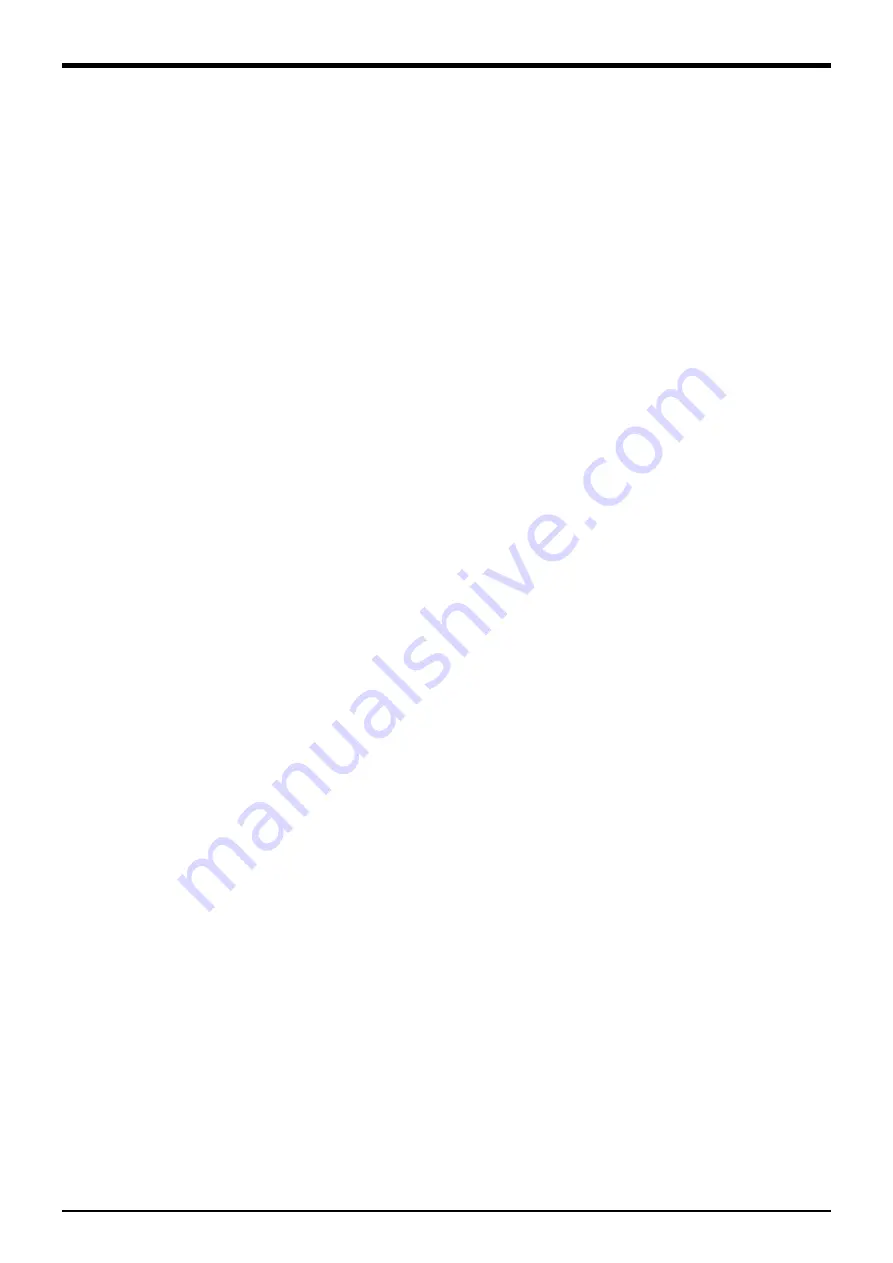
16 In such a case (improvement example)
16-176 Make adsorption and release of the work speedy
(3)
Please change the on timing of a sensor by m
aking reference to "
".
When it can't be settled, it's to the next.
(4)
Please confirm whether the timing a stock sensor t
urns on is right.
When being not right, please do a sensitivity adjustment of a sensor. When being right, it's to the next.
(5)
Please confirm the state variable "P_CvSpd (<Logic encoder number>)" using a variable monitor of RT
ToolBox3, and confirm whether conveyor speed isn't changing extremely.
When there is an extreme change, please confirm whether there isn't influence of noise.
When noise doesn't influence, it's to the next.
(6)
There is a possibility that the encoder value was abnormal or a possibility that the price of the state variable
"M_EncStart" and "M_EncStop" was changed after instruction work in instruction work by a program "A1".
Please p
ut "
)" into effect again.
16.4.
Make adsorption and release of the work speedy
Adjust the adjustment variable "PDly1", and the value of X coordinates of "PDly2" of the program 1.
Refer to
1 List of adjustment variables in the program
" (high speed and accuracy tracking) or "Table
List of variable for operating conditions" (circular arc tracking) for the adjustment method.
16.5.
Make movement of the robot speedy
Adjust the following setting to make movement of the robot speedy.
1)
Adjustment of the optimal acceleration-and-deceleration setting
Set mass, size, and center of gravity of the hand installed in the robot as the parameter "HNDDAT1.
"
And, set mass, size, and center of gravity of the work as the parameter "WRKDAT1."
By this setting, the robot can move with the optimal acceleration and deceleration and speed.
Refer to "Table
" for setting method.
2)
Adjustment of carrying height
By making low distance at adsorption and release of robot, the moving distance decreases and motion
time can be shortened as a result. Refer to the adjustment variable of "Pup1"and "Pup2" in the "
1 List of adjustment variables in the program
" (high speed and accuracy tracking) or "Table
of variable for operating conditions" (circular arc tracking) for change of rise distance.
16.6.
Restore backup data to another controller
The status variable "P_EncDlt
()" is not saved in the backup data from tracking system robot
controller.
To generate the value of "
P_EncDlt(MENCNO)
", execute the "P_EncDlt(MENCNO) =PY10ENC"
command of "Program A" by step forward. (Movin
g distance per one pulse)
Summary of Contents for CR800 Series
Page 2: ......
Page 12: ......
Page 202: ...18 Appendix 18 190 Calibration sheet ...
Page 203: ......