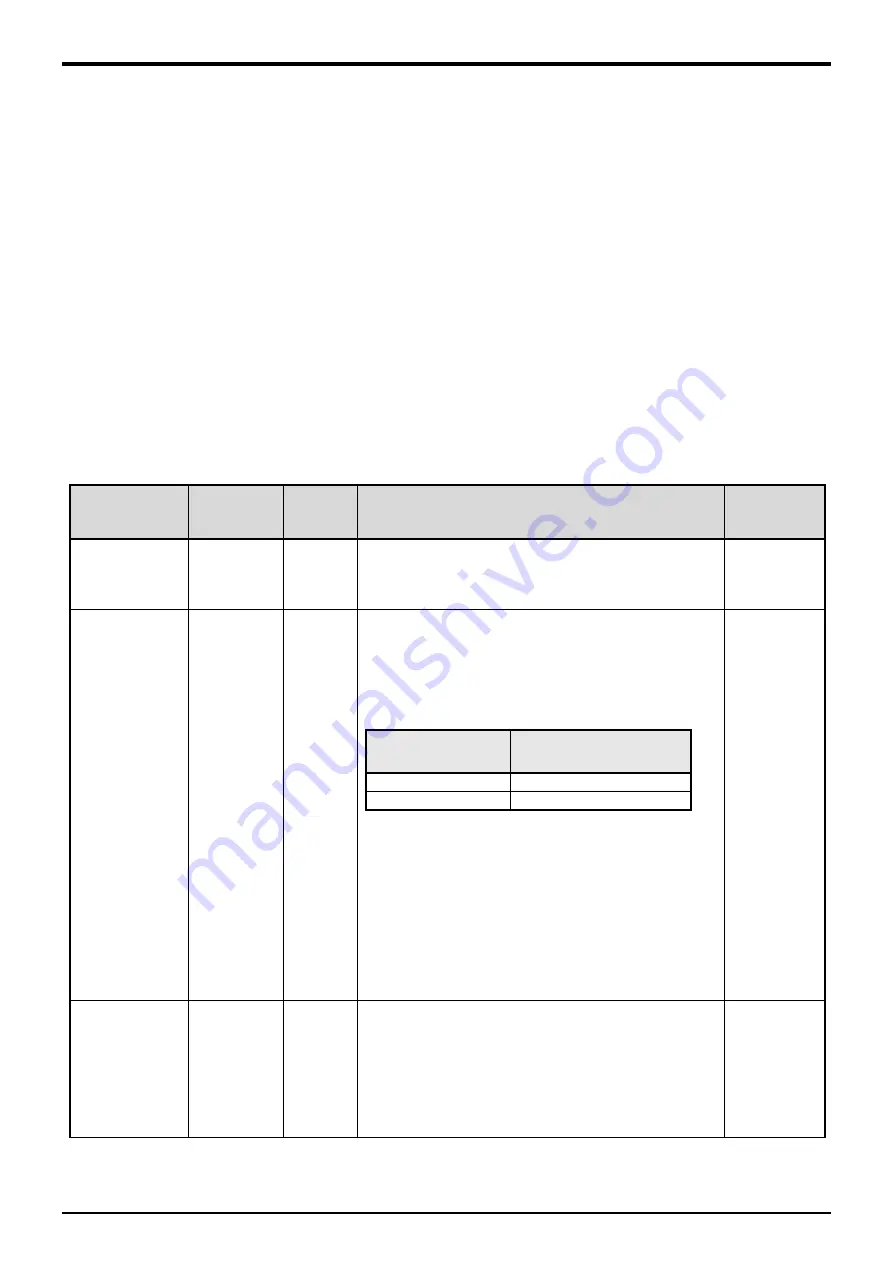
6 Parameter Setting
Tracking Parameter Setting 6-33
6.
Parameter Setting
This chapter explains how to set dedicated input/output signals that play the role of interface between a robot and an
external device (e.g., a Programmable Logic Controller) and parameters related to the tracking function.
Please refer to “Detailed Explanations of Functions and Operations” for how to set the parameters.
6.1.
Tracking Parameter Setting
Specify to which channel of the encoder connector an encoder of conveyer is connected.
The parameter settings for the robot CPU and PLC CPU are shown below. Make the settings as required.
6.1.1.
Robot CPU parameter setting
After the installation of
Q173DPX module and connection with the encoder are complete, use the following steps to
establish robot CPU parameters.
[D type or R type]
(1) Set a parameter TRMODE to 1, validate a function of tracking.
(2) Specify the channel to which the encoder is connected using a parameter EXTENC.
(3) Reset a power supply and reflect a parameter.
Table 6-1 Tracking Parameter Setting [D type or R type]
Parameter
Parameter
name
Number
of
elements
Explanation
Value set at
factory
shipping
Tracking mode
TRMODE
1 integer
Enable the tracking function
Please set it to “1" when you use the tracking
function.
0: Disable/1: Enable
0
→
1
Encoder
number
allocation
EXTENC
8
integers
Set connection destinations on the connector for
encoder numbers 1 to 8.
Parameter elements correspond to encoder number
1, encoder number 2 … encoder number 8 of a state
variable "M_Enc" from the left.
Setting value is input encoder physics number from
below list.
Encoder
physics number
Connection channel
1
Standard CH1
2
Standard CH2
In the initial setting, the value of the encoder which is
wired to the channel 1 of the encoder input connector
can be c
hecked with the status variables "M_Enc
(1)", "M_Enc (3)", "M_Enc (5)", and "M_Enc (7)". The
value of the encoder which is wired to the channel 2
can be checked with the status variables "M_Enc
(2)", "M_Enc (4)", "M_Enc (6)", and "M_Enc (8)".
Please refer
to "
List of Robot Status Variables
for the explanation of state variable “M_Enc".
Please refer to “Detailed Explanations of Functions
and Operations” for how to check the status variable.
1,2,1,2,1,2,1,2
↓
Change the
set value
according to
the situation.
Tracking
Workpiece
judgment
distance
TRCWDST
1 integer
Distance to judge that the same workpiece is being
tracked (mm)
The sensor reacts many times when the workpiece
with the ruggedness passes the sensor. Then, the
robot controller judged that one workpiece is two or
more pieces.
The sensor between values [mm] set to this
parameter does not react after turning on the sensor.
5.00
↓
Size of the
workpiece
Summary of Contents for CR800 Series
Page 2: ......
Page 12: ......
Page 202: ...18 Appendix 18 190 Calibration sheet ...
Page 203: ......