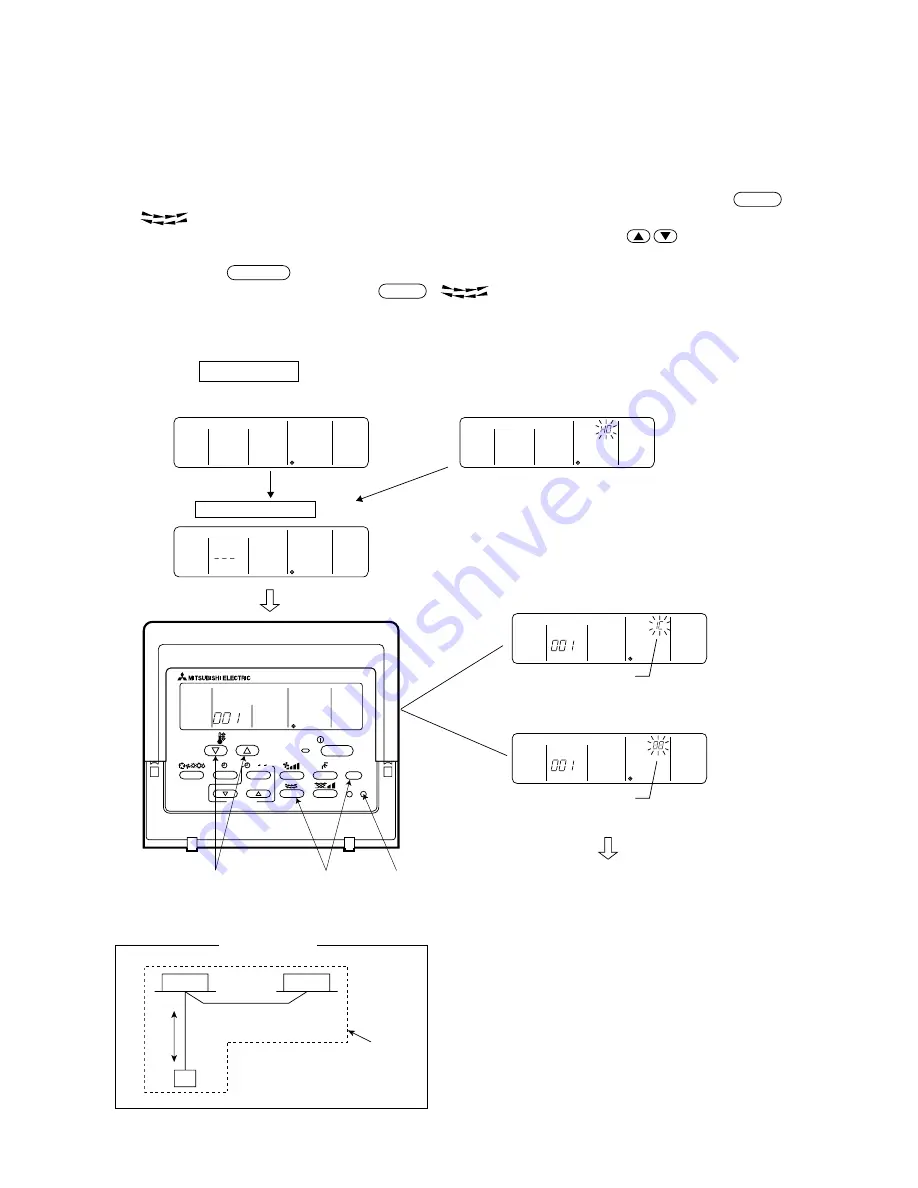
–36–
(3) Group registration of indoor unit
1)
Registration method
• Group registration of indoor units ......................................................................
1
The indoor units to be controlled by a remote controller are registered on the remote controller.
[Registration procedure]
1
With the remote controller under stopping mode or with “HO” displayed on the LED, press and hold the
FILTER
+
buttons (
A
+
B
) simultaneously for 2 seconds to switch to the registration mode. (See the figure below.)
2
Assign the indoor unit address to “INDOOR UNIT ADDRESS NO.” by operating the
(Room temperature
adjustment) (
C
).
Then press the
TEST RUN
switch (
D
) to register. In the figure below, the “INDOOR UNIT ADDRESS NO.” is set to 001.
3
After completing the registration, press the
FILTER
+
buttons (
A
+
B
) simultaneously for 2 seconds to return
to the original mode (with the remote controller under stopping mode).
• Remote controller stopped
• “HO” on the display
Ordinary mode
INDOOR UNIT
ADDRESS NO
ERROR CODE
OA UNIT ADDRESS NO
˚C
INDOOR UNIT
ADDRESS NO
ERROR CODE
OA UNIT ADDRESS NO
˚C
ERROR CODE
OA UNIT ADDRESS NO
˚C
1
1
Group setting mode
• Confirm the indoor unit address No.
• Confirm the connection of the transmission line.
ERROR CODE
OA UNIT ADDRESS NO
˚C
ERROR CODE
OA UNIT ADDRESS NO
˚C
• Registration complete
• Registration error
Indicates the type of unit
(Indoor unit in this case)
“88” flashes to indicate
registration error (when
the indoor unit registered
does not exist).
2
Use these
buttons to
assign the
address (
C
).
1
Use these
buttons to
change to the
registration
mode (
A
+
B
).
3
Use this
button to
resister
settings (
D
).
Remote controller
▲
▼
System example
Indoor units
Group
2
+
3
ON/OFF
TEMP
FILTER
CHECK TEST
ON OFF
CLOCK
PAR-F27MEA
TIMER SET