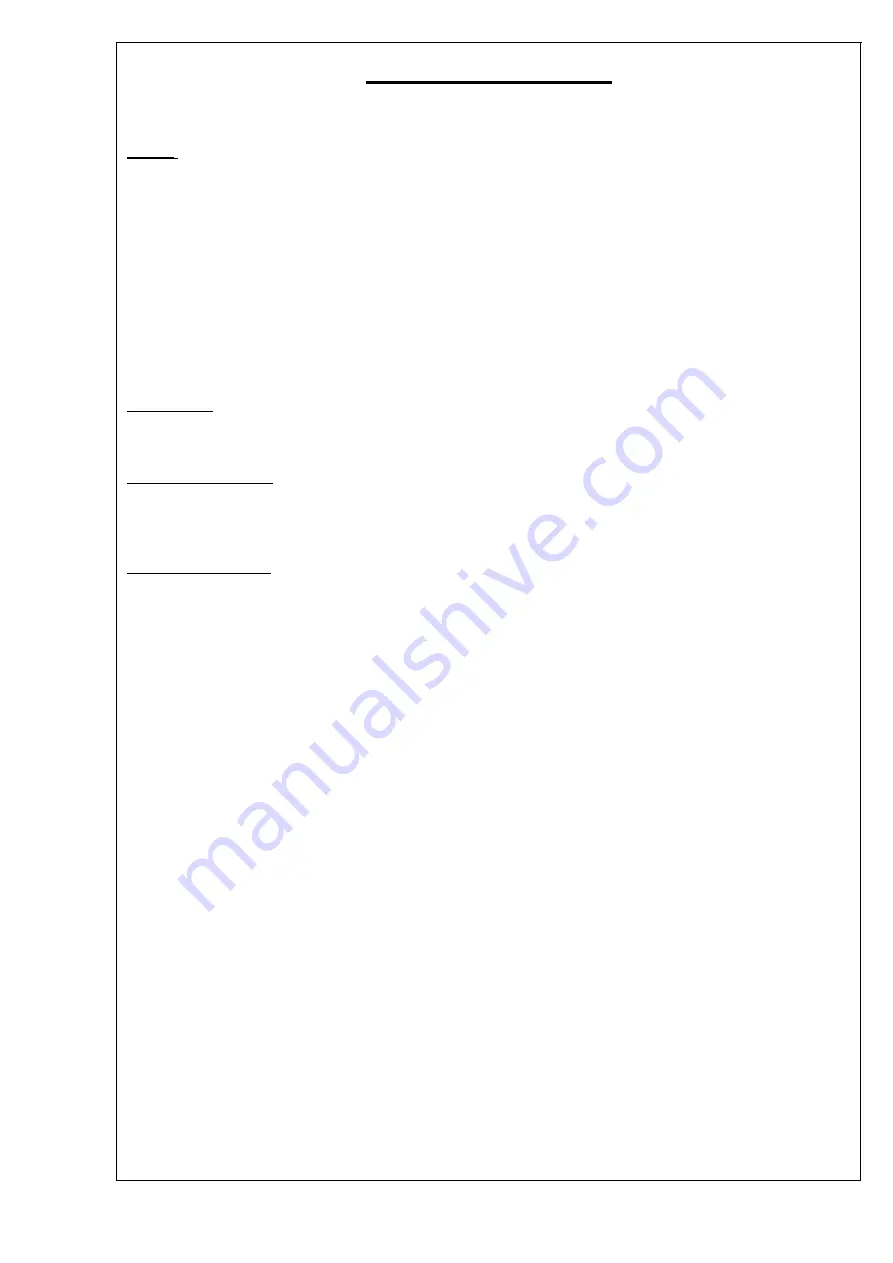
Operation & Maintenance, Page
6
of
23
Section
3
– Revision 2.3
Trouble Shooting Guide
It is recommended that a daily check be made for any excessive noise, vibration, lubricant leaks, or obvious damage. The
following hints should help in determining the source of any unusual feature;
NOISE
– When an unusual noise is heard, it is important to determine quickly what is causing the noise, so that action
can be taken. There are basically two noises to consider.
i
High speed end (Electric Motor)
ii
Low speed ends (Breaker Shafts)
The first step is to determine the frequency of the noise. It will be a regular noise in either the machine aperture or the
drive train. If it is a slow rhythmic noise, it is likely to come from the shafts. This could indicate that there is a broken or
loose bolt. Fully check the machine, the machine aperture, (with no material passing through), to determine the cause.
If the noise is high frequency, it is possibly coming from the drive train. Starting from the motor, work along the transmis-
sion to determine the cause of the noise. The obvious causes would be; faulty bearings in the motor, fluid coupling, or
gearbox; lack of lubricant or ingress of dust into rotating parts.
VIBRATION
– A similar check list is used as when tracking down an unusual noise, however, most excessive vibration
is caused either by faulty main shaft bearings or faulty gearbox bearings. These items should be checked first by checking
the temperature on the frame of the machine adjacent to the shaft bearings and on the casing of the gearbox.
LUBRICANT LEAKS
– It is essential that all lubricants are corrected and replenished in accordance with the service
manual recommendations. If any leak is found, action must be taken immediately to correct it, i.e find the source of the
leak, determine the cause of the leak by reference to the spare parts manual, and identify the parts required to rectify the
leak. When this has been done, the machine must be stopped at the first opportunity so that the work carried out.
OBVIOUS DAMAGE
– 99% of the obvious damage occurring on MMD machines inside the machine aperture is
caused by tramp iron. Broken or cracked caps/segments and bolts are the most common form of obvious damage. A vis-
ual inspection will determine the cause.