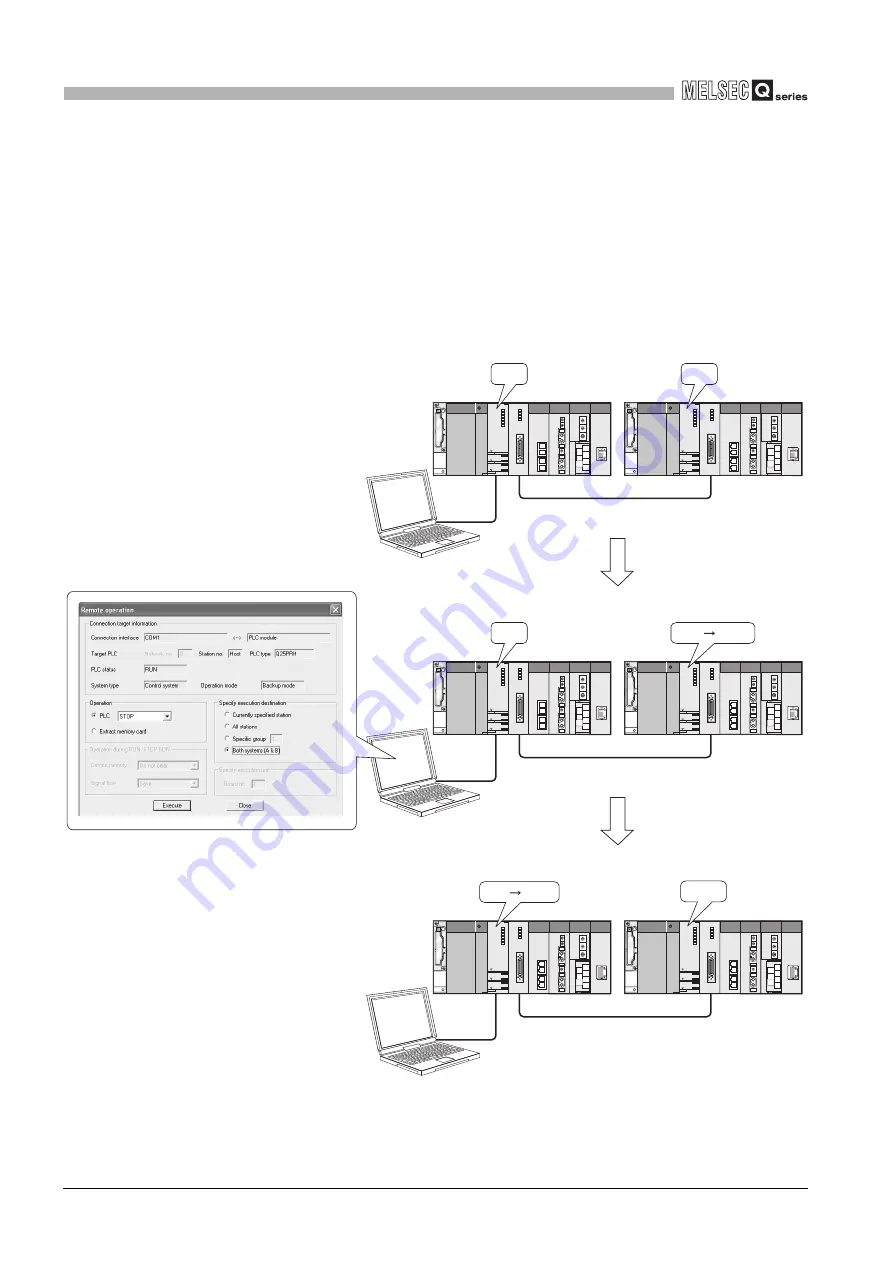
5
- 133
5.10 Redundant CPU Functions Restricted in Redundant System
5.10.2 Remote Operation for Redundant System
5
(b) Remote operation for both systems
When "Both systems (A & B)" is selected at the execution destination area on the
Remote operation screen of GX Developer, remote operation is performed for the
control system and standby system.
Remote operation for "Both systems" can be selected in the backup mode only.
(In the separate mode, "Both systems" cannot be selected at the execution
destination area on the Remote operation screen of GX Developer.)
When "Both systems (A & B)" is selected, GX Developer executes remote
operation in order of the "standby system CPU module" and "control system CPU
module".
Diagram 5.100 Remote STOP Operation When Both Systems Are Specified
Control system
Standby system
Control system
Standby system
GX Developer
GX Developer
Tracking cable
Tracking cable
RUN
STOP
RUN STOP
RUN STOP
Control system
Standby system
GX Developer
Tracking cable
RUN
RUN