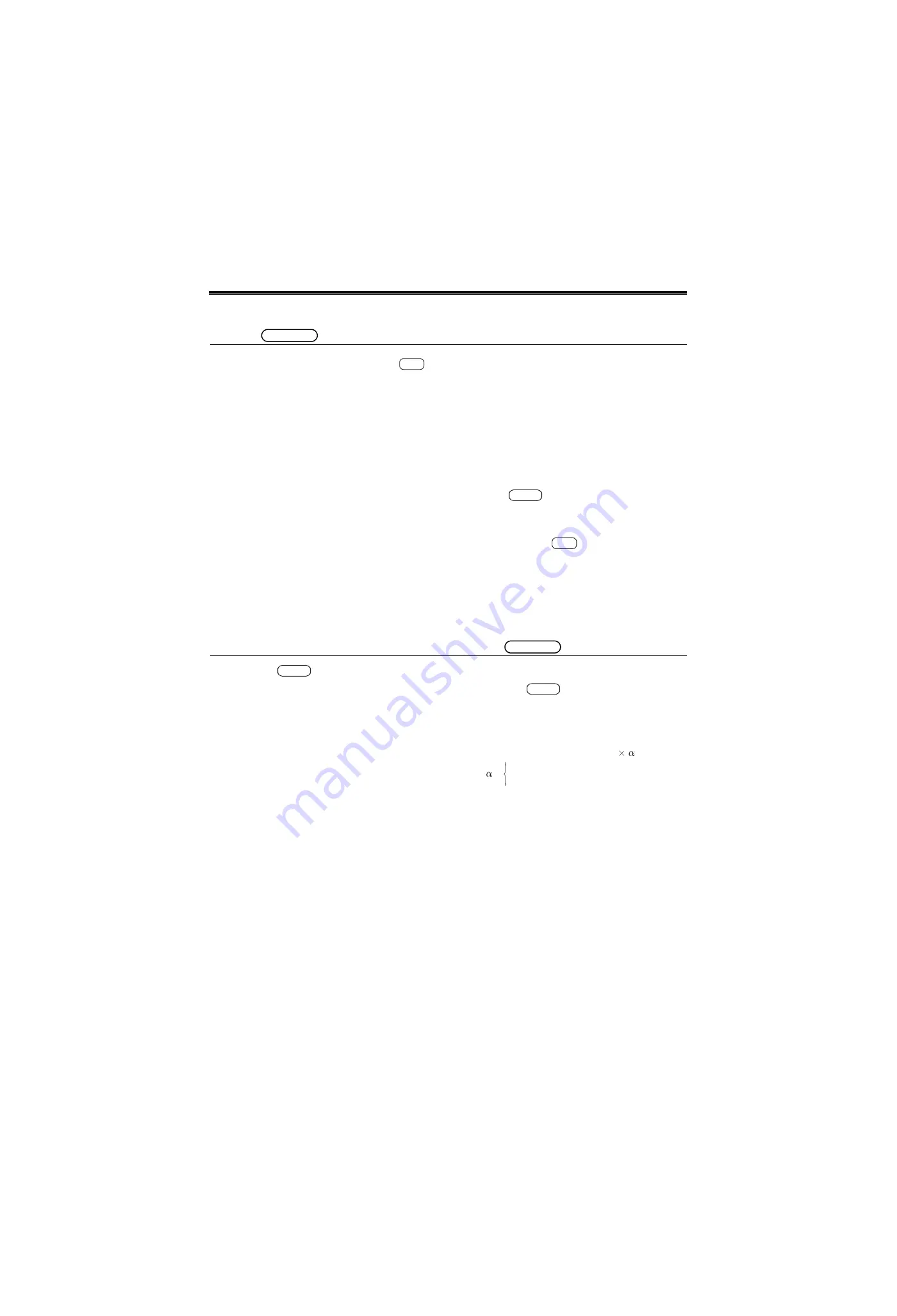
108
SPECIFICATIONS
1.5.6
Brake resistor overheat protection and brake transistor alarm detection
(common)
(1) Brake resistor overheat protection
Any of the inverters 0.4K to 7.5K have a built-in
regenerative brake discharge resistor. This brake
resistor has a heat capacity of 100 to 150% torque
and is used for a short time. (within 5 to 8s
continuously)
If the regenerative brake beyond the above value is
required (the brake transistor ON time has exceeded
the permissible value), the brake resistor overheat
protection is activated to shut off the brake transistor
gate. The regenerative brake may be used again
when the discharge resistor has cooled after the
regenerative brake is shut off.
The heat capacity can be increased by using the
external brake discharging resistor instead. (Refer to
page 489)
The brake resistor overheat protection function is
reset to the initial (cold) state by switching ON the
inverter power or the reset signal (RES signal).
Unnecessary reset and power-OFF should therefore
be avoided. The inverter must not be installed on any
combustible surface, such as wood, because the
temperature of the built-in brake resistor reaches
approximately 200
°
C maximum.
If the brake transistor output voltage becomes
excessive during deceleration, the regenerative
overvoltage protection may be activated to stop the
inverter output.
(2) Brake transistor circuit alarm detection
(BE)
When the regenerative brake transistor has been
damaged due to an external brake discharge resistor
wiring fault etc. (
at internal circuit alarm for
the 55K or less), this function detects the fault, shuts
off the inverter output, and gives the alarm output
signal. When this alarm output signal is provided,
shut off the inverter power supply to protect the
discharge resistor from overheating.
1.5.7
Electronic thermal relay function(THM, THT)
(common)
(1) Function
On detecting the overload of the motor or transistor,
the electronic thermal relay in the inverter stops the
transistor operation and output, and keeps them
stopped.
*1
Protective function by electronic thermal relay function is
reset by inverter power reset and reset signal input.
Avoid unnecessary reset and power-OFF.
*2
When multiple motors are operated by a single inverter,
protection cannot be provided by the electronic thermal
function. Install an external thermal relay to each motor.
*3
A special motor cannot be protected by the electronic
thermal relay function. Use an external thermal relay.
*4
The operation time of the transistor protection thermal
shortens when the [
Pr. 72 PWM frequency selection
] setting
is increased.
(2) Setting the electronic thermal relay
function
Define the protection characteristic of the electronic
thermal relay on the basis of the rated current value
of the motor as indicated below:
Set the value in terms of amperes from the operation
panel (parameter unit). ([
Pr. 9
])
*1
Set 0 in [
Pr. 9
] when you do not want to operate the
electronic thermal relay function when using the motor
with the external thermal relay, etc. (Note that the output
transistor protection (E.THT) of the inverter functions.)
*2
Since a thermal relay protector is built in a motor
dedicated for vector control (SF-V5RU), set [
Pr. 9
= 0] to
use the motor.
*3
When a difference between the inverter and motor
capacities is large and the setting is small, the protective
characteristics of the electronic thermal relay function will
be deteriorated. In this case, use an external thermal
relay.
*4
Electronic thermal relay may not function when 5% or
less of inverter rated current is set to electronic thermal
relay setting.
common
A700
common
F700
common
common
Setting value = rated current value (A)
:
200V(400V) 50Hz ................................. 1.0
200/220V(400/440V) 60Hz ...................1.1
common
Summary of Contents for FR-A700 Series
Page 245: ...279 2 PARAMETER PARAMETER MEMO ...
Page 440: ...474 PARAMETER MEMO ...
Page 522: ...556 SELECTION MEMO ...