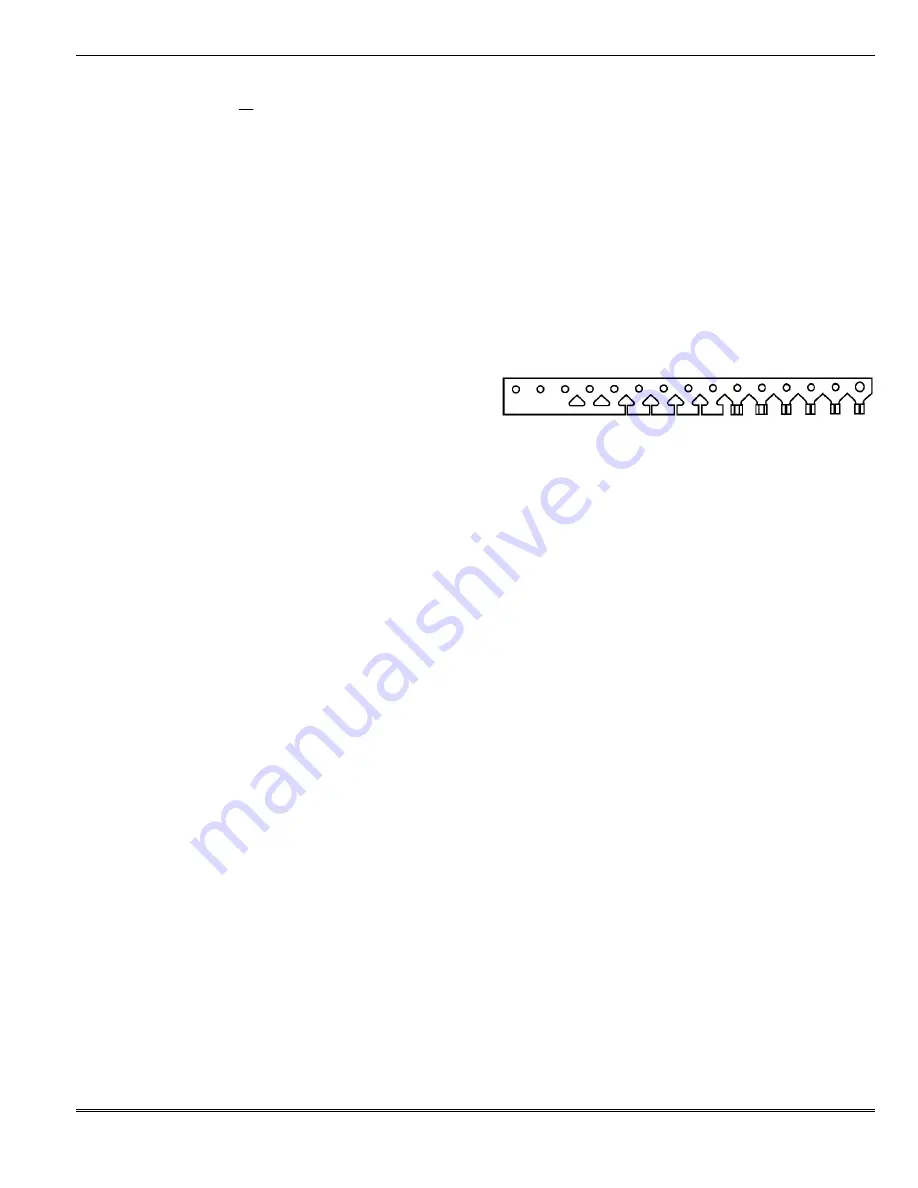
Industrial Crimp Quality Handbook
Doc No: TM-640160065
Release Date: 00-00-02
UNCONTROLLED COPY
Page 26 of 27
Revision: C
Revision Date: 12-23-09
R
=
I
E
Where:
R
is the resistance (in milliohms)
E
is the voltage drop (in millivolts)
I
is the current flowing (in amperes)
Crimp voltage drop and resistance values are quite
small and are expressed in terms of milivolts (.001
volts) and miliohms (.001 ohms).
A crimp joint of poor quality could be caused by
several factors. It is indicated by increased resistance,
which cause increase in voltage drop value.
For example, the presence of air pockets or voids in
the crimped joint will cause a higher resistance
(smaller area of contact between terminal and wire).
Increased resistance results in a higher voltage drop
and a temperature rise, which in turn increases the
corrosion rate and further increases the resistance.
A crimped joint that has been over-crimped and the
conductor (wire) elongated out of shape could cut the
circular area of the conductor and cause a greater
resistance at this weakened point.
8.5 Crimp Joints
A finely stranded wire (large number of small diameter
strands) usually improves crimped joint performance.
A wire composed of a few strands of larger size will
tend to act as a solid wire in the crimp. Some
stranded wire crimp configurations are not satisfactory
for solid wire. More deformation must be imposed in
order to form wire and barrel into a solid mass. On the
other hand, finer strands will more readily fill the inside
corners of the crimp shape and more evenly distribute
the forces of the crimp.
Brazed barrel terminals usually give higher tensile test
than the non-brazed (for specific values, tensile tests
must be performed on each terminal).
Annealing
When the metal part of a solderless terminal is
stamped on a stamping press; the strip of metal
material is repeatedly hit in the stamping process.
These terminals are made on progressive dies.
This repeated hitting causes the metal (usually
copper) to become work hardened. Copper gives its
best mechanical and electrical characteristics when it
is in its original (not work hardened) state.
In order to return the work hardened copper to its
normal soft and malleable state, it must be annealed.
Annealing is accomplished by heating the metal
(copper) terminal in a furnace, and then cooling it
slowly. This process restores the copper to its
original state.
How does annealing (or lack of) affect the crimp
barrel and quality of a solderless terminal?
When a work-hardened terminal is crimped, it does
not form around the wire in a uniform fashion, thus
giving sharp angles, which allows for voids. The
annealed barrel can be easily formed, giving uniform
pressure on the wire and thus a superior crimp.