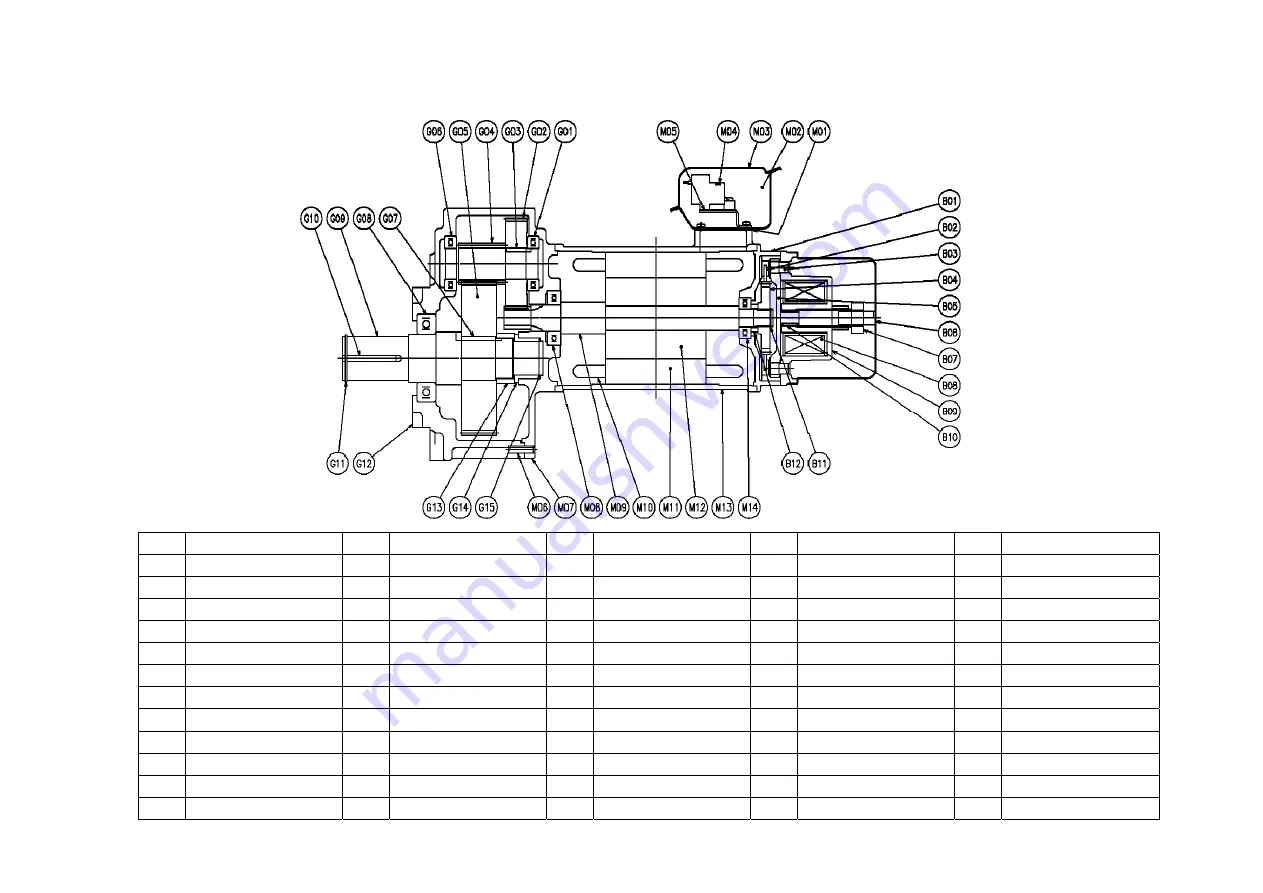
GEARED MOTOR CONSTRUCTION
( ST-2.2D2-W )
Item Description Item
Description Item
Description Item
Description Item
Description
G01 Ball Bearing
G13
Spacer
M01
Packing
M13
Stator Frame
B01
Brake Casing
G02 No.2 Gear
G14
Metal
M02
Terminal Box
M14
Ball Bearing
B02
Brake Disk
G03 Key
G15
Oil
immersed
M03
Cover
B03
Pin
G04 No.3 Gear
M04
Terminal Block
B04
Brake Gear
G05
No.4
Gear
M05
Plate
B05
Movable
Core
G06
Ball
Bearing
M06
Parallel
Pin
B06
Cover
G07
Key
M07
L
Bracket
B07
Adjustment
Bolt
G08 Ball Bearing
M08
Ball Bearing
B08
Brake Coil
G09
Output
Shaft
M09
Motor
Shaft
B09
Stationary
Core
G10
Key
M10
Stator
Coil
B10
Coil
Spring
G11
Snap
Ring
M11
Stator
Core
B11
Snap
Ring
G12
Gear
Casing
M12
Rotor
B12
Spacer
P288902
-
31
-