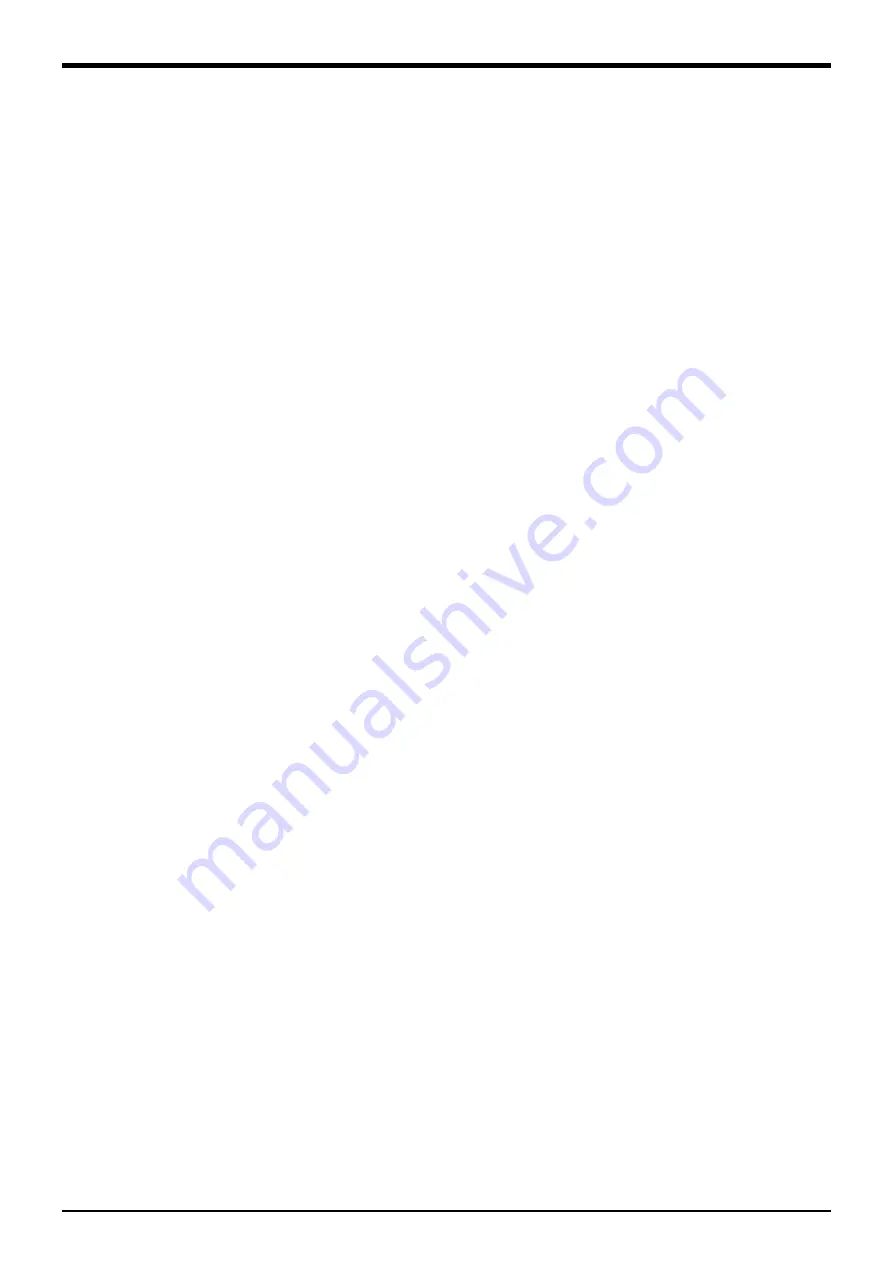
8 Calibration of Conveyer and Robot Coordinate Systems (“A1” program)
8-56 Confirmation after operation
(13)
Press [F1] (FWD) key and execute step feed
“(8)
Perform step operation…”
is displayed.
Perform step operation until “End.”
* The amount of robot movement per encoder pulse is calculated based on this operation.
8.3.
Confirmation after operation
Check the value of “P_EncDlt” using T/B.
* This value indicates the movement of each coordinate (mm) of the robot coordinate system,
corresponding to the movement of the conveyer per pulse.
Example
)
If ”0.5” is displayed for the Y coordinate only
This means that if the conveyer moves for 100 pulses, the workpiece moves 50 mm (0.5 x 100 = 50)
in the +Y direction in the robot coordinate system.
When backing up, the data of “P_EncDlt" is not backed up.
Please work referring to "16.6
Restore backup data to another controller" when you restore data to another
tracking system.
8.4.
When multiple conveyers are used
Carry out the same operations as above when multiple conveyers are used as well, but pay attention to the
following points.
Example
)
When using conveyer 2 (enc
oder number “
2”
),
(a) Copy the “
A1”
program, please create a “
A2”
program.
(b)
Please change the encoder number for variable
“
MEncNo”
in the “
A2”
program to “
2”
.
Summary of Contents for CR800 Series
Page 2: ......
Page 12: ......
Page 202: ...18 Appendix 18 190 Calibration sheet ...
Page 203: ......