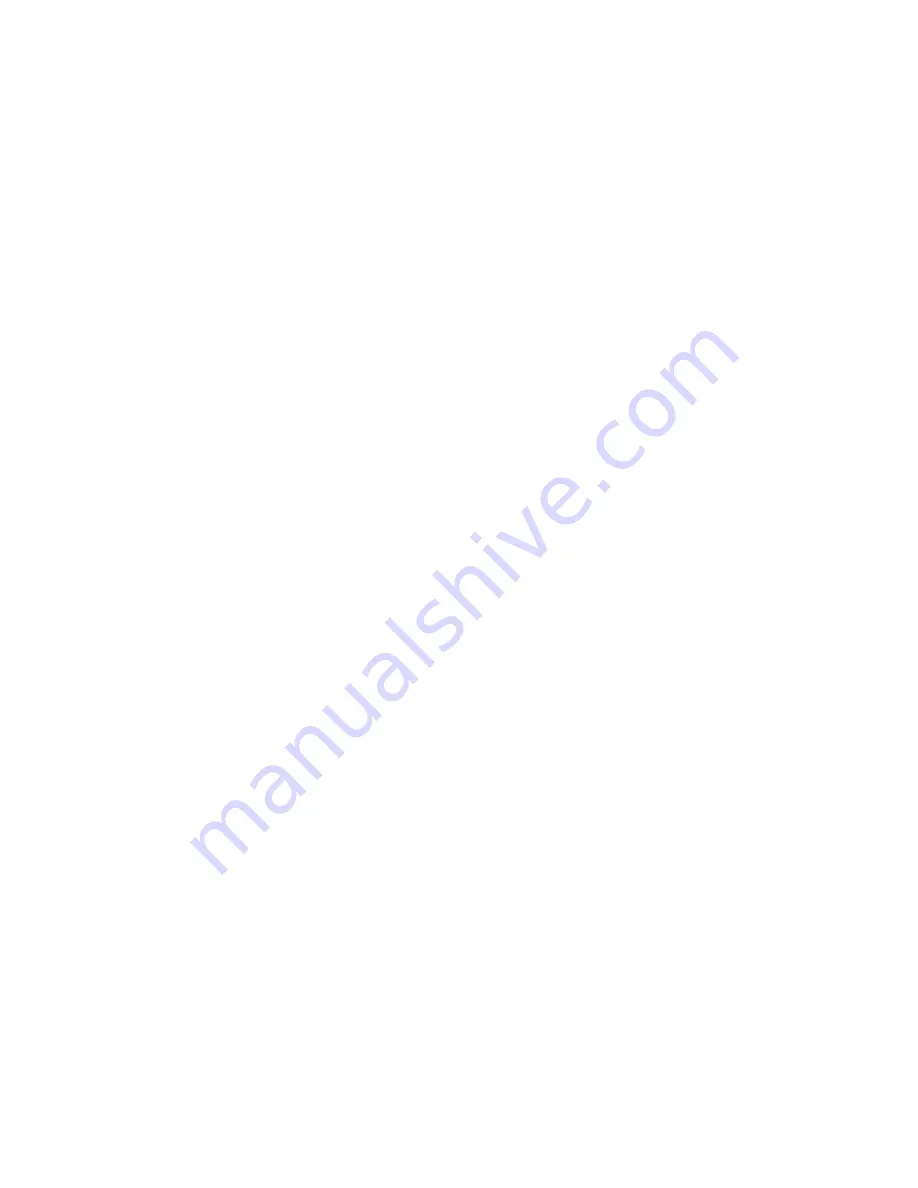
2
2
T
TH
HE
E IIN
NS
ST
TA
AL
LL
LA
AT
TIIO
ON
N A
AN
ND
D M
MA
AIIN
NT
TE
EN
NA
AN
NC
CE
E IIN
NS
ST
TR
RU
UC
CT
TIIO
ON
NS
S
IIN
N T
TH
HIIS
S M
MA
AN
NU
UA
AL
L M
MU
US
ST
T B
BE
E F
FO
OL
LL
LO
OW
WE
ED
D T
TO
O E
EN
NS
SU
UR
RE
E S
SA
AF
FE
E,,
E
EF
FF
FIIC
CIIE
EN
NT
T A
AN
ND
D T
TR
RO
OU
UB
BL
LE
E-F
FR
RE
EE
E O
OP
PE
ER
RA
AT
TIIO
ON
N.. IIN
N
A
AD
DD
DIIT
TIIO
ON
N,, P
PA
AR
RT
TIIC
CU
UL
LA
AR
R C
CA
AR
RE
E M
MU
US
ST
T B
BE
E E
EX
XE
ER
RC
CIIS
SE
ED
D
R
RE
EG
GA
AR
RD
DIIN
NG
G T
TH
HE
E S
SP
PE
EC
CIIA
AL
L P
PR
RE
EC
CA
AU
UT
TIIO
ON
NS
S L
LIIS
ST
TE
ED
D B
BE
EL
LO
OW
W..
F
FA
AIIL
LU
UR
RE
E T
TO
O P
PR
RO
OP
PE
ER
RL
LY
Y A
AD
DD
DR
RE
ES
SS
S T
TH
HE
ES
SE
E C
CR
RIIT
TIIC
CA
AL
L
A
AR
RE
EA
AS
S C
CO
OU
UL
LD
D R
RE
ES
SU
UL
LT
T IIN
N P
PR
RO
OP
PE
ER
RT
TY
Y D
DA
AM
MA
AG
GE
E O
OR
R L
LO
OS
SS
S,,
P
PE
ER
RS
SO
ON
NA
AL
L IIN
NJ
JU
UR
RY
Y,, O
OR
R D
DE
EA
AT
TH
H..
1.
Any power supply must be disconnected before making
wiring connections to prevent electrical shock and
equipment damage. All units must be wired strictly in
accordance with the wiring diagram (see Fig. 6 page 9).
2.
The gas supply must be turned off before commencing
installation of the heaters. An isolating union gas cock or
union and isolating gas cock M
MU
US
ST
T be fitted before the inlet
to the gas valve to allow replacement of parts.
3.
The gas supply pressure to the unit heater controls must
never exceed 45mbar.
When leak testing the gas supply system, the unit, and its
combination gas control, must be isolated during any
pressure testing in excess of 45mbar. The unit should be
isolated from the gas supply system by closing the manual
shutoff valve.
4.
Start-up and adjustment procedures should be performed
by a qualified engineer. The gas inlet pressure should be
checked upstream of the combination gas control. The inlet
pressure should be at least 20mbar on natural gas or 37mbar
on propane. Purging of gas piping should be performed as
described in IM2. Supply pressure and setting pressure must
be checked with heater in operation when making final
adjustments.
5.
All units must be flued to outside.
6.
The units M
MU
US
ST
T N
NO
OT
T b
be
e installed in potentially explosive or
flammable atmospheres laden with grain dust, sawdust or
similar airborne materials.
7.
Installation of units in high humidity or salt water
atmospheres should be avoided as this will cause
accelerated corrosion resulting in a reduction of the normal
life span of the units.
8.
To prevent premature heat exchanger failure do not locate
A
AN
NY
Y gas fired unit in areas where chlorinated, halogenated
or acid vapours are present in the atmosphere.
9.
Do not install units in extremely draughty locations.
Draughts can cause burner flames to impinge on the heat
exchanger thereby shortening its life. Separation between
units should be maintained to avoid discharge from one unit
entering the inlet of another.
10. Do not install units in tightly sealed rooms or small
compartments without provision for adequate combustion
air and venting. Combustion air must have access to the
space through a minimum of two permanent openings in
the enclosure, one near the bottom and the other near the
top. They should provide a free area of at least the values
given in Section 2.2 ‘Ventilation’.
11. Do not install units outdoors
12. For all sizes, required minimum clearance to combustible
materials from the bottom of the unit is 300mm (however
see page 2 section 16 which may require greater
clearances for servicing) and from the sides 450mm. For
PDE units sizes 30-50 minimum clearance from the top is
25mm and from the flue collar 50mm; for PDE units sizes
75-300 minimum clearance from the top is 50mm and from
the flue collar is 75mm; for PDE unit 350 minimum
clearance from the top is 75mm and from the flue collar is
100mm, for PDE unit 400 minimum clearance from the top
is 100mm and from the flue collar is 125mm.
13. At least 150mm clearance at the sides and 300mm
clearance at rear (or 150mm beyond end of motor at rear of
unit, whichever is greater) must be allowed to provide
sufficient air for combustion and correct operation of the
fan. However see page 2 section 12 for clearances to
combustible material.
14. The minimum distance required from combustible materials
is based on the combustible material surface not exceeding
70°C. Clearance from the top of the unit may be required to
be greater than 150mm if heat damage, other than fire,
may occur to materials above the unit heater at the
temperature described.
15. PDE unit heaters are designed for use in heating
applications with ambient temperatures between 0°C
and 32°C. If an application exists where ambient
temperatures can be expected to fall outside of this range,
contact your local sales representative for
recommendations.
16. Clearance must be provided for opening hinged bottom for
servicing. See Figure 1. Do not stand unit on its base.
17. To ensure that flames do not impinge on heat exchanger
surfaces, the unit must be suspended in a vertical and level
position. Failure to suspend a unit properly may shorten its
life.
18. The unit heater must not be lifted by its gas controls or gas
manifold.
19. Ensure there are no obstructions which block air intake and
discharge of the unit heater.
20. Do not attach duct work or air filters to any PDE model unit
heaters.
21. In aircraft hangars, the bottom of the unit must be at least
3m from the highest surface of the wings or engine
enclosures of the highest aircraft housed in the hangar and
the installation must be in accordance with the
requirements of the enforcing authority.
22. In garages or other sections of aircraft hangars such as
offices and shops which communicate with areas used for
servicing or storage, the bottom of the unit must be at least
1.8m above the floor.
23. The piping, electrical, ventilation and flueing instructions in
this manual should be carefully read before commencing
installation.
24. All literature shipped with the unit should be kept for future
use for servicing or service diagnosis. None of the literature
shipped with the unit should be discarded.
25. Only approved service replacement parts should be used
when servicing or repairing these unit heaters. A complete
replacement parts list may be obtained by contacting your
appliance supplier. The data plate on the unit gives the unit
model number, serial number and company address. Any
substitution of non-approved parts or controls is at the
owners risk and may invalidate the EC Certification.
26. Always turn off the gas supply at the gas cock and
disconnect the electricity supply to the appliance before
servicing or replacing any components.
27. These unit heaters will normally be controlled by a room
thermostat. Harry Taylor have available a proportional
temperature controller (PTC-1) which can be used to
provide this control. If a room thermostat is to be used
contact Harry Taylor for details of suitable models.
IIN
NS
ST
TA
AL
LL
LA
AT
TIIO
ON
N
S
SP
PE
EC
CIIA
AL
L P
PR
RE
EC
CA
AU
UT
TIIO
ON
NS
S