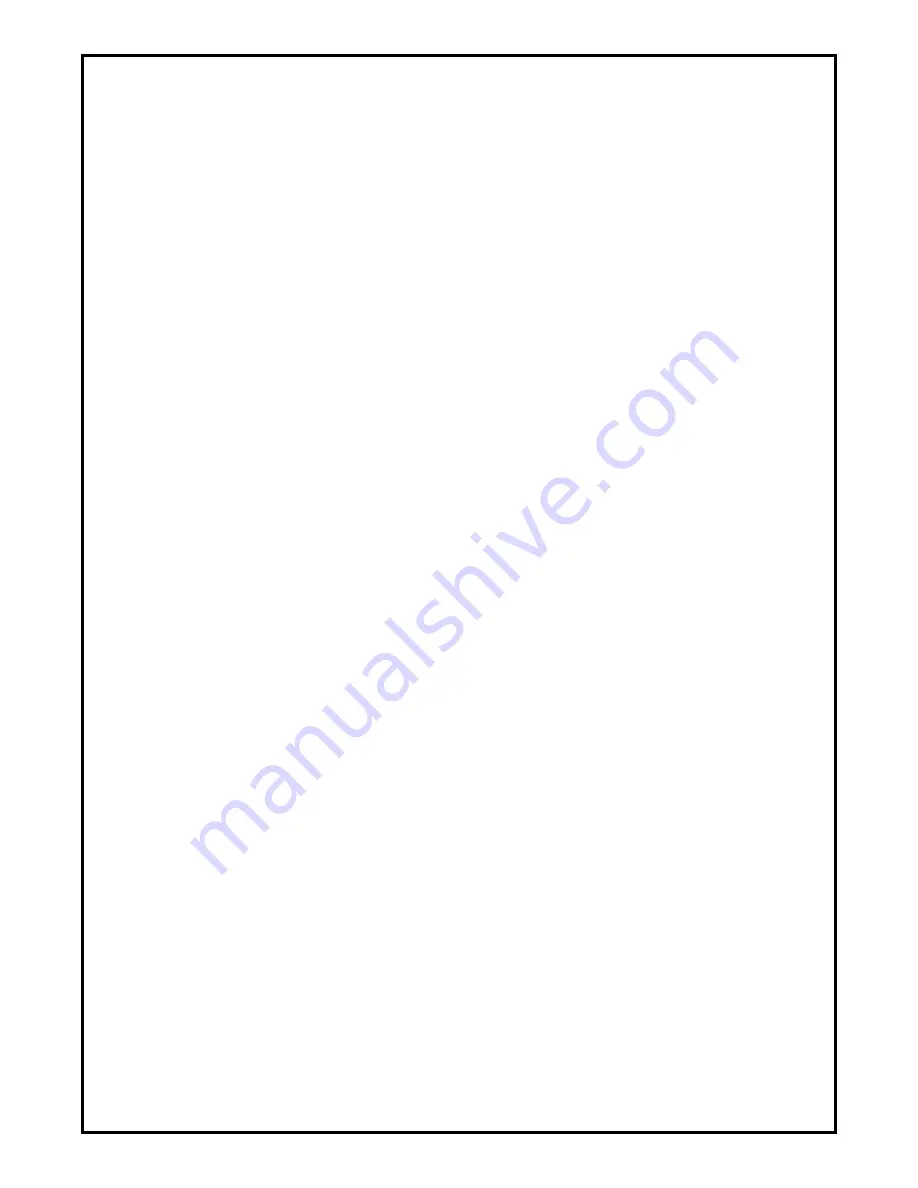
Weld Control Selector Guide - Page iii
SafEty COnSidERatiOnS
- Continued -
very bright and hot. Sparks fly, fumes rise,
ultraviolet and infrared energy radiates,
weldments are hot, and compressed gases
may be used. The wise operator avoids
unnecessary risks and protects himself
and others from accidents.
a. Burn Protection
Comply with precautions in 1-2.
The welding arc is intense and visibly
bright. Its radiation can damage eyes,
penetrate lightweight clothing, reflect from
light-colored surfaces, and burn the skin and
eyes. Skin burns resemble acute sunburn;
those from gas-shielded arcs are more
severe and painful. DON’T GET BURNED;
COMPLY WITH PRECAUTIONS.
1. Protective Clothing
Wear long-sleeve clothing in addition to
gloves, hat, and shoes. As necessary,
use additional protective clothing such
as leather jacket or sleeves, flameproof
apron, and fire-resistant leggings. Avoid
outer garments of untreated cotton.
Bare skin protection. Wear dark, substantial
clothing. Button collar to protect chest and
neck, and button pockets to prevent entry
of sparks.
2. Eye and Head Protection
Protect eyes from exposure to arc. Eyes
may be damaged by radiant energy when
exposed to the electric arc, even when not
looking in the direction of the arc. Never look
at an electric arc without protection.
Welding helmet or shield containing a filter
plate shade no. 12 or denser must be used
when welding. Place over face before
striking arc.
Protect filter plate with a clear cover plate.
Cracked or broken helmet or shield should
NOT be worn; radiation can be passed
through to cause burns.
Cracked, broken, or loose filter plates
must be replaced IMMEDIATELY. Replace
clear cover plate when broken, pitted, or
spattered.
Flash goggles with side shields MUST
be worn under the helmet to give some
protection to the eyes should the helmet
not be lowered over the face before an arc
is struck. Looking at an arc momentarily
with unprotected eyes (particularly a high
intensity gas-shielded arc) can cause a
retinal burn that may leave a permanent
dark area in the field of vision.
3. Protection of nearby Personnel
Enclose the welding area. For production
welding, a separate room or enclosed bay is
best. In open areas, surround the operation
with low-reflective, noncombustible screens
or panels. Allow for free air circulation,
particularly at floor level.
Viewing the weld. Provide face shields for
all persons who will be looking directly at
the weld.
Others working in area. See that all persons
are wearing flash goggles.
Before starting to weld, make sure that screen
flaps or bay doors are closed.
B. toxic fume Prevention
Comply with precautions in 1-2B.
Generator engine exhaust must be vented to
the outside air. Carbon monoxide can kill.
C. fire and Explosion Prevention
Comply with precautions in 1-2C.
Equipment’s rated capacity. Do not overload
arc welding equipment. It may overheat cables
and cause a fire.
Loose cable connections may overheat or
flash and cause afire.
Never strike an arc on a cylinder or other
pressure vessel. It creates a brittle area that
can cause a violent rupture or lead to such a
rupture later under rough handling.
d. Compressed Gas Equipment
Comply with precautions in 1-2D.
E. Shock Prevention
Exposed electrically hot conductors or
other bare metal in the welding circuit, or in
ungrounded, electrically-HOT equipment can
fatally shock a person whose body becomes a
conductor. DO NOT STAND, SIT, LIE, LEAN
ON, OR TOUCH a wet surface when welding
without suitable protection.
To protect against shock:
Keep body and clothing dry. Never work in
damp area without adequate insulation against
electrical shock. Stay on a dry duckboard, or
rubber mat when dampness or sweat cannot
be avoided. Sweat, sea water, or moisture
between body and an electrically HOT part -
or grounded metal - reduces the body surface
electrical resistance, enabling dangerous
and possibly lethal currents to flow through
the body.
1. Grounding the Equipment
When installing, connect the frames of each
unit such as welding power source, control,
work table, and water circulator to the building
ground. Conductors must be adequate to carry
ground currents safely. Equipment made
electrically HOT by stray currents may shock,
possibly fatally. Do NOT GROUND to electrical
conduit, or to a pipe carrying ANY gas or a
flammable liquid such as oil or fuel.
Three-phase connection. Check phase
requirement of equipment before installing. If
only three-phase power is available, connect
single-phase equipment to only two wires of
the three-phase line. Do NOT connect the
equipment ground lead to the third (live) wire,
or the equipment will become electrically
HOT - a dangerous condition that can shock,
possibly fatally.
Before welding, check ground for continuity.
Be sure conductors are touching bare metal
of equipment frames at connections.
If a line cord with a ground lead is provided
with the equipment for connection to a
switch box, connect the ground lead to
the grounded switch box. If a three-prong
plug is added for connection to a grounded
mating receptacle, the ground lead must be
connected to the ground prong only. If the
line cord comes with a three-prong plug,
connect to a grounded mating receptacle.
Never remove the ground prong from a plug,
or use a plug with a broken ground prong.
2. Connectors
Fully insulated lock-type connectors should
be used to join welding cable lengths.
3. Cables
Frequently inspect cables for wear, cracks,
and damage. IMMEDIATELY REPLACE
those with excessively worn or damaged
insulation to avoid possibly lethal shock
from bared cable. Cables with damaged
areas may be taped to give resistance
equivalent to original cable.
Keep cable dry, free of oil and grease, and
protected from hot metal and sparks.
4. terminals and Other Exposed Parts
Terminals and other exposed parts of
electrical units should have insulating
covers secured before operation.
5. Electrode Wire
Electrode wire becomes electrically HOT
when the power switch of gas metal-arc
welding equipment is ON and welding gun
trigger is pressed. Keep hands and body
clear of wire and other HOT parts.
6. Safety devices
Safety devices such as interlocks and circuit
breakers should not be disconnected or
shunted out.
Before installation, inspection, or service of
equipment, shut OFF all power, and remove
line fuses (or lock or red-tag switches) to
prevent accidental turning ON of power.
Disconnect all cables from welding power
source, and pull all 115 volts line-cord
plugs.
Do not open power circuit or change polarity
while welding. If, in an emergency, it must
be disconnected, guard against shock burns
or flash from switch arcing.
Leaving equipment unattended. Always
shut OFF, and disconnect all power to
equipment.
Power disconnect switch must be available
near the welding power source.