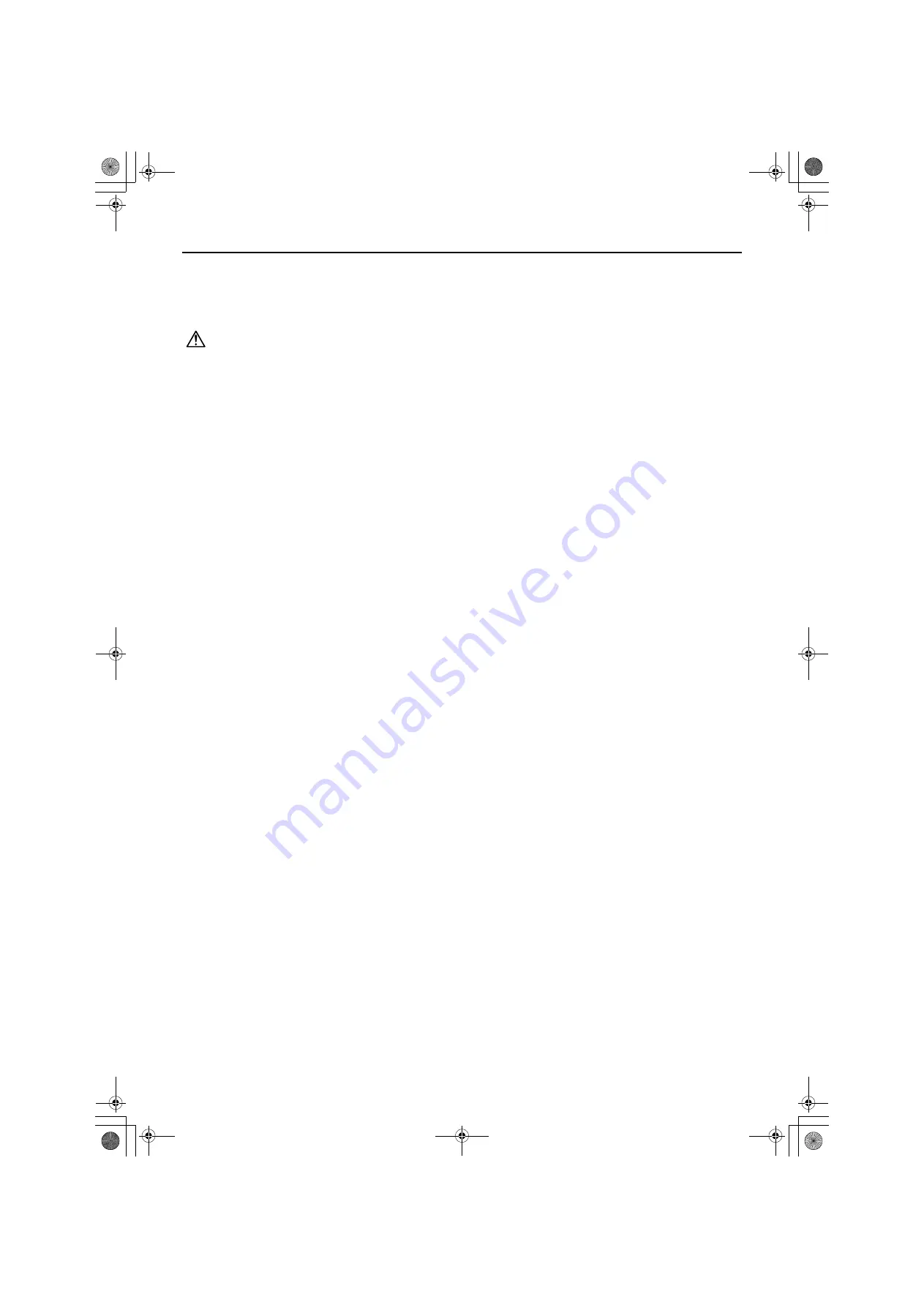
iiii
HWE19070
GB
Pay a special attention to the place, such as a basement, etc. where re-
frigeration gas can stay, since refrigeration is heavier than the air.
This appliance is intended to be used by expert or trained users in shops,
in light industry and on farms, or for commercial use by lay persons.
Precautions for devices that use R32/R410A refrigerant
Do not use the existing refrigerant piping.
- The old refrigerant and refrigerator oil in the existing piping contains a large
amount of chlorine which may cause the refrigerator oil of the new unit to de-
teriorate.
Use refrigerant piping made of C1220 (Cu-DHP) phosphorus deoxidized
copper as specified in the JIS H3300 “Copper and copper alloy seam-
less pipes and tubes”. In addition, be sure that the inner and outer sur-
faces of the pipes are clean and free of hazardous sulphur, oxides, dust/
dirt, shaving particles, oils, moisture, or any other contaminant.
- Contaminants on the inside of the refrigerant piping may cause the refriger-
ant residual oil to deteriorate.
Store the piping to be used during installation indoors and keep both
ends of the piping sealed until just before brazing. (Store elbows and
other joints in a plastic bag.)
- If dust, dirt, or water enters the refrigerant cycle, deterioration of the oil and
compressor trouble may result.
Use liquid refrigerant to fill the system.
- If gas refrigerant is used to seal the system, the composition of the refriger-
ant in the cylinder will change and performance may drop.
Do not use a refrigerant other than R32/R410A.
- If another refrigerant (R22, etc.) is used, the chlorine in the refrigerant may
cause the refrigerator oil to deteriorate.
Use a vacuum pump with a reverse flow check valve.
- The vacuum pump oil may flow back into the refrigerant cycle and cause the
refrigerator oil to deteriorate.
Do not use the following tools that are used with conventional refriger-
ants. (Gauge manifold, charge hose, gas leak detector, reverse flow
check valve, refrigerant charge base, vacuum gauge, refrigerant recov-
ery equipment)
- If the conventional refrigerant and refrigerator oil are mixed in the R32/
R410A, the refrigerant may deteriorated.
- If water is mixed in the R32/R410A, the refrigerator oil may deteriorate.
- Since R32/R410A does not contain any chlorine, gas leak detectors for con-
ventional refrigerants will not react to it.
Do not use a charging cylinder.
- Using a charging cylinder may cause the refrigerant to deteriorate.
Be especially careful when managing the tools.
- If dust, dirt, or water gets in the refrigerant cycle, the refrigerant may deteri-
orate.
Cautions for unit using R32 refrigerant
Basic work procedures are the same as those for conventional units us-
ing refrigerant R410A. However, pay careful attention to the following
points.
(1) Information on servicing
(1-1) Checks on the Area
Prior to beginning work on systems containing flammable refrigerants,
safety checks are necessary to ensure that the risk of ignition is mini-
mized.
For repair to the refrigeranting systems, (1-3) to (1-7) shall be complet-
ed prior to conducting work on the systems.
(1-2) Work Procedure
Work shall be undertaken under a controlled procedure so as to mini-
mize the risk of a flammable gas or vapor being present while the work
is being performed.
(1-3) General Work Area
All maintenance staff and others working in the local area shall be in-
structed on the nature of work being carried out.
Work in confined spaces shall be avoided. The area around the work-
space shall be sectioned off. Ensure that the conditions within the area
have been made safe by control of flammable material.
(1-4) Checking for Presence of Refrigerant
The area shall be checked with an appropriate refrigerant detector prior
to and during work, to ensure the technician is aware of potentially toxic
or flammable atmospheres. Ensure that the leak detection equipment
being used is suitable for use with all applicable refrigerants, i.e. non-
sparking, adequately sealed or intrinsically safe.
(1-5) Presence of Fire Extinguisher
If any hot work is to be conducted on the refrigeration equipment or any
associated parts, appropriate fire extinguishing equipment shall be
available to hand.
Have a dry powder or CO2 fire extinguisher adjacent to the charging area.
(1-6) No Ignition Sources
No person carrying out work in relation to a refrigeration system which
involves exposing any pipe work shall use any sources of ignition in
such a manner that it may lead to the risk of fire or explosion. All possi-
ble ignition sources, including cigarette smoking, should be kept suffi-
ciently far away from the site of installation, repairing, removing and
disposal, during which refrigerant can possibly be released to the sur-
rounding space. Prior to work taking place, the area around the equip-
ment is to be surveyed to make sure that there are no flammable
hazards or ignition risks. “No Smoking” signs shall be displayed.
(1-7) Ventilated Area
Ensure that the area is in the open or that it is adequately ventilated be-
fore breaking into the system or conducting any hot work. A degree of
ventilation shall continue during the period that the work is carried out.
The ventilation should safely disperse any released refrigerant and pref-
erably expel it externally into the atmosphere.
(1-8) Checks on the Refrigerantion Equipment
Where electrical components are being changed, they shall be fit for the
purpose and to the correct specification. At all times the manufacturer’s
maintenance and service guidelines shall be followed. If in doubt, con-
sult the manufacturer’s technical department for assistance.
The following checks shall be applied to installations using flammable
refrigerants:
• The charge size is in accordance with the room size within which the
refrigerant containing parts are installed.
• The ventilation machinery and outlets are operating adequately and
are not obstructed.
• Marking to the equipment continues to be visible and legible. Mark-
ings and signs that are illegible shall be corrected.
• Refrigeration pipe or components are installed in a position where
they are unlikely to be exposed to any substance which may corrode
refrigerant containing components, unless the components are con-
structed of materials which are inherently resistant to being corroded
or are suitably protected against being corroded.
(1-9) Checks on Electrical Devices
Repair and maintenance to electrical components shall include initial
safety checks and component inspection procedures.
If a fault exists that could compromise safety, then no electrical supply
shall be connected to the circuit until it is satisfactorily dealt with. If the
fault cannot be corrected immediately but it is necessary to continue op-
eration, an adequate temporary solution shall be used. This shall be re-
ported to the owner of the equipment so all parties are advised.
Initial safety checks shall include that:
• capacitors are discharged: this shall be done in a safe manner to
avoid possibility of sparking;
• no live electrical components and wiring are exposed while charging,
recovering or purging the system;
• there is continuity of earth bonding
(2) Repairs to Sealed Components
(2-1) During repairs to sealed components, all electrical supplies shall be dis-
connected from the equipment being worked upon prior to any removal
of sealed covers, etc. If it is absolutely necessary to have an electrical
supply to equipment during servicing, then a permanently operating
form of leak detection shall be located at the most critical point to warn
of a potentially hazardous situation.
(2-2) Particular attention shall be paid to the following to ensure that by work-
ing on electrical components, the casing is not altered in such a way that
the level of protection is affected. This shall include damage to cables,
excessive number of connections, terminals not made to original spec-
ification, damage to seals, incorrect fitting of glands, etc.
Ensure that the apparatus is mounted securely.
Ensure that seals or sealing materials have not degraded to the point
that they no longer serve the purpose of preventing the ingress of flam-
mable atmospheres.
Replacement parts shall be in accordance with the manufacturer’s
specifications.
(3) Repair to intrinsically Safe Components
Do not apply any permanent inductive or capacitance loads to the circuit
without ensuring that this will not exceed the permissible voltage and cur-
rent permitted for the equipment in use.
Intrinsically safe components are the only types that can be worked on
while live in the presence of a flammable atmosphere. The test apparatus
shall be at the correct rating.
Replace components only with parts specified by the manufacturer. Other
parts may result in the ignition of refrigerant in the atmosphere from a leak.
(4) Cabling
Check that cabling will not be subject to wear, corrosion, excessive pres-
sure, vibration, sharp edges or any other adverse environmental effects.
The check shall also take into account the effects of aging or continual vi-
bration from sources such as compressors or fans.
(5) Detection of Flammable Refrigerants
Under no circumstances shall potential sources of ignition be used in the
CAUTION
HWE19070.book Page ii Thursday, September 12, 2019 3:46 PM