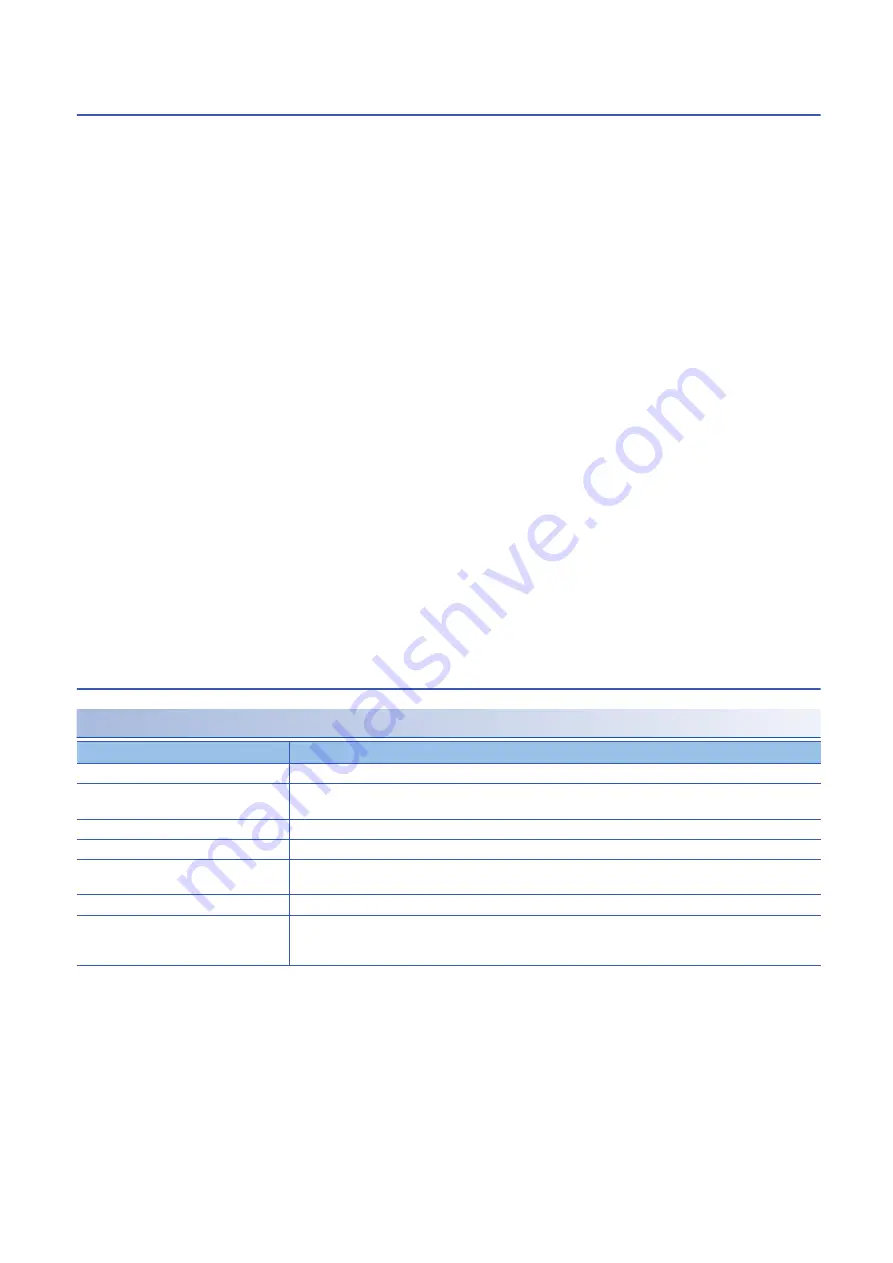
216
8 USING STO FUNCTION [G] [A]
8.1 INTRODUCTION
Residual risks of the STO function
Machine manufacturers are responsible for all risk evaluations and all associated residual risks. Below are residual risks
associated with the STO function. Mitsubishi Electric is not liable for any damages or injuries caused by these risks.
• The STO function disables energy supply to the servo motor by electrical shut-off. The function does not mechanically
disconnect electricity from the motor. Therefore, this function cannot prevent exposure to electric shock. To prevent an
electric shock, install a magnetic contactor or a molded-case circuit breaker to the main circuit power supply (L1/L2/L3) of
the servo amplifier.
• The STO function disables energy supply to the servo motor by electrical shut-off. It does not guarantee stop control or
deceleration control of the servo motor.
• For proper installation, wiring, and adjustment, thoroughly read the installation guide of each individual safety related
component.
• In the safety circuit, use components that are confirmed safe or meet the required safety standards.
• The STO function does not guarantee that the drive part of the servo motor will not rotate due to external or other forces.
• Safety is not assured until safety-related components of the system are completely installed or adjusted.
• When replacing this servo amplifier, confirm that the new servo amplifier is exactly the same model as that being replaced.
Once installed, make sure to verify the performance of the functions before commissioning the system.
• Perform all risk assessments to the machine or the entire system.
• To prevent accumulation of malfunctions, perform function checks at regular intervals based on the risk assessments of the
machine or the system. Regardless of the system safety level, malfunction checks should be performed at least once per
year.
• If the upper and lower power modules in the servo amplifier are shorted and damaged simultaneously, the servo motor may
make a half revolution at a maximum. For a linear servo motor, the primary side will move the distance of the pole pitch.
• The STO input signals (STO1, STO2) must be supplied from one power source. Otherwise, the STO function may not
function properly due to a sneak current, failing to bring the STO shut-off state.
• For the I/O signals of the STO function, supply power by using a safety extra low voltage (SELV) power supply with the
reinforced insulation.
Specifications
Specifications
*1 This is the value required by safety standards.
*2 The safety level depends on the setting value of [Pr. PF18 STO diagnosis error detection time] and whether STO input diagnosis by
TOFB output is performed or not. For details, refer to [Pr. PF18] in the following user's manual.
MR-J5-G/MR-J5W-G User's Manual (Parameters)
MR-J5-A User's Manual (Parameters)
Item
Specifications
Functional safety
STO (IEC/EN 61800-5-2)
Safety performance (Standards certified by
CB)
EN ISO 13849-1:2015 Category 3 PL e, IEC 61508 SIL 3, EN 62061 SIL CL3, EN 61800-5-2
Mean time to dangerous failure (MTTFd)
MTTFd ≥ 100 [years] (314a)
Diagnostic coverage (DC)
DC = Medium, 97.6 [%]
Probability of dangerous Failure per Hour
(PFH)
PFH = 6.4
10
-9
[1/h]
Number of on/off times of STO
1,000,000 times
CE marking
LVD: EN 61800-5-1
EMC: EN 61800-3
MD: EN ISO 13849-1:2015, EN 61800-5-2, EN 62061