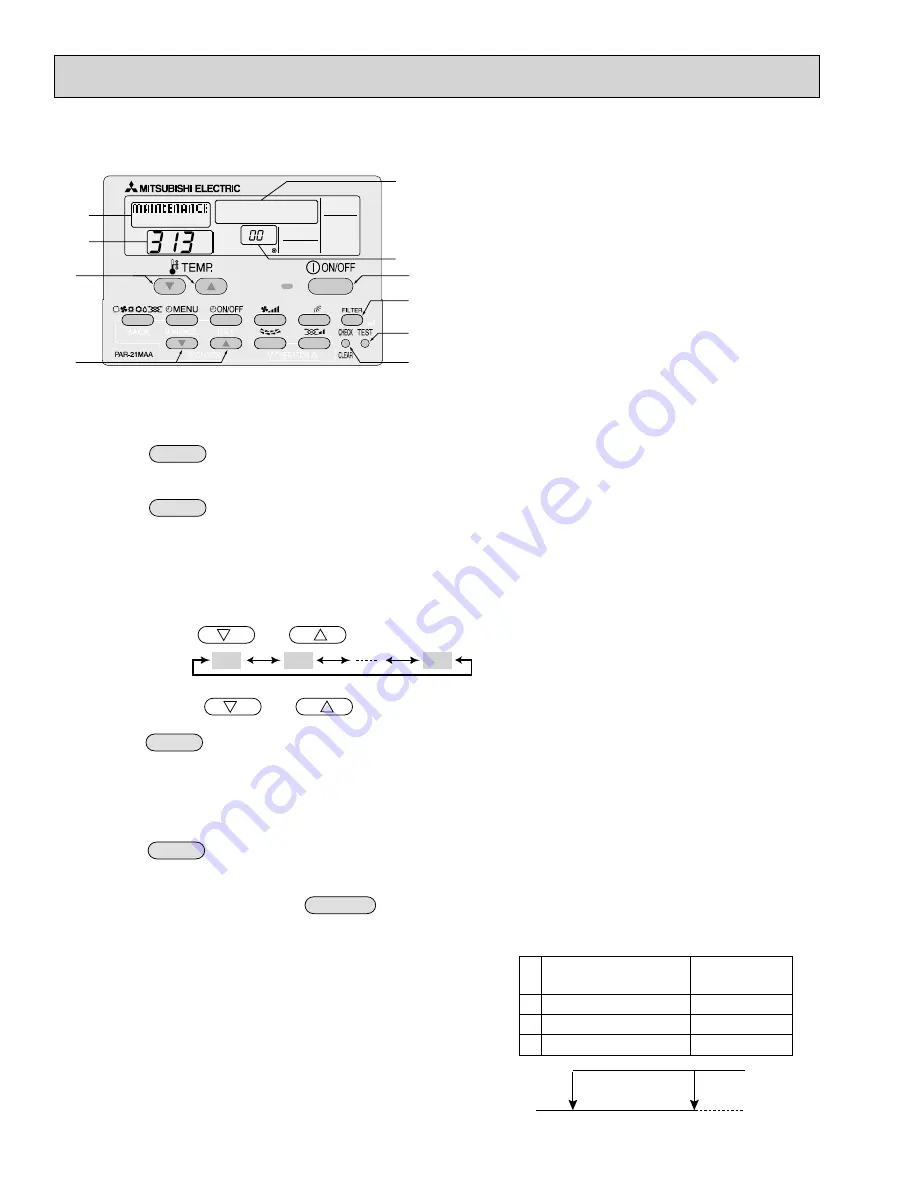
30
(2) Setting method of each function by wired remote controller
B: Refrigerant address
C: Data display area
D: Request code display area
TEST
CHECK
FILTER
FILTER
ON/OFF
1. Stop operation(
).
2. Press the button (
) for 3 seconds so that [Maintenance mode] appears on the screen (
).
After a while, [00] appears in the refrigerant address number display area.(at
)
3. Press the button (
) for 3 seconds to switch to [Maintenance monitor].
Note) It is not possible to switch to [Maintenance monitor] during data request in maintenance mode
(i.e., while “----” is blinking) since no buttons are operative.
[----] appears on the screen (
) when [Maintenance monitor] is activated.
(The display (
) now allows you to set a request code No.)
4. Press the [TEMP ( and )] buttons (
) to select the desired refrigerant address.
5. Press the [CLOCK ( and )] buttons (
) to set the desired request code No.(“311~318”, “321~324”)
6. Press the button (
) to perform function setting.
If above setting operations are done correctly, "Request code number" will appear in data display area.(
)
[Example: When the "311" of "Request code number" is set, [311] appears on the screen.(
)]
[Refererence]
You can check current "request code number" setting by setting the "request code number"(“310” or “320”) and
pressing the button.(
)
[Example: When the current setting is "Setting No.2(Request code 311)", [311] appears on the screen.(
)]
7. To return to normal mode, press the button (
).
[ScreenB]
10-2. BACK-UP HEATING FUNCTION (CN24)
10-2-1. Operation
Outline of functions
The back-up heater signal is sent out according to the tempera-
ture difference between indoor room temperature and set tem-
perature. This function is available only in heating operation.
10-2-2. How to connect
When connecting to the connector CN24 of the indoor unit, use
PAC-SE56RA-E(optional parts).
Z
0
˚
C(
˚
F)
0 < Z < 2.5
˚
C(4.5
˚
F)
2.5
˚
C(4.5
˚
F)
Z
OFF
Keeping condition
ON
1
2
3
Temperature difference
(Z=Set temp. - Room temp.)
Back-up heater
signal output
Z
0
2.5
˚
C(4.5
˚
F)
OFF
ON