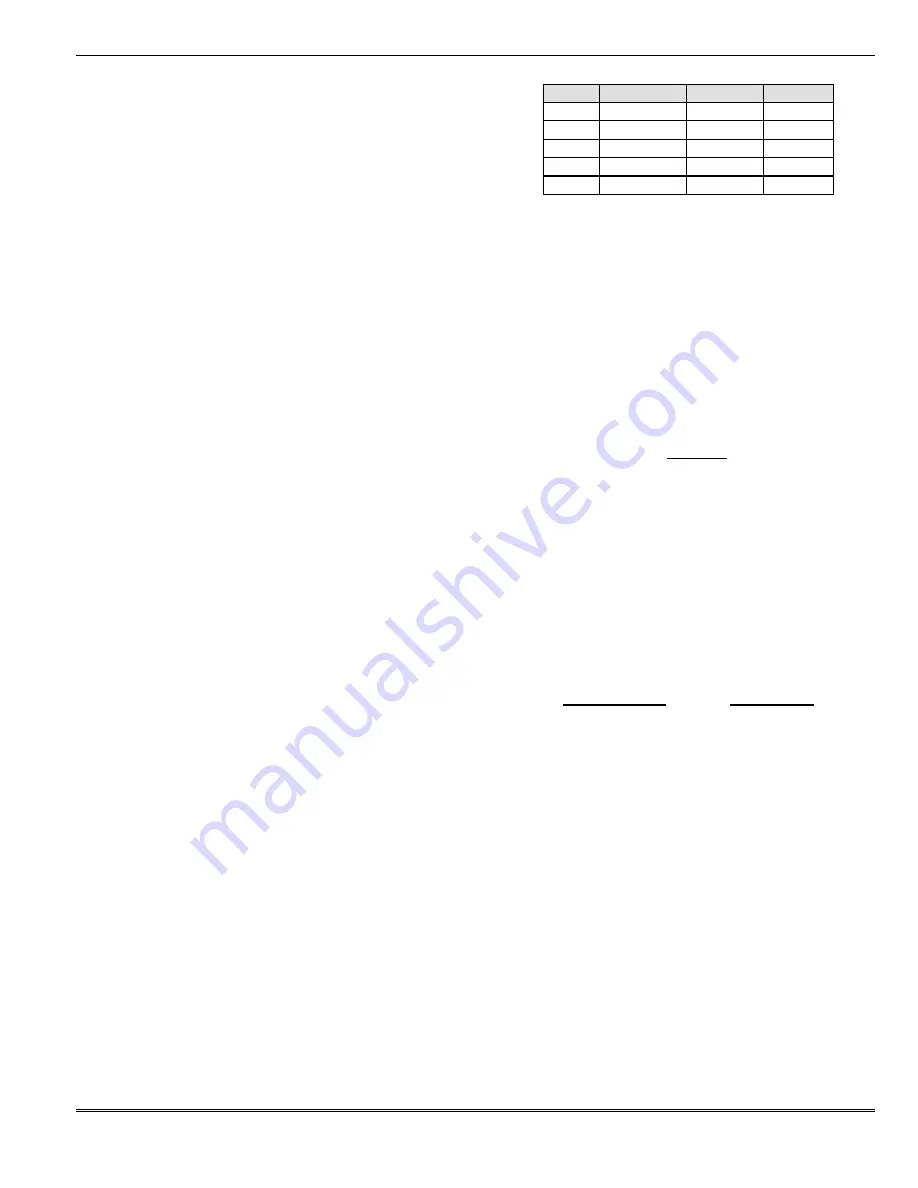
FineAdjust Applicator
Doc. No: TM-638004900
Release Date: 09-04-03
UNCONTROLLED COPY
Page 46 of 50
Revision: G
Revision Date: 01-15-13
B.1 Crimp Process Control
The crimp process is the interaction of a terminal, wire,
tooling, personnel, methods and procedures, and
environmental attributes that, when controlled, produce a
quality termination. Quality control is an important aspect
of quality crimping. It should not take excessive setup or
inspection time to implement, and can save a harness
manufacturer thousands of dollars in potential rework or
re-manufacturing.
The key to quality is to target nominal specifications while
continuously reducing variability. Achieving target is
determined by the adjustability of the tooling. The
FineAdjust applicator allows crimp height adjustment to
.005mm (.0002”) of target.
Variability is the slight changes that occur from crimp to
crimp. There are two types of variability, common and
special. Common sources of variation are those causes
that affect the process uniformly, and are created from
numerous small sources. Common variability is inherent
tolerances within a reel of wire or terminals. In addition,
common variability is created by the natural tolerances of
the stripping and crimping machines. Reduction of
variability at the common level normally has to come from
changes at the wire, terminal, and tooling manufacturer.
The second source of variability is referred to as special
cause. Unlike common cause, special sources of
variation occur irregularly and unpredictably. Without
checks throughout a run, a tool becoming loose after the
first hundred crimps, or a damaged tool from a jam, may
be undetected until thousands of crimps are made.
This section assumes that crimp height is being
measured with a resolution of .0025 mm (.0001”), and
pull force is measured with a resolution of 1 N (.25 lbf).
B.2 Process Capability
Molex qualifies each FineAdjust Applicator design for pull
force and crimp height.
This qualification is performed on a common wire
stranding, and is targeted at 2.0 C
pk
. Before a new
crimping tool is put in production, it is recommended that
the customer using their specific wire in their process
should do a capability study. A capability study is based
on the assumption of a normal distribution (bell-type
curve). It provides an estimate on the probability of a
measurement being outside of specification.
C
pk
+/- Sigma
% Yield
PPM
0.67
2
95.45
45,500
1
3
99.73
2,699
1.33
4
99.99
63
1.67
5
99.99+
0.57
2
6
99.99++
0
PPM - Parts per million – number of potential defects
per million crimps produced.
A minimum of a 25-piece sample should be run off
the crimping process. The average and standard
deviation should be calculated for each specification.
A capability index (C
p)
is defined by the formula
below. C
p
may range in value from 0 to infinity, with
a larger value indicating a more capable process. A
value greater than (>) 1.33 is normally considered
acceptable.
Tolerance
6*Standard Deviation
The C
pk
index indicates whether the process will produce
units within the tolerance limits. C
pk
has a value equal to
C
p
if the process is centered on the mean of specification;
if C
pk
is negative, the process mean is outside the
specification limits; if C
pk
is between 0 and 1 then some of
the 6 sigma spread falls outside the tolerance limits. If
C
pk
is larger than 1, the 6 sigma spread is completely
within the tolerance limits. C
pk
is calculated with the
lesser of the following formulas:
(USL - MEAN) (LSL - MEAN)
3*Standard Deviation 3*Standard Deviation
USL = Upper Specification Limit, LSL = Lower
Specification Limit
Six sigma is a goal of many companies because it
represents virtually zero defects. The ability of a
company to achieve a six-sigma level is dependent on
the amount of common variability in their process. Hand
stripping of the wire will produce more variability than a
stripping machine.
A crimping hand tool will produce more variability than a
press and die set. Bench terminations will produce more
variability than a wire-processing machine.
A portion of the variability in crimping will come from what
instruments are used to measure the parts and the ability
of an operator to repeat the measurement. A crimp
micrometer will measure more accurately than a dial
caliper. An automatic pull force system will measure