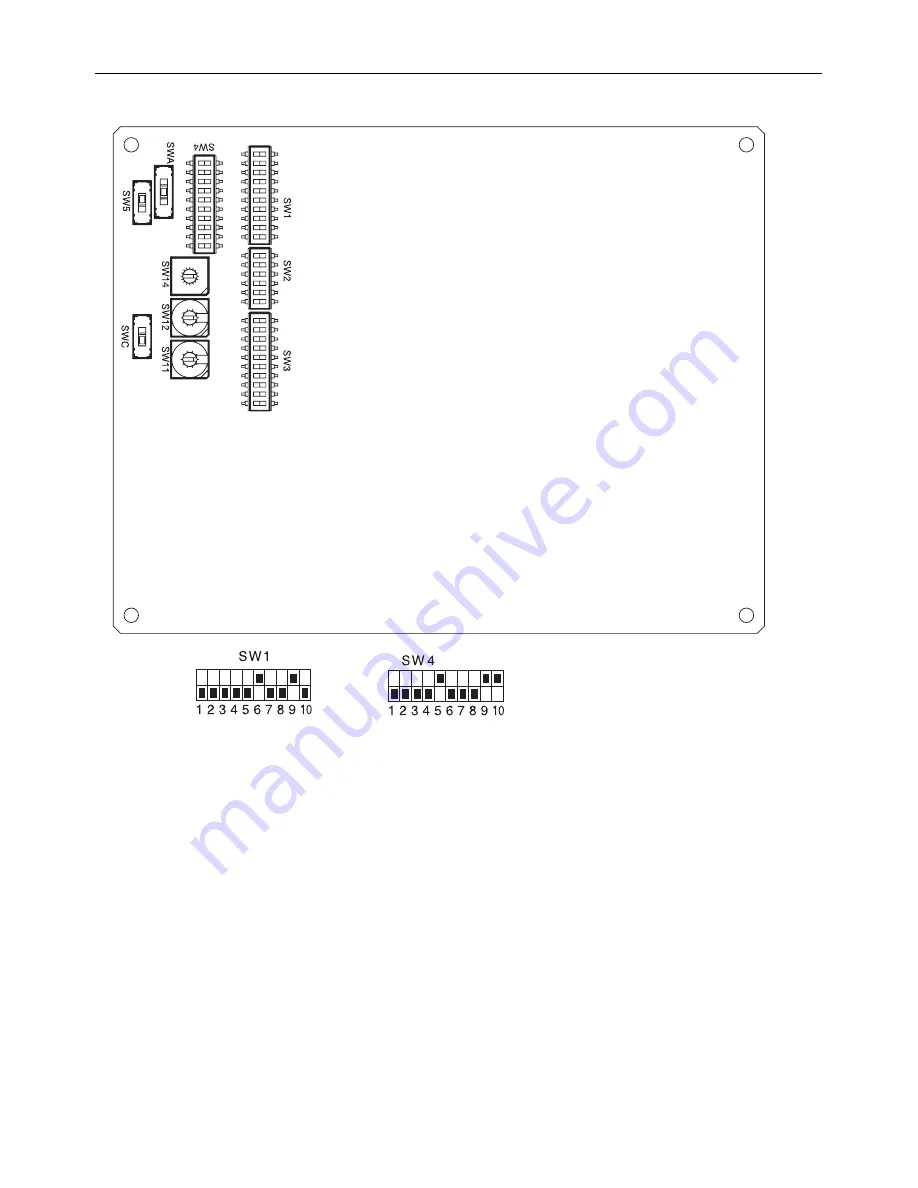
[
VIII
Troubleshooting ]
- 26 -
HWE09040
GB
3. Address switch setting
Make sure that power to the unit is turned off.
1. When using an ME remote controller, set the address with the rotary switches (SW11, SW12).
Address setting is not required when the unit remote controller is used.
On-site address setting is required for the indoor units to run.
2. Address settings vary in different systems.
Refer to the section on address setting in the outdoor unit installation manual.
3. Address is set with a combination of SW12 (10's digit) and SW11 (1's digit).
To set the address to "3," set SW12 to "0" and SW11 to "3."
To set the address to "25," set SW 12 to "2" and SW 11 to "5."
(A)
Indoor unit control board
(B)
Factory setting (all models)
ON
OFF
ON
OFF
(A)
(B)
Summary of Contents for CITY MULTI PEFY-P06NMAU-E
Page 5: ...HWE09040 GB ...