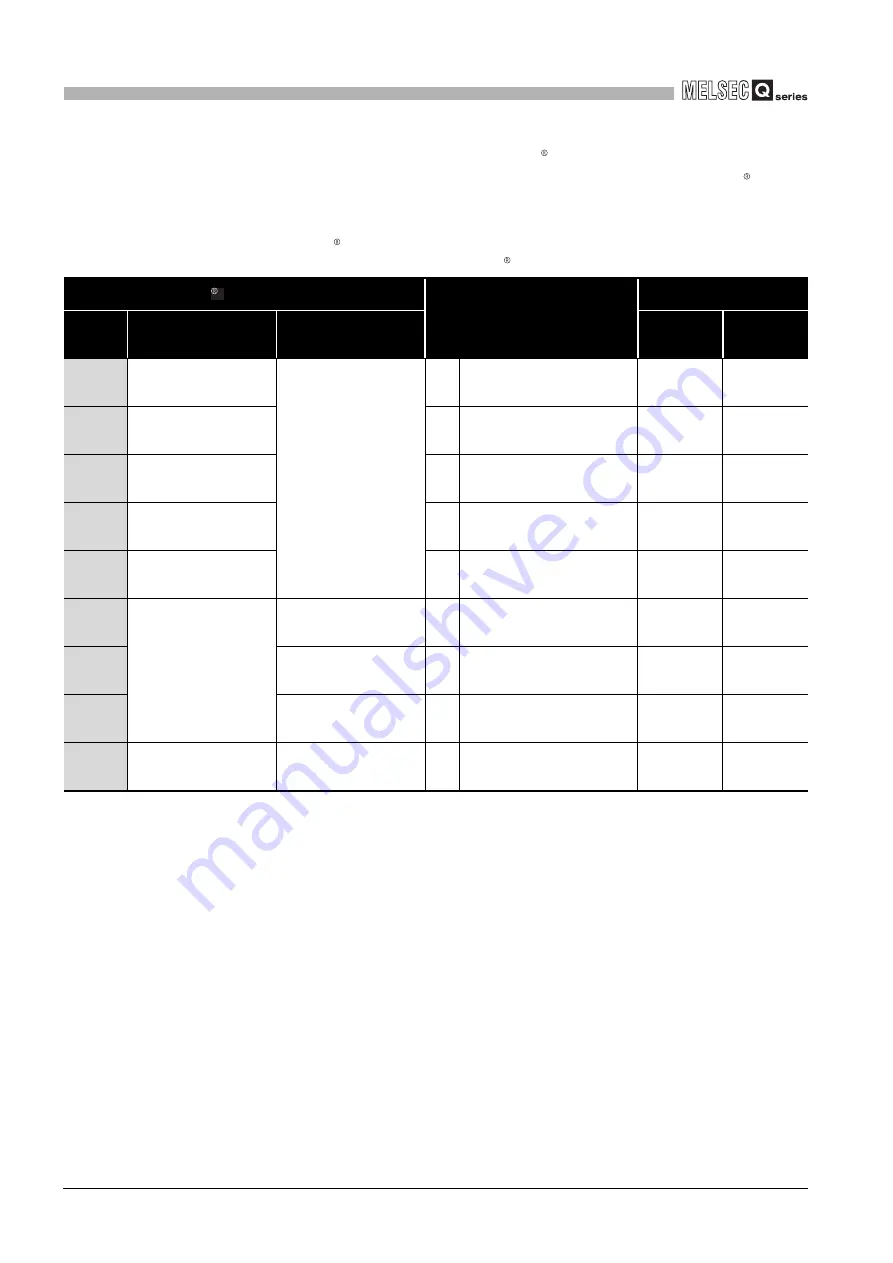
10
- 7
10.2 Z(P).MBRW
10
DEDICATED INSTRUCTIONS
(a) Type specification of the target MODBUS device
The table below shows the possible combinations in the target MODBUS device
type specification ((S1)+8) and the valid ranges of the access points.
Any other combinations are not applicable to the Type specification of the target
MODBUS device type ((S1)+8).
* 1 Read File Record (FC: 20) and Write File Record (FC: 21) allows access to multiple areas in one
transmission, however, only one area is accessible in one transmission when using this dedicated
instruction.
* 2 In the case of broadcast, only 0001
H
(Write multiple coils), 0005
H
(Write multiple registers) and
0007
H
(Write file record) can be set.
* 3 Simultaneous execution of read and write with a single instruction is allowed only for 0505
H
(Read/
Write multiple registers).
Table10.6 Possible combinations of target MODBUS
device type specification
Target MODBUS
device type specification
Function code
Valid access point range
Setting
value
Read target
Write target
Read points
Write points
0100
H
Coil
No specification
01
Read coils
1 to 2000
points
-
0200
H
Input
02
Read discrete inputs
1 to 2000
points
-
0400
H
Input register
04
Read input registers
1 to 125
points
-
0500
H
Holding register
03
Read holding registers
1 to 125
points
-
0700
H
Extended file register
*1
20
Read file record
1 to 124
points
-
0001
H
*2
No specification
Coil
15
Write multiple coils
-
1 to 1968
points
0005
H
*2
Holding register
16
Write multiple registers
-
1 to 123
points
0007
H
*2
Extended file register
*1
21
Write file record
-
1 to 122
points
0505
H
*3
Holding register
Holding register
23
Read/Write multiple registers
1 to 125
points
1 to 121
points
Summary of Contents for QJ71MB91
Page 1: ......
Page 2: ......
Page 366: ...App 14 Appendix 4 External Dimensions APPENDICES Memo ...
Page 371: ......
Page 372: ......