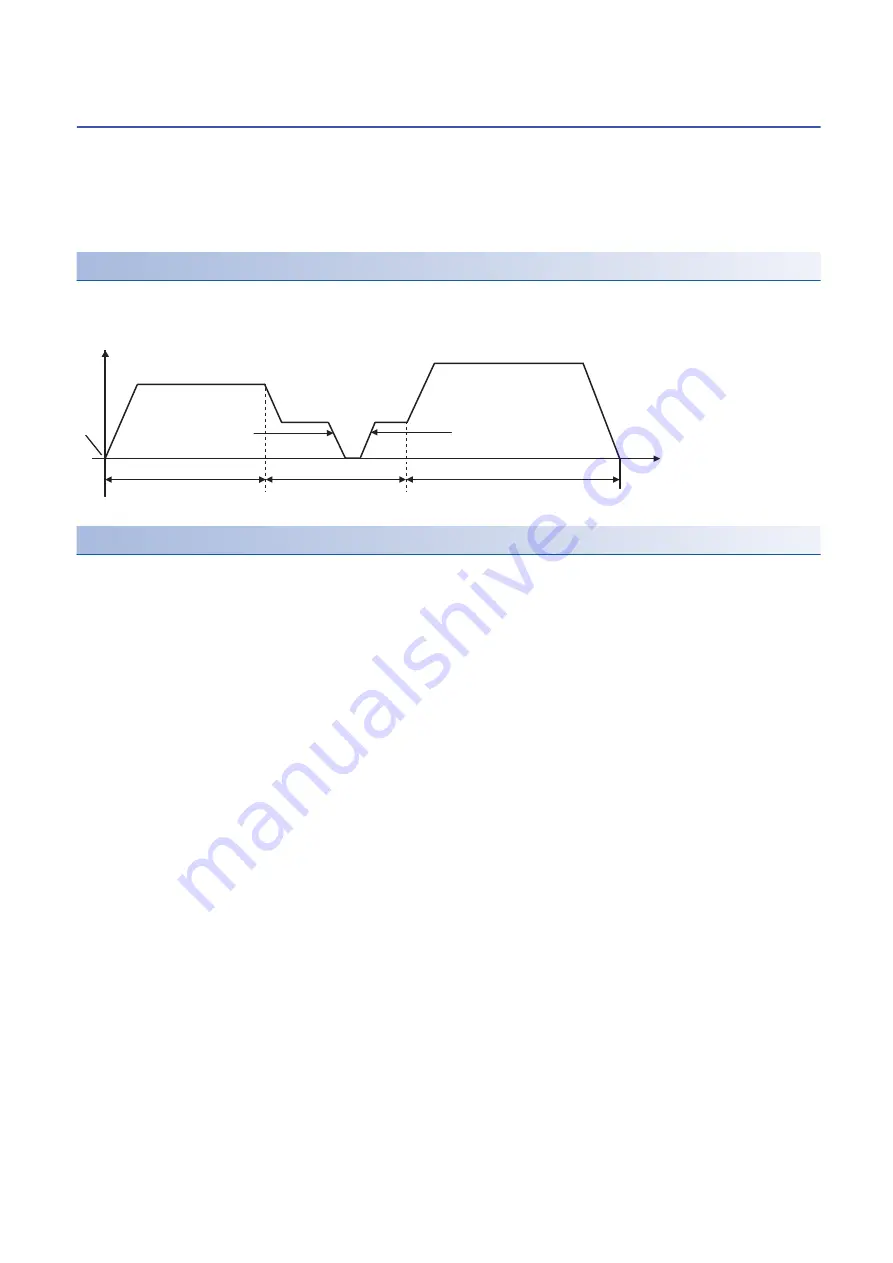
36
1 STARTING AND STOPPING
1.3 Restarting
1.3
Restarting
If the positioning control is stopped by a stop command (Axis stop signal [Y4, Y5, Y6, Y7] or a stop signal from an external
device), the positioning can be restarted from the stopped position to the end point of the position control by using [Cd.6]
Restart command. (However, restarting is not possible when the continuous operation is interrupted.)
This command is useful when performing the remaining positioning from the stopped position during the position control of the
incremental system such as the INC linear 1. (The remaining distance does not need to be calculated.)
Operation
After a deceleration stop by a stop command is completed, write 1 to [Cd.6] Restart command while [Md.26] Axis operation
status is Stopped. The positioning restarts.
Restrictions
• Restarting can be executed only when [Md.26] Axis operation status is Stopped (the deceleration stop by the stop
command is completed). If [Md.26] Axis operation status is not Stopped, Restart not possible (Warning code: 0902H)
occurs and restarting is not executed. The processing at that time will be continued.
• Restarting can be executed even while Positioning start signal is ON. However, do not turn off and on Positioning start
signal while [Md.26] Axis operation status is Stopped. If Positioning start signal is turned off and on while [Md.26] Axis
operation status is Stopped, the normal positioning (using the positioning data set in [Cd.3] Positioning start No.) is started.
• If PLC READY signal is turned off and on while [Md.26] Axis operation status is Stopped, the positioning control cannot be
restarted. If a restart request is issued, Restart not possible (Warning code: 0902H) occurs.
• Do not execute restarting while the stop command is on. If restarting is attempted while the stop command is on, Stop
signal ON at start (Error code: 1908H or 1909H) occurs and [Md.26] Axis operation status turns to Error. In this case, even
if the error is reset, the operation cannot be restarted.
• If the positioning is ended with the continuous operation interrupt request, the operation cannot be restarted. If a restart
request is issued, Restart not possible (Warning code: 0902H) occurs.
• When the positioning has been stopped with the interpolation operation, write 1: Restart into [Cd.6] Restart command for
the reference axis and restart the positioning.
• If any of the reference partner axes executes the positioning operation once, Restart not possible (Warning code: 0902H)
occurs, and the positioning cannot be restarted.
• When the machine OPR and fast OPR is stopped, OPR restart not possible (Error code: 1946H) occurs and the positioning
cannot be restarted.
• When the manual operation is stopped, Restart not possible (Warning code: 0902H) occurs and the positioning cannot be
restarted.
V
t
Start
Positioning data No.10
Positioning data No.11
Positioning data No.12
Stop processing
with the stop command
Positioning data No.11
proceeds with the restart
command
Summary of Contents for MELSEC iQ-R RD75P4
Page 1: ...MELSEC iQ R Positioning Module User s Manual Application RD75P2 RD75P4 RD75D2 RD75D4 ...
Page 2: ......
Page 13: ...11 MEMO ...
Page 19: ...17 CONTENTS INDEX 588 REVISIONS 592 WARRANTY 593 TRADEMARKS 594 ...
Page 498: ...496 13 PROGRAMMING 13 2 List of Labels Used ...
Page 503: ...13 PROGRAMMING 13 4 Program Example 501 13 ...
Page 514: ...512 13 PROGRAMMING 13 4 Program Example Restart program Parameter data initialization program ...
Page 515: ...13 PROGRAMMING 13 4 Program Example 513 13 Flash ROM write program Error reset program ...
Page 516: ...514 13 PROGRAMMING 13 4 Program Example Stop program ...
Page 565: ...APPENDICES Appendix 4 Operation Examples of When the Remote Head Module Is Mounted 563 A ...
Page 597: ......