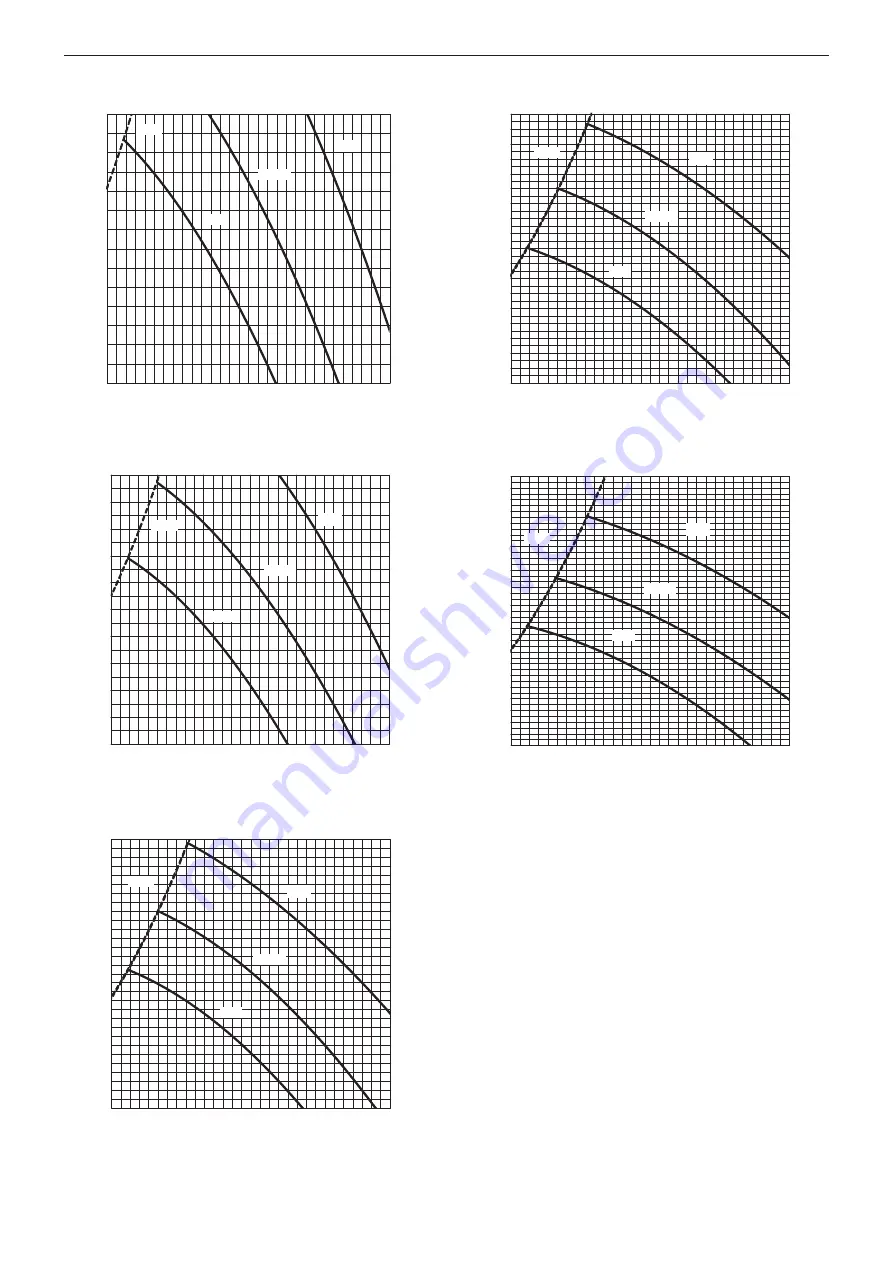
17
HWE1305A
FAN PERFORMANCE AND CORRECTED AIR FLOW
PEY-P36, 42, 48JA(L)(T)
(External static pressure 35Pa) 220-240V 50Hz / 220V 60Hz
0
10
20
30
40
50
60
70
15
20
25
30
35
40
45
Airflow rate(m
3
/min)
E
xt
er
na
l s
ta
tic
pressur
e
(Pa
)
Middle
Low
High
Limit
PEY-P36, 42, 48JA(L)(T)
(External static pressure 50Pa) 220-240V 50Hz / 220V 60Hz
0
10
20
30
40
50
60
70
80
90
100
15
20
25
30
35
40
45
Airflow rate(m
3
/min)
E
xt
er
na
l s
ta
tic
pressur
e
(Pa
)
Middle
Low
High
Limit
PEY-P36, 42, 48JA(L)(T)
(External static pressure 70Pa) 220-240V 50Hz / 220V 60Hz
0
10
20
30
40
50
60
70
80
90
100
110
120
130
140
150
15
20
25
30
35
40
45
Airflow rate(m
3
/min)
E
xt
er
na
l s
ta
tic
pressur
e
(Pa
)
Middle
Low
High
Limit
PEY-P36, 42, 48JA(L)(T)
(External static pressure 100Pa) 220-240V 50Hz / 220V 60Hz
0
10
20
30
40
50
60
70
80
90
100
110
120
130
140
150
160
170
180
15
20
25
30
35
40
45
Airflow rate(m
3
/min)
E
xt
er
na
l s
ta
tic
pressur
e
(Pa
)
Middle
Low
High
Limit
PEY-P36, 42, 48JA(L)(T)
(External static pressure 125Pa) 220-240V 50Hz / 220V 60Hz
0
10
20
30
40
50
60
70
80
90
100
110
120
130
140
150
160
170
180
190
200
210
220
230
15
20
25
30
35
40
45
Airflow rate(m
3
/min)
E
xt
er
na
l s
ta
tic
pressur
e
(Pa
)
Middle
Low
High
Limit