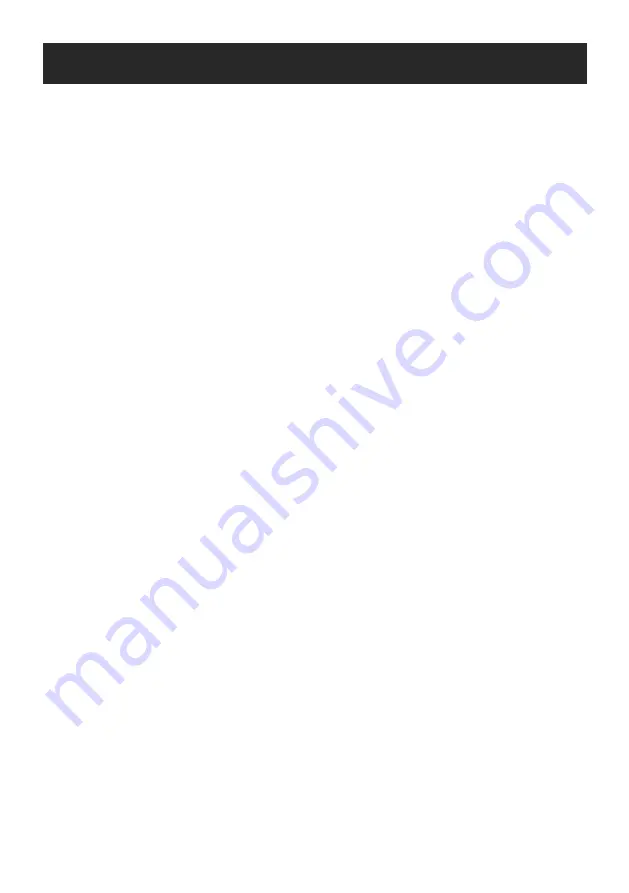
10
Installation: general guidelines
Unvented installations
In the case of an unvented installation, installers should ensure
incoming mains pressure is less than 1 MPa (10 bar) and that local
authority approval for installation of unvented systems is granted.
Ensure adequate flow rate is available.
Use of flux and sterilisation
Excessive use of flux can damage the unit and especially the valves
and expansion vessel (if supplied). Avoid over-use and ensure the
system is fully flushed of any debris or flux after connection. If a full
sterilisation of all the pipework including the cylinder is required
then a complete drain down and flush of the unit is essential. A
simple flush through with water is not adequate in removing all
sterilising solution within the cylinder. Under no circumstances
should sterilising solution be left in the cylinder any longer than re-
quired (seek dosage requirements from chemical manufacturer).
Pipework and cold water control group
The unit should be piped in with a nominal 22mm pipe to ensure
adequate flow rate. The unit is supplied with a monobloc pressure
reducing valve that has a set pressure of 3.0 bar. The valve also
consists of a serviceable strainer, non return valve, expansion relief
valve, connection for an expansion vessel and balanced cold feed
supply. We would strongly recommend fitting an isolating valve
(not supplied) prior to the monobloc valve for ease of maintenance
at a later date. Under no circumstances should an insolating valve
be fitted between the expansion valve and the storage cylinder.
Fitting a drain valve
Please ensure that a drain valve is fitted to the lowest part of the
unit, The drain valve must be fitted as low as possible so that at
least 80% of the cylinder’s total capacity can be drained off.
Connecting the hot draw
It is recommended that a 90° elbow be fitted within 100 mm of
the hot draw to minimize heat losses due to thermosiphoning.
Summary of Contents for M0008
Page 15: ...15 Installation electrical...
Page 16: ...16 Installation electrical...
Page 33: ...33 Service record Service date Serviced by Comments...
Page 35: ......