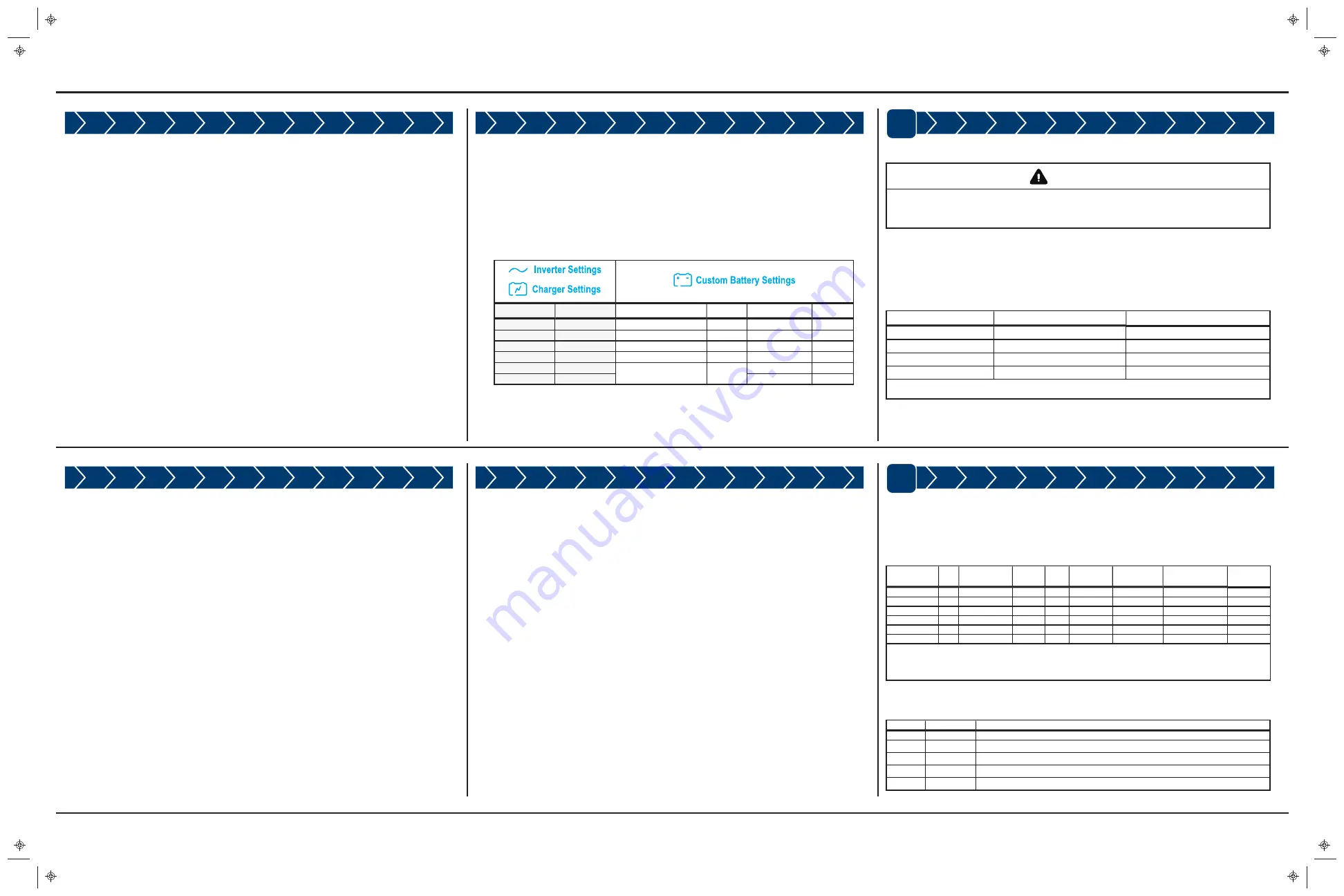
http://www.xantrex.com
Freedom e-GEN System Installation Guide for OEM Installers
975-0790-01-01 Rev J
Dec 2020
Copyright © 2019-2020 Xantrex LLC. All Rights Reserved.
All trademarks are owned by Xantrex LLC and its affiliates.
3
l
Use DC cables with a higher insulation temperature rating (105 °C) if possible.
However, a higher insulation temperature rating does not mean the conductor size
can be reduced due to the temperature ratings of the terminal connections. Always
use a qualified installer to ensure conductor sizing complies with regional, national,
and local electrical codes.
l
The DC cables must be UL marked and certified.
l
Longer cables may cause excessive voltage drop and affect system performance.
Keep cable length as short as practically possible.
l
Use twin wires [pos(+) and neg(-) DC cables] for all DC connections. Do not use the
vehicle chassis in place of the DC negative connection. The system requires reliable
DC return paths.
l
The battery system must be used with a Xantrex-approved fuse (see
for a list
of approved fuse options). The main battery fuse and all other fuses in the system
must be installed on the positive (ungrounded) conductor as close to their power
sources as possible. Distance restrictions may apply according to applicable codes.
l
The DC load branch, if installed, must be properly fused. The total DC load branch
should not exceed 30A to avoid overheating the main DC cables and blowing the
main battery fuse. It is the installer's responsibility to ensure the voltage, current and
interrupt ratings of the DC load branch fuse are adequate to protect the cables and
downstream loads according to applicable codes.
l
Use Xantrex-approved busbars (Blue Sea, 2104) to make the DC interconnections to
ensure sufficient current-carrying capacity. You must follow the connection order at
the busbar terminal studs (DC load - alternator - BMS - Freedom SW) as shown in the
system diagram for optimal heat transfer. Use the same connection order for both
positive and negative busbars.
l
Ensure there is sufficient space between the DC positive and negative busbars and
fuse holders.
l
All terminals must be tightened according to the manufacturer’s torque specifications.
l
Certain codes require a service disconnect such as a battery disconnect switch. In
this case, you must select a battery disconnect switch with a continuous current rating
of no less than 450A and a voltage rating of no less than 12V.
l
Ensure all system devices are properly and securely grounded to the vehicle chassis
using the correct wire sizes.
l
Install terminal covers and make sure there are no exposed conductors.
6
Arc Flash Energy Specifications
below quantifies the hazard level of arc flash energy that each battery system is capable of
producing. Calculations are based on NFPA 70E D.5.1 using the Maximum Power Method applied for a
maximum of six modules in parallel connection.
Configuration
V
sys
Impedance mΩ
Ibf, calc.
I
arc
IEm cal/cm
2
3x IEm cal/cm
2
Distance where
IEm=1.2 (Arc
Boundary), inches.
Hazard level
GT12V450
12.8
0.34
37833
18916
0.082
0.246
4
0
GT12V525
12.8
0.3
43390
21695
0.094
0.282
5
0
GT12V600
12.8
0.35
36398
18199
0.079
0.236
4
0
GT24V300
25.6
0.32
80000
40000
0.346
1.039
9
0
GT48V150
48
0.9
53432
26716
0.434
1.301
10
0
GT51V150
51.2
0.85
60117
30059
0.52
1.561
11
0
Formula:
I
arc
= 0.5 × Ibf
IEm = 0.01 × V
sys
× I
arc
× *T
arc
÷ D
2
(Arc Flash Energy)
T
arc
= 70ms fuse clearing time
Table 5 Hazard level of arc flash energy
Category
Energy level
Typical PPE examples
0
n/a
non-melting, flammable materials (e.g. untreated cotton, wool, rayon, etc.)
1
5 cal/cm
2
Fire resistant (FR) shirt and fire resistant (FR) pants
2
8 cal/cm
2
Cotton und FR shirt and FR pants
3
25 cal/cm
2
Cotton und FR shirt and FR pants + FR coverall
4
40 cal/cm
2
Cotton und FR shirt and FR pants + double layer switching coat and pants
Table 6 Hazard/risk classification per NFPA 70E-2018
10. Make the system communication connections between all system devices using the
provided system wiring harness (881-0040-12). Use the labels on the wiring harness
as a guide and follow the “System Diagram for Communication Connection”. Follow
the vehicle manufacturer’s instructions when wiring to the vehicle’s ignition circuit.
11. End devices in the Xanbus network must both be terminated with a 120Ω resistor or a
Xanbus network terminator (PN: 809-0941). When integrating Xanbus devices into a
larger vehicle CAN network, termination resistors are required at each end of the
larger CAN network.
12. Ensure the installation complies with regional, national, and local electrical codes.
13. Make sure all DC and AC connections are secure. Install and put on all necessary
safeguard and covers. Make sure there are no exposed conductors. Remove LOTO.
14. Perform the end-of-line functional check (document number: 976-0361-01-01).
15. Follow the system user guide (document number: 975-0791-01-01) and perform the
following system configurations.
a. Download and install the ComBox Freedom SW app to the tablet.
b. Connect to the system ComBox using the app. See ComBox Owner’s Guide for
login instructions.The default user name is “admin” and the password is
“password”.
c. In the app, go to “Device Parameters” and configure the Freedom SW
inverter/charger settings as follows.
Parameter
Value
Parameter
Value
Parameter
Value
Low Batt Cut Out
10.5 V
Equalize Support
Disabled
Max Charge Rate
100%
LBCO Delay
10 sec (min)
Bulk Voltage
14.6 V
Charge Cycle
3-Stage
High Batt Cut Out
14.8 V
Absorb Voltage
14.6 V
Default Batt Temp
Warm
Battery Type
Custom
Float Voltage
13.4 V
ReCharge Volts
12.4 V
--
--
Batt Capacity (as applicable)
630 Ah
600 Ah
450 Ah
Absorb Time
30 min
--
--
Auto Charge Enable
Enabled
Table 3 Device parameters
5
DC Cable and Fuse Requirements
WARNING
HAZARD OF ELECTRIC SHOCK, FIRE, OR PERSONAL INJURY
Equipment shall only be installed and serviced by qualified electrical personnel who have training,
knowledge, and experience in installing electrical equipment and applying applicable installation codes.
Failure to follow these instructions can result in death or serious injury.
IMPORTANT
l
The following table contains the minimum system DC cable size requirements for
single-insulated copper conductors rated 75 °C in free air based on ambient
temperature of 30 °C according to NEC 2017 Table 310.15(B)(17). This table does
not apply to conductors in raceway or conduit, or in ambient above 30 °C.
Device*
Typical Amps (A)
Cable Size (AWG)**
Alternator
270
4/0
Freedom SW
320
4/0
BMS
300
4/0
Chassis battery
90
2
* cable is from the Device to the DC busbar
** free air, 30 °C ambient
Table 4 Minimum system DC cable size requirements