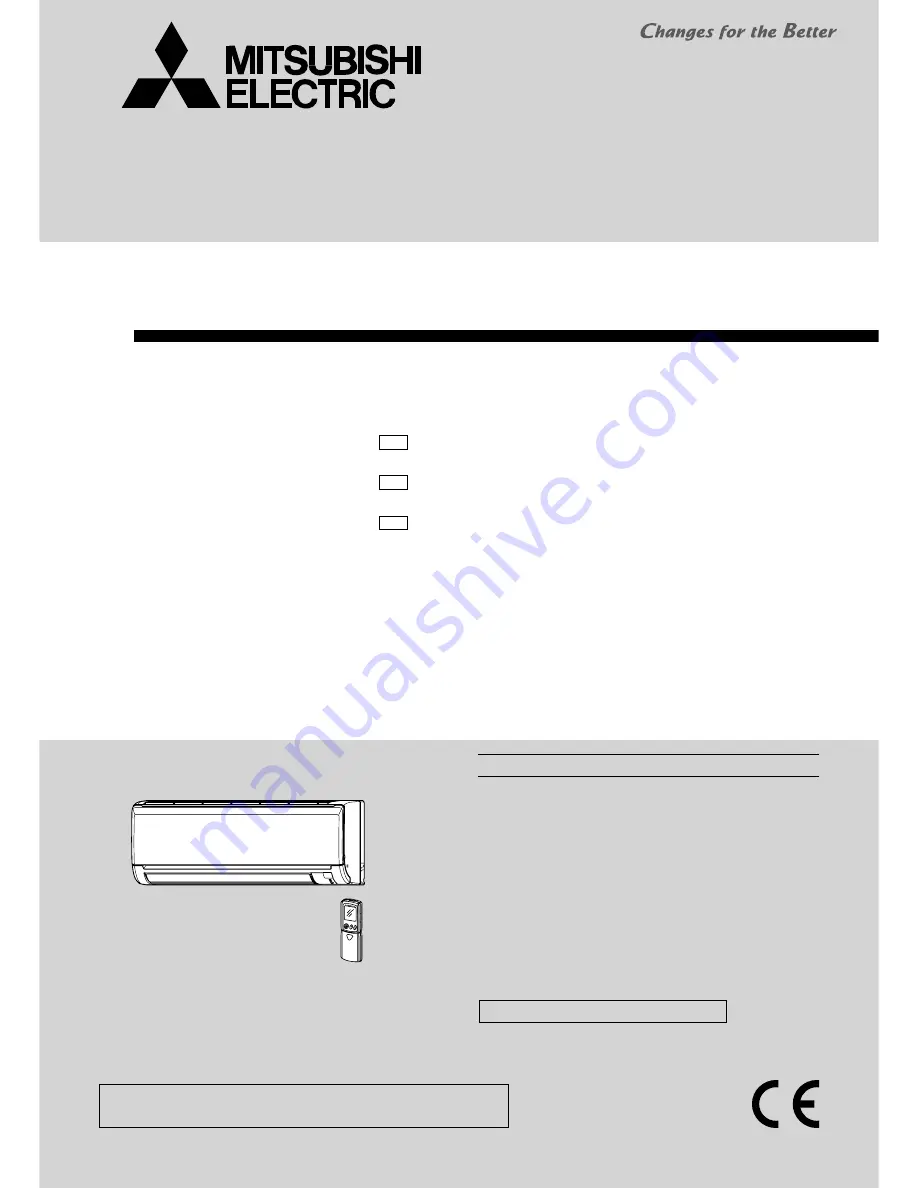
CONTENTS
1. TECHNICAL CHANGES ··································· 2
2. PART NAMES AND FUNCTIONS ····················· 3
3. SPECIFICATION ················································ 4
4. NOISE CRITERIA CURVES ······························ 5
5. OUTLINES AND DIMENSIONS ························ 6
6. WIRING DIAGRAM ············································ 6
7. REFRIGERANT SYSTEM DIAGRAM ··············· 7
8. SERVICE FUNCTIONS ····································· 8
9. MICROPROCESSOR CONTROL ··················· 10
10. TROUBLESHOOTING ····································· 15
11. DISASSEMBLY INSTRUCTIONS ···················· 25
SPLIT-TYPE AIR CONDITIONERS
Outdoor unit service manual
MU-GF·VA Series (OBH622)
SERVICE MANUAL
No. OBH621
INDOOR UNIT
PARTS CATALOG (OBB621)
NOTE:
RoHS compliant products have <G> mark on the spec name plate.
Models
MS-GF20VA
-
E1
MS-GF25VA
-
E1
MS-GF35VA
-
E1