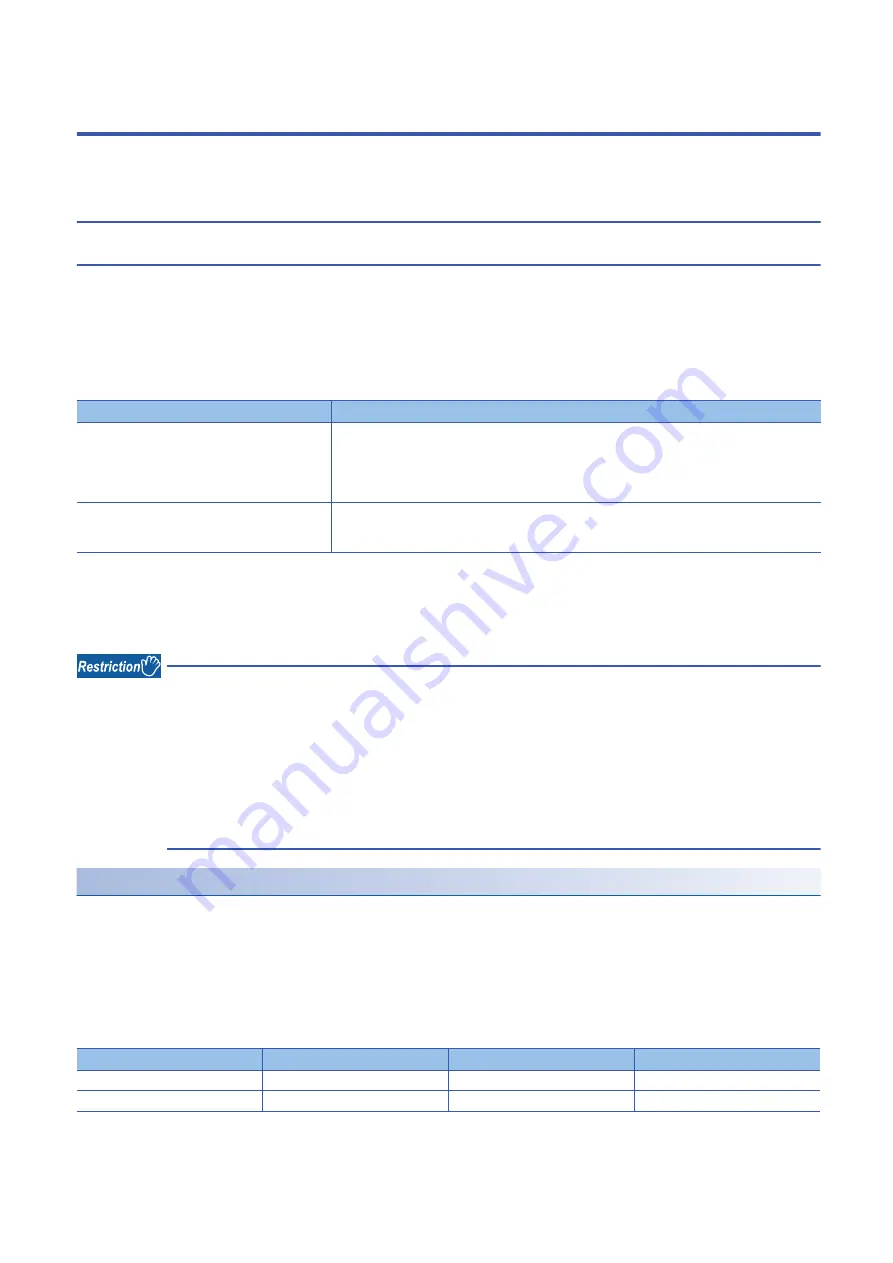
38
2 OPR CONTROL
2.1 Overview of the OPR Control
2
OPR CONTROL
This chapter describes the details and usage of the OPR control.
2.1
Overview of the OPR Control
Two types of OPR controls
The OPR control establishes a start point (= OP) for performing the positioning control, and performs positioning toward that
start point. This control is used to return the machine system located at a position other than the OP to the OP when the RD75
issues an OPR request with the power turned on or after the positioning stops.
In the RD75, the two types of controls shown below are defined as OPR control, following the flow of the OPR work. These
two types of OPR controls can be executed by setting OPR parameter, setting Positioning start No.9001 and Positioning start
No.9002 originally prepared for the RD75 in [Cd.3] Positioning start No., and turning on Positioning start signal.
The OPR control can be performed by setting 9001 or 9002 for the start No. of the dedicated instruction GP.PSTRT
. For
details on the dedicated instructions, refer to the following.
MELSEC iQ-R Programming Manual (Instructions, Standard Functions/Function Blocks)
To perform Fast OPR, perform Machine OPR beforehand.
In the following cases, the RD75 turns on OPR request flag ([Md.31] Status: b3), which indicates that the
machine OPR needs to be performed.
• When the power is turned on
• When Drive unit READY signal ([Md.30] External I/O signal: b2) turns off
• When PLC READY signal [Y0] is turned off and on
While OPR request flag is on, the address information stored in the RD75 is not guaranteed. When the
execution of the machine OPR is normally completed, OPR request flag turns off and OPR complete flag
([Md.31] Status: b4) turns on.
Sub functions specific to OPR
For details on Sub functions that can be combined with the OPR control, refer to the following.
MELSEC iQ-R Positioning Module User's Manual (Startup)
For details on each sub function, refer to the following.
Page 209 CONTROL SUB FUNCTIONS
[Information]
The following two sub functions are only related to the machine OPR.
: Combination possible,
: Combination limited,
: Combination not possible
OPR method
Description
Machine OPR (Positioning start No.9001)
Performs the OPR operation to establish a machine OP position. Subsequent positioning control
operations are performed with reference to the OP established after the OPR operation is completed.
When the system is powered on and a machine OP has yet to be established (the current value that the
RD75 monitors and the actual machine position do not match), the machine OPR is required to be
performed.
Fast OPR (Positioning start No.9002)
Performs the positioning toward the OP established by the machine OPR. Specifying positioning start
No.9002 performs the fast OPR. Thus, the positioning to the OP can be performed without setting
positioning data.
Sub function name
Machine OPR
Fast OPR
Reference
OPR retry function
OP shift function
Summary of Contents for MELSEC iQ-R RD75P4
Page 1: ...MELSEC iQ R Positioning Module User s Manual Application RD75P2 RD75P4 RD75D2 RD75D4 ...
Page 2: ......
Page 13: ...11 MEMO ...
Page 19: ...17 CONTENTS INDEX 588 REVISIONS 592 WARRANTY 593 TRADEMARKS 594 ...
Page 498: ...496 13 PROGRAMMING 13 2 List of Labels Used ...
Page 503: ...13 PROGRAMMING 13 4 Program Example 501 13 ...
Page 514: ...512 13 PROGRAMMING 13 4 Program Example Restart program Parameter data initialization program ...
Page 515: ...13 PROGRAMMING 13 4 Program Example 513 13 Flash ROM write program Error reset program ...
Page 516: ...514 13 PROGRAMMING 13 4 Program Example Stop program ...
Page 565: ...APPENDICES Appendix 4 Operation Examples of When the Remote Head Module Is Mounted 563 A ...
Page 597: ......