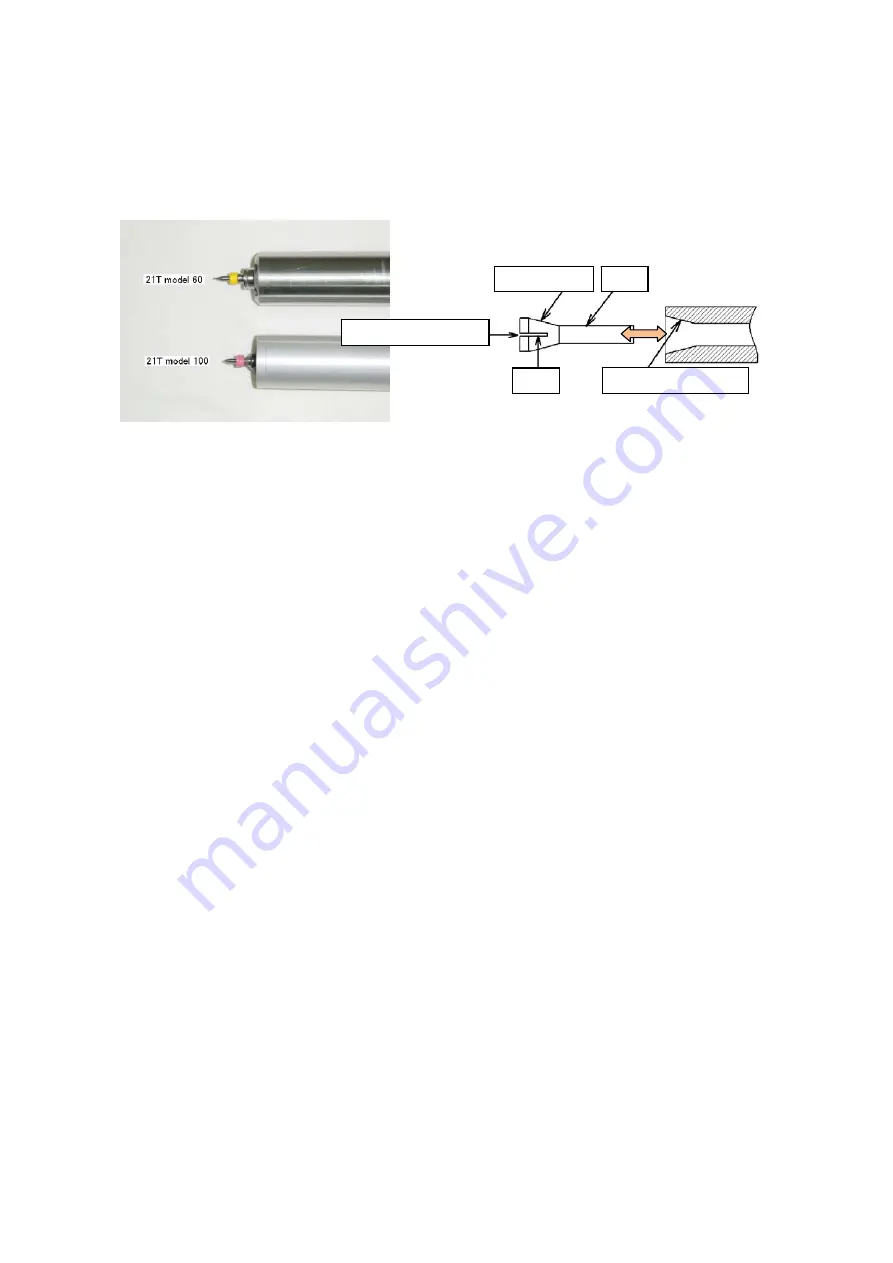
2
1. Needs Frequent
Cleaning
The initial failure of a spindle motor is mostly caused by scraped particles getting
inside a collet chuck.
Scraped particles are generated every time when the spindle motor cuts a board or
etc. We have already provided our PCB prototyping machine with vacuum cleaner
function. However, it is difficult to completely avoid a small amount of scraped
particles getting into the engagement region between the collet and the body of the
spindle motor.
The parts shown in the picture above have the structure as shown in the drawing at
right. You need to clean these designated parts: the inside diameter region, the slit,
the taper, and the pilot of the collet; and the taper region within the spindle motor.
Even a small amount of scraped particles remaining in the engagement region can
deteriorate the rotational precision and weaken the holding power of a drill.
Gradually the drill may become loose resulting in failure of the spindle motor and
finally damage to our PCB prototyping machine.
We highly suggest that you clean the spindle motor with the cleaning set provided
every time you finish processing.
<How to clean the spindle motor>
Clean the inside of the taper with a brush provided with the system.
Do not use the air unit while cleaning the spindle motor. If you use the air, scraped
particles are more likely to get into the inside of the spindle motor.
Inside diameter region
Slit
Taper of spindle motor
Taper of collet
Pilot