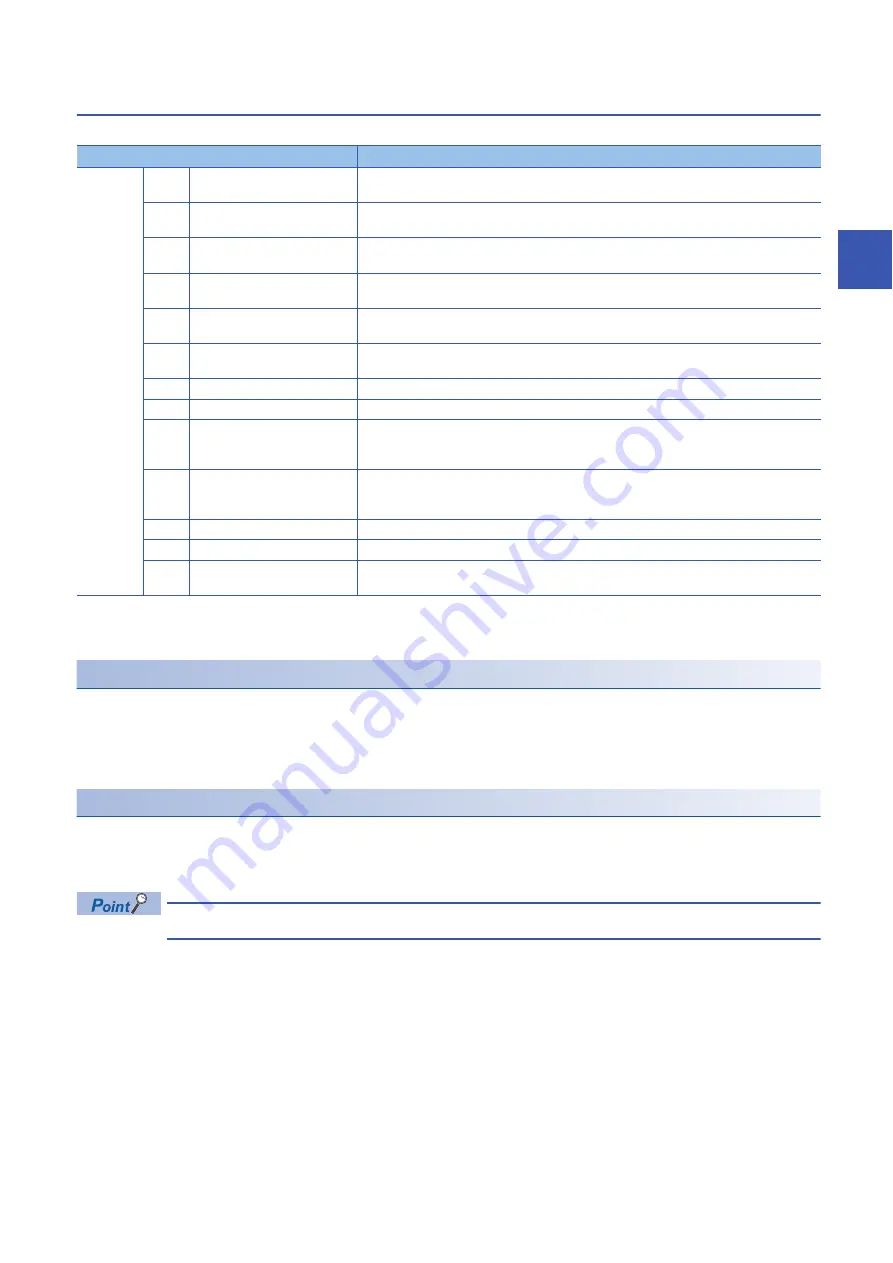
3 MAJOR POSITIONING CONTROL
3.1 Overview of the Major Positioning Controls
61
3
Data required for major positioning control
The following table lists Positioning data required for performing Major positioning control.
The settings of [Da.1] to [Da.10] and [Da.27] to [Da.29] differ depending on the setting of [Da.2] Control method. (
Sub functions for major positioning control
For details on the sub functions that can be combined with the major positioning control, refer to the following.
MELSEC iQ-R Positioning Module User's Manual (Startup)
For details on each sub function, refer to the following.
MELSEC iQ-R Positioning Module User's Manual (Startup)
Major positioning control from an engineering tool
Major positioning controls can be executed using the positioning test of the engineering tool. For details on the positioning
test, refer to the following.
Up to 600 positioning data (Positioning data No.1 to 600) can be set for each axis.
Setting item
Setting detail
Positioning
data
[Da.1]
Operation pattern
Set an operation pattern for the continuous positioning data (example: Positioning data No.1 to 3).
(
Page 62 Operation pattern of major positioning control)
[Da.2]
Control method
Set a control method defined for Major positioning control used. (
[Da.3]
Acceleration time No.
Select and set an acceleration time at the start of the control. (Select one from four values set in
[Pr.9], [Pr.25], [Pr.26], and [Pr.27] as the acceleration time.)
[Da.4]
Deceleration time No.
Select and set a deceleration time at the stop of the control. (Select one from four values set in
[Pr.10], [Pr.28], [Pr.29], and [Pr.30] as the deceleration time.)
[Da.5]
Axis to be interpolated
Set a target axis (partner axis) for the 2-axis interpolation control, and a circular interpolation axis
for the 3-axis helical interpolation control. (
Page 77 Interpolation control)
[Da.6]
Positioning address/movement
amount
Set a target value for the position control. (
Page 71 Specifying the positioning address)
[Da.7]
Arc address
Set a sub point or a center point address for the circular interpolation control.
[Da.8]
Command speed
Set the speed at the execution of the control.
[Da.9]
Dwell time
The time from when the command pulse output is completed to when Positioning complete signal
is turned on. Set this time to absorb the delay of machine systems to the command, such as the
delay (deviation) of the servo system.
[Da.10]
M code
Set an M code to issue a command for a subsidiary work (such as stopping clamps or drills and
changing tools) corresponding to each M code number that can be related to the execution of the
positioning data.
[Da.27]
M code ON signal output timing
Set the M code ON signal output timing for each positioning data.
[Da.28]
ABS direction in degrees
Set the ABS direction in degrees for each positioning data.
[Da.29]
Interpolation speed specification
method
Set the interpolation speed specification method for each positioning data.
Summary of Contents for MELSEC iQ-R RD75P4
Page 1: ...MELSEC iQ R Positioning Module User s Manual Application RD75P2 RD75P4 RD75D2 RD75D4 ...
Page 2: ......
Page 13: ...11 MEMO ...
Page 19: ...17 CONTENTS INDEX 588 REVISIONS 592 WARRANTY 593 TRADEMARKS 594 ...
Page 498: ...496 13 PROGRAMMING 13 2 List of Labels Used ...
Page 503: ...13 PROGRAMMING 13 4 Program Example 501 13 ...
Page 514: ...512 13 PROGRAMMING 13 4 Program Example Restart program Parameter data initialization program ...
Page 515: ...13 PROGRAMMING 13 4 Program Example 513 13 Flash ROM write program Error reset program ...
Page 516: ...514 13 PROGRAMMING 13 4 Program Example Stop program ...
Page 565: ...APPENDICES Appendix 4 Operation Examples of When the Remote Head Module Is Mounted 563 A ...
Page 597: ......