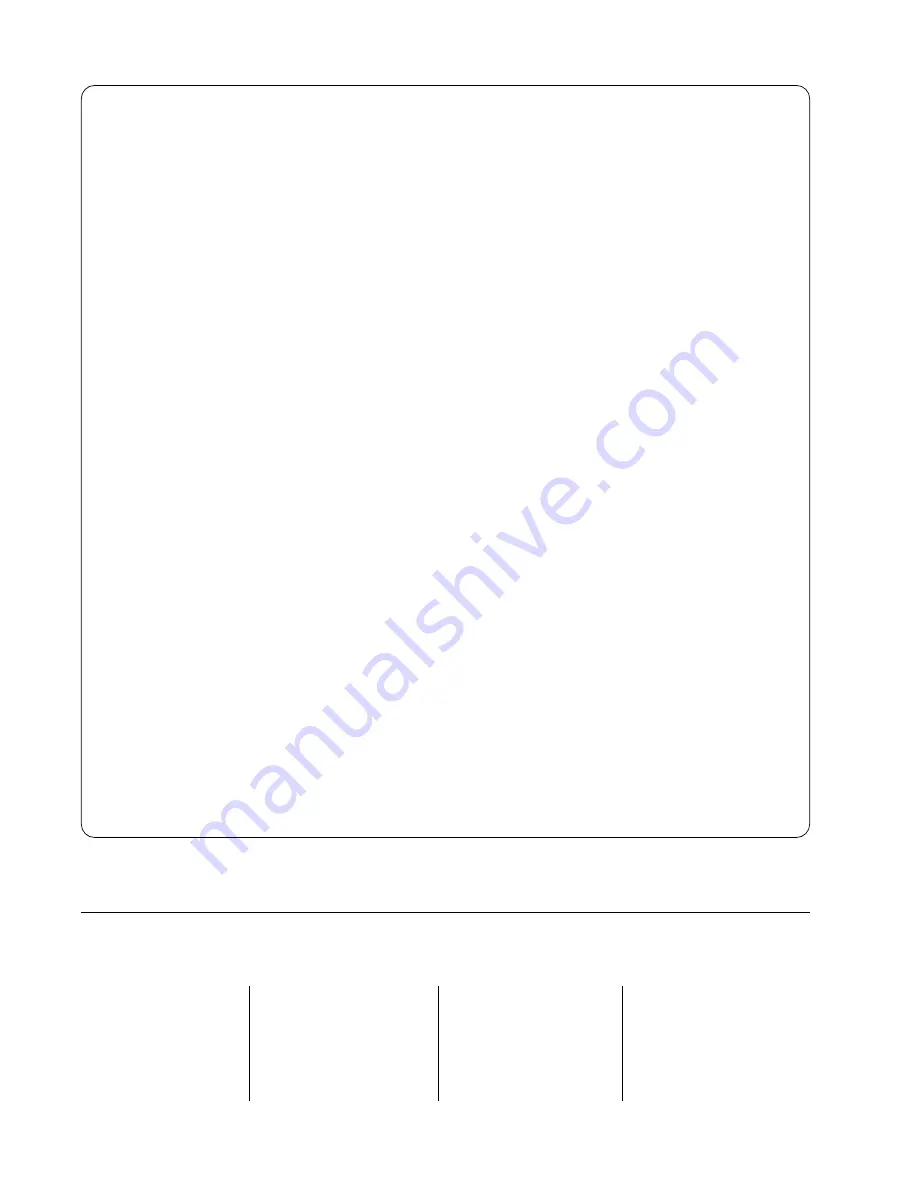
6
Visit our website at http://modeltech.globalhobby.com or for Customer Service at http://globalservices.globalhobby.com
LANDING GEAR ASSEMBLY
❑
(1)
Prebent Aluminum Main Gear Strut
❑
(2)
Main Gear Wheels
❑
(2)
M4 x 16 Machine Screws
❑
(2)
M4 x 35 Smooth-Shank Machine Screws
❑
(8)
M4 Flat Washers
❑
(4)
M4 Lock Nuts
ELEVATOR CONTROL SYSTEM
❑
(1)
19-1/8" Threaded Wire w/90º Bend
❑
(1)
18" Threaded Wire w/Plain End
❑
(2)
Nylon Control Horns w/Backplates (Small)
❑
(4)
M2 x 15 Machine Screws
❑
(2)
Nylon Clevises
❑
(1)
Nylon 90º Snap Keeper
❑
(2)
Wheel Collars w/Set Screws
❑
(6)
C/A Style Hinges
RUDDER CONTROL SYSTEM
❑
(2)
21-1/2" Threaded Wires w/90º Bend
❑
(2)
Nylon Control Horns (Large)
❑
(4)
M2 x 17 Machine Screws
❑
(4)
M2 Hex Nuts
❑
(2)
Nylon Clevises
❑
(2)
Nylon 90º Snap Keepers
❑
(3)
C/A Style Hinges
MISCELLANEOUS WING PARTS
❑
(1)
Hardwood Wing Joiner
❑
(1)
Plywood Wing-Screw Doubler
❑
(2)
M6 x 40 Machine Screws
❑
(2)
M6 Flat Washers
MISCELLANEOUS FUSELAGE PARTS
❑
(1)
Prepainted Molded Fiberglass Cowling
❑
(1)
Molded Clear Canopy
❑
(2)
M2 x 10 Flange-Head Wood Screws
❑
(4)
M3 x 5 Wood Screws
❑
(4)
M3 Flat Washers
❑
(1)
Length of Clear Tubing
❑
(1)
Decal Set
FUEL TANK ASSEMBLY
❑
(1)
320cc Fuel Tank
❑
(1)
Large Diameter Metal Plate
❑
(1)
Small Diameter Metal Plate
❑
(1)
Rubber Stopper
❑
(1)
Fuel Pick-Up "Clunk"
❑
(1)
M3 x 20 Machine Screw
❑
(1)
Silicon Fuel Tubing
❑
(2)
Aluminum Tubing
ENGINE MOUNT ASSEMBLY
❑
(2)
Engine Mounting Beams
❑
(4)
M4 x 20 Socket-Cap Screws
❑
(4)
M4 x 25 Socket-Cap Screws
❑
(4)
M4 Lock Nuts
❑
(12) M4 Flat Washers
To convert inches into millimeters: Inches x 25.4 = mm
To convert millimeters into inches: Millimeters / 25.4 = in
1/64"
=
.4mm
1/32"
=
.8mm
1/16"
=
1.6mm
3/32"
=
2.4mm
1/8"
=
3.2mm
5/32"
=
4.0mm
3/16"
=
4.8mm
1/4"
=
6.4mm
3/8"
=
9.5mm
1/2"
= 12.7mm
5/8"
= 15.9mm
3/4"
= 19.0mm
1"
= 25.4mm
2"
= 50.8mm
3"
= 76.2mm
6"
= 152.4mm
12"
= 304.8mm
18"
= 457.2mm
21"
= 533.4mm
24"
= 609.6mm
30"
= 762.0mm
36"
= 914.4mm
SECTION 4: METRIC CONVERSION CHART
AILERON CONTROL SYSTEM
❑
(2)
3-7/8" Threaded Wires w/Z-Bend
❑
(2)
Nylon Control Horns w/Backplates (Small)
❑
(4)
M2 x 15 Machine Screws
❑
(2)
Nylon Clevises
❑
(8)
C/A Style Hinges