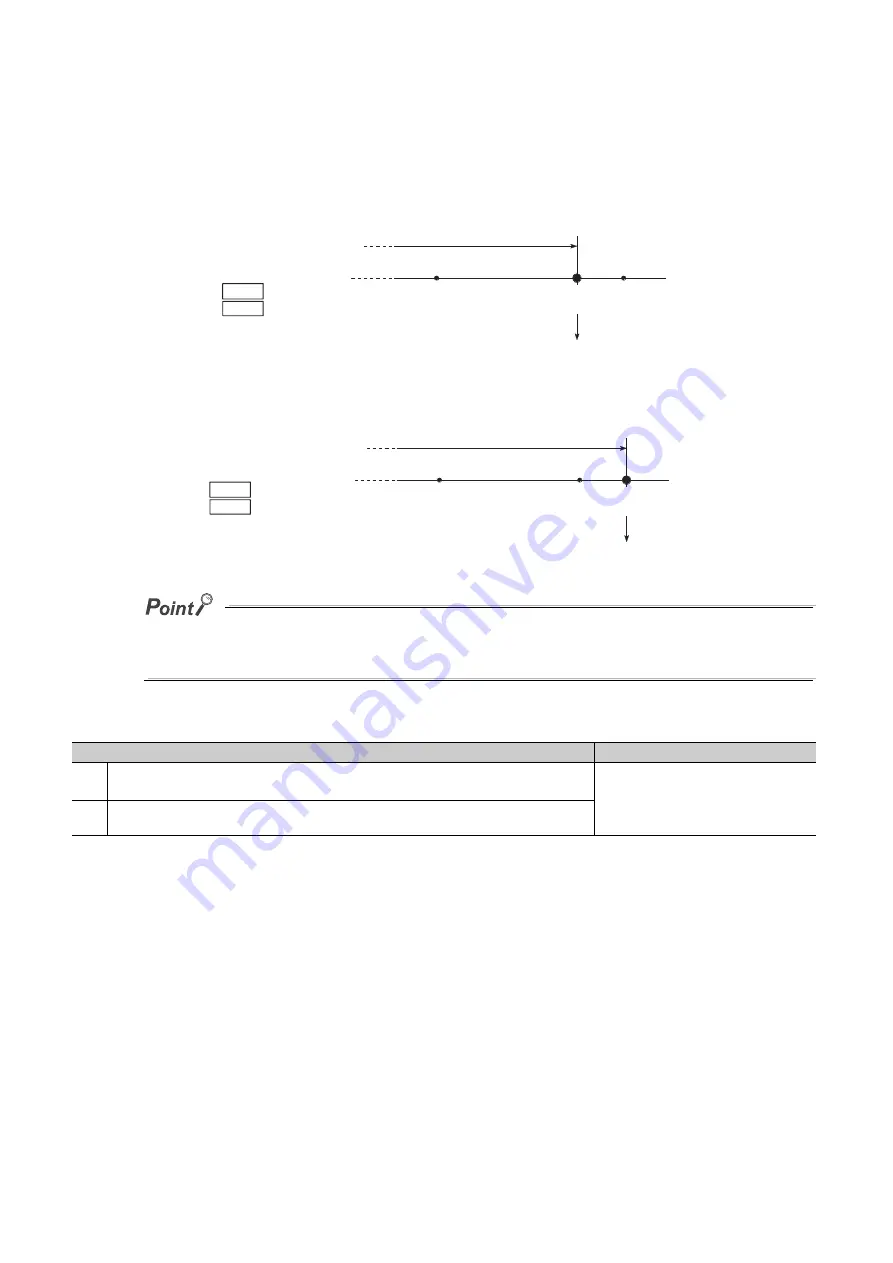
536
[Current value changing]
When the current value is changed by a new current value command from 2000 to 1000, the current value will
change to 1000, but the machine feed value will stay the same at 2000.
• When the machine feed value is set at the limit, the machine feed value of 5000 (current feed value: 4000)
becomes the upper stroke limit.
• When the current feed value is set at the limit, the current feed value of 5000 (machine feed value: 6000)
becomes the upper stroke limit.
When "machine feed value" is set in "[Pr.14] Software stroke limit selection", the moveable range becomes an absolute
range referenced on the OP. When "current feed value" is set, the moveable range is the relative range from the "current
feed value".
(2) Software stroke limit check details
*1
Check whether the "[Md.20] Current feed value" or "[Md.21] Machine feed value" is set in "[Pr.14] Software stroke limit
selection".
*2
Moveable range from the "[Pr.12] Software stroke limit upper limit value" to the "[Pr.13] Software stroke limit lower limit
value".
Check details
Processing whenan error occurs
1)
An error shall occur if the current value
is outside the software stroke limit range
.
(Check "[Md.20] Current feed value" or "[Md.21] Machine feed value".)
An "axis error" will occur
(The error "Software stroke limit +" or
"Software stroke limit –" (error code: 507 or
508) will occur.)
2)
An error shall occur if the command address is outside the software stroke limit range.
(Check " Da.6 Positioning address/movement amount".)
4000
5000
5000
6000
Upper stroke limit
1000
2000
Moveable range
Md. 20 Current feed value
Md. 21 Machine feed value
4000
5000
5000
6000
Upper stroke limit
1000
2000
Moveable range
Md. 20 Current feed value
Md. 21 Machine feed value
Summary of Contents for MELSEC-L LD75D
Page 2: ......
Page 11: ...9 Memo ...
Page 176: ...174 ...
Page 264: ...262 ...
Page 266: ...264 ...
Page 267: ...265 CHAPTER 6 PROGRAM USED FOR POSITIONING CONTROL 6 6 4 Positioning Program Examples ...
Page 268: ...266 ...
Page 269: ...267 CHAPTER 6 PROGRAM USED FOR POSITIONING CONTROL 6 6 4 Positioning Program Examples ...
Page 270: ...268 ...
Page 271: ...269 CHAPTER 6 PROGRAM USED FOR POSITIONING CONTROL 6 6 4 Positioning Program Examples ...
Page 272: ...270 Z ABRST1 instruction execution ...
Page 273: ...271 CHAPTER 6 PROGRAM USED FOR POSITIONING CONTROL 6 6 4 Positioning Program Examples ...
Page 278: ...276 ...
Page 279: ...277 CHAPTER 6 PROGRAM USED FOR POSITIONING CONTROL 6 6 4 Positioning Program Examples ...
Page 280: ...278 ...
Page 281: ...279 CHAPTER 6 PROGRAM USED FOR POSITIONING CONTROL 6 6 4 Positioning Program Examples ...
Page 282: ...280 ...
Page 283: ...281 CHAPTER 6 PROGRAM USED FOR POSITIONING CONTROL 6 6 4 Positioning Program Examples ...
Page 284: ...282 ...
Page 285: ...283 CHAPTER 6 PROGRAM USED FOR POSITIONING CONTROL 6 6 4 Positioning Program Examples ...
Page 286: ...284 ...
Page 287: ...285 CHAPTER 6 PROGRAM USED FOR POSITIONING CONTROL 6 6 4 Positioning Program Examples ...
Page 316: ...314 Memo ...
Page 685: ...683 APPENDICES A Appendix 1 Function Update Appendix 1 1 Function comparison Memo ...
Page 738: ...736 Memo ...
Page 817: ......