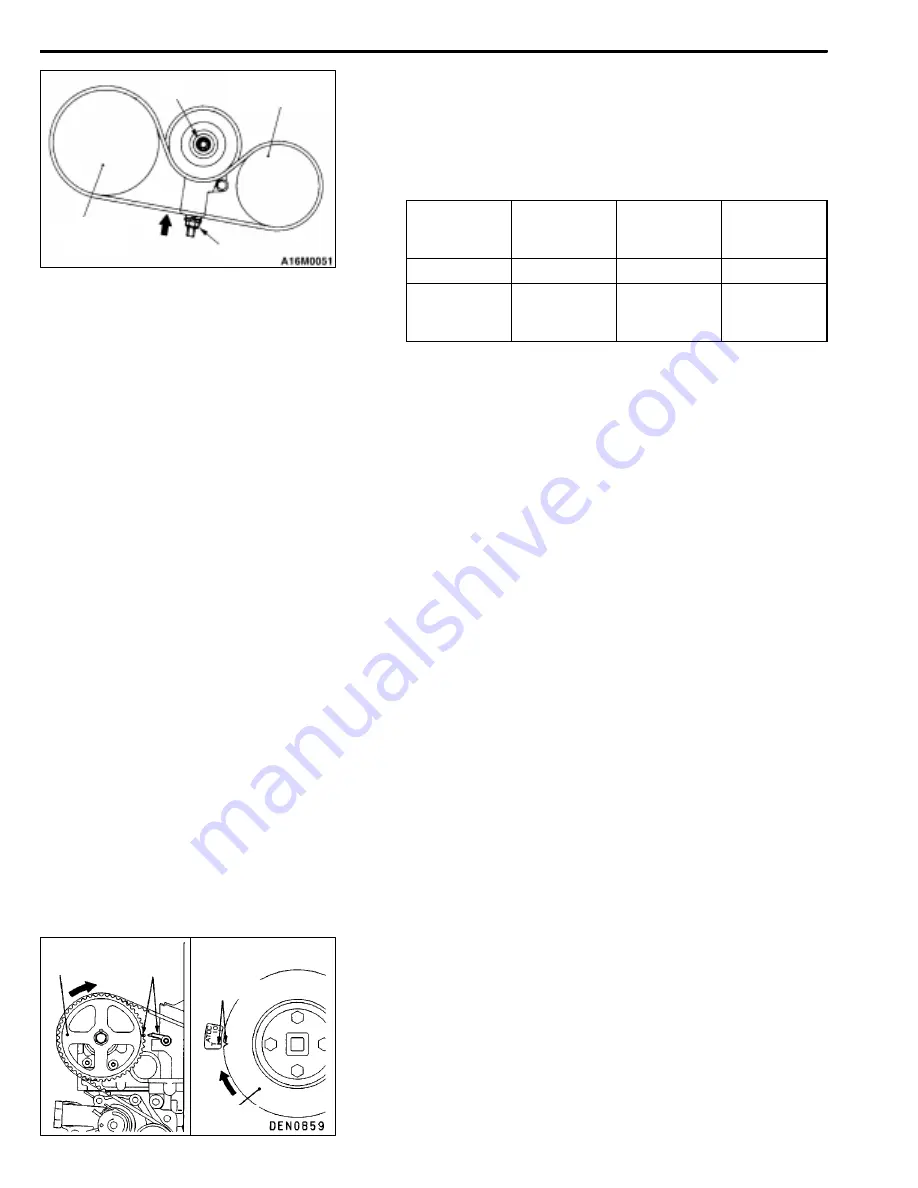
ENGINE <4D6> -
On-vehicle Service
11C-8
COMPRESSOR DRIVE BELT TENSION CHECK AND
ADJUSTMENT
11100100203
1. Check the tension by pulling or pushing at the centre
of the belt between pulleys with a force of 98 N as shown
in the figure. Measure drive belt deflection amount.
Standard value:
Items
When
checked
When a
used belt is
installed
When a new
belt is
installed
Tension N
392 - 588
441 - 539
637 - 833
Deflection
(Reference
value) mm
9.2 - 12.0
9.8 - 11.2
7.0 - 8.6
2. If the tension is outside the standard value, adjust by
the following procedure.
(1) Loosen tensioner pulley fixing nut A.
(2) Adjust the belt tension using adjusting bolt B.
(3) Tighten fixing nut A.
Tightening torque: 25 Nm
(4) Check the belt frequency, tension or deflection, and
readjust if necessary.
Caution
Check after turning the crankshaft once or more
clockwise (right turn).
VALVE CLEARANCE CHECK AND
ADJUSTMENT
11100150130
1. Start the engine and allow it to warm up until the engine
coolant temperature reaches 80 to 95
_
C.
2. Remove the timing belt upper cover.
3. Remove the rocker cover.
4. Remove the glow plug plate and all of the glow plugs.
5. Turn the crankshaft clockwise to align the crankshaft pulley
timing mark and to set the No.1 cylinder or No.4 cylinder
to the compression top dead centre position.
NOTE
Aligning the camshaft sprocket timing mark will set the
No.1 cylinder to the compression top dead centre position.
If the crankshaft is turned one more full revolution from
this position, the No.4 cylinder will be set to the
compression top dead centre position.
A/C compressor
pulley
A
B
Crankshaft
pulley
Camshaft
sprocket
Timing
marks
Timing marks
Crankshaft
pulley