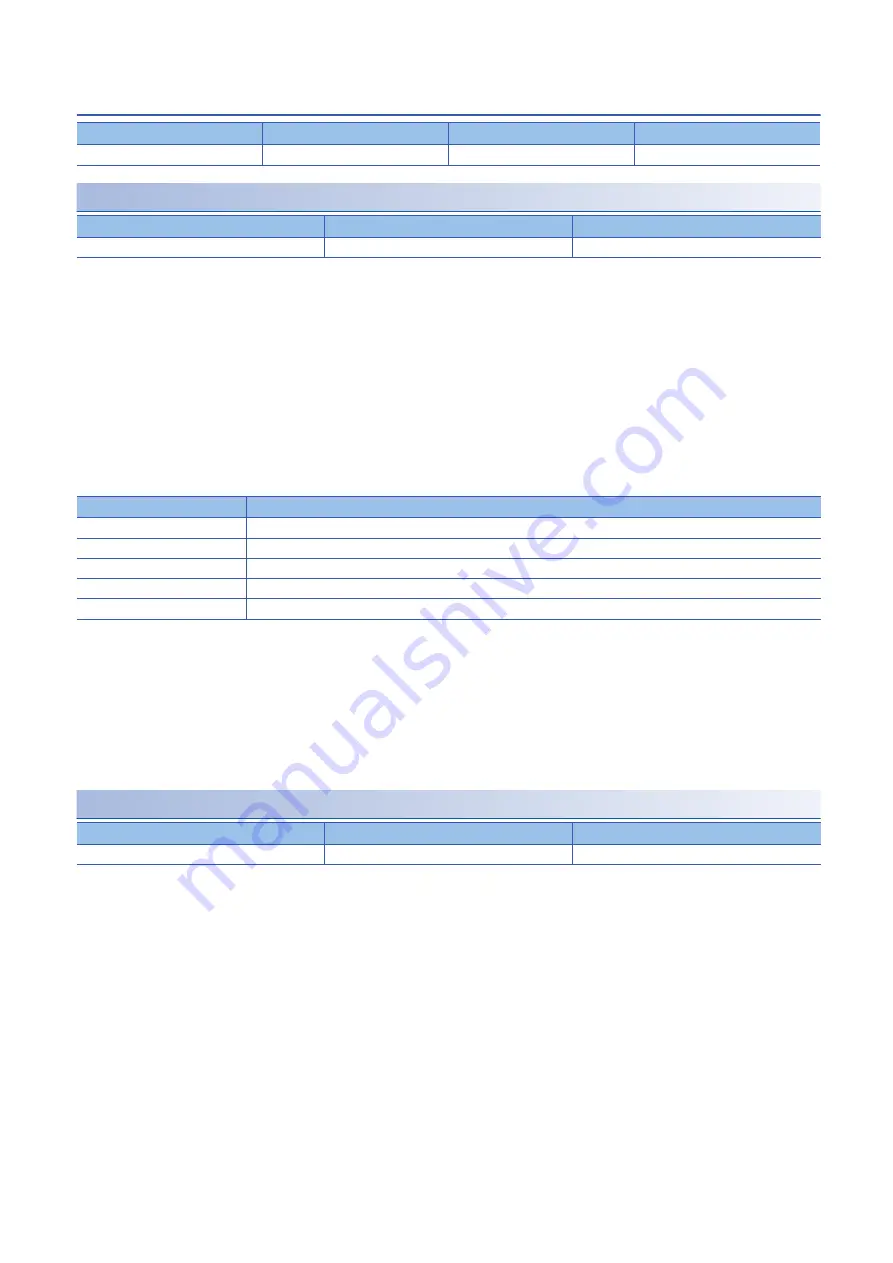
174
1 SERVO PARAMETER DETAILS
1.9 Positioning control setting servo parameters group ([Pr. PT_ _ ])
[Pr. PT68_Function selection T-11 (TOP11)]
[Pr. PT68.0_Quick stop method selection]
Select the quick stop method.
In the slave axis torque mode (slt), the servo motor ignores the Quick Stop input and decelerates to a stop in accordance with
the stop command from the master axis regardless of the setting value of this servo parameter. For details, refer to "Master-
slave operation simultaneous stop function" in the User's Manual (Communication Function).
Forced stop deceleration by turning off EM2 (Forced stop 2) is the same as "2" regardless of the setting value of this servo
parameter.
When [Pr. PA04.3 Forced stop deceleration function selection] is set to "0" (forced stop deceleration function disabled), the
servo motor stops with the dynamic brake regardless of the setting value of this servo parameter.
This function corresponds to [Quick stop option code (Obj. 605Ah)].
When the object is mapped to the cyclic communication, do not write values with engineering tools because the controller
overwrites the servo parameter values written with engineering tools.
*1 Available on servo amplifiers with firmware version D0 or later.
*2 Not available for CC-Link IE Field Network Basic.
*3 For the deceleration time constants of the control modes, refer to "[Quick stop option code (Obj. 605Ah)]" in the User's Manual (Object
Dictionary).
*4 When the controller being used cannot perform follow-up in the "Quick stop active" state (during servo-on), do not use this setting value
in the cyclic synchronous position mode (csp). For information on whether the controller being used can perform follow-up in the "Quick
stop active" state, refer to the manual for the controller.
*5 When canceling Quick stop in the cyclic synchronous position mode (csp), cancel it after servo-off or perform position follow-up with the
controller. If Quick stop is canceled without performing position follow-up, the servo motor may suddenly accelerate.
[Pr. PT68.2_Temporary stop method selection]
Select a temporary stop method.
0: Automatic selection (deceleration to a stop method)
1: Deceleration to a stop method
This function corresponds to [Halt option code (Obj. 605Dh)].
When the object is mapped to the cyclic communication, do not write values with engineering tools because the controller
overwrites the servo parameter values written with engineering tools.
Initial value
Setting range
Setting method
Ver.
00000002h
Refer to the relevant detail No.
Each axis
Refer to the relevant detail No.
Initial value
Setting range
Ver.
2h
Refer to the text
A0
Setting value
Description
Stop with dynamic brake
Servo-off after deceleration to a stop at the deceleration time constant of any of the control modes
2
Servo-off after deceleration to a stop with [Quick stop deceleration (Obj. 6085h)]
Maintain servo-on after deceleration to a stop at the deceleration time constant of any of the control modes
Maintain servo-on after deceleration to a stop with [Quick stop deceleration (Obj. 6085h)]
Initial value
Setting range
Ver.
0h
Refer to the text
A0