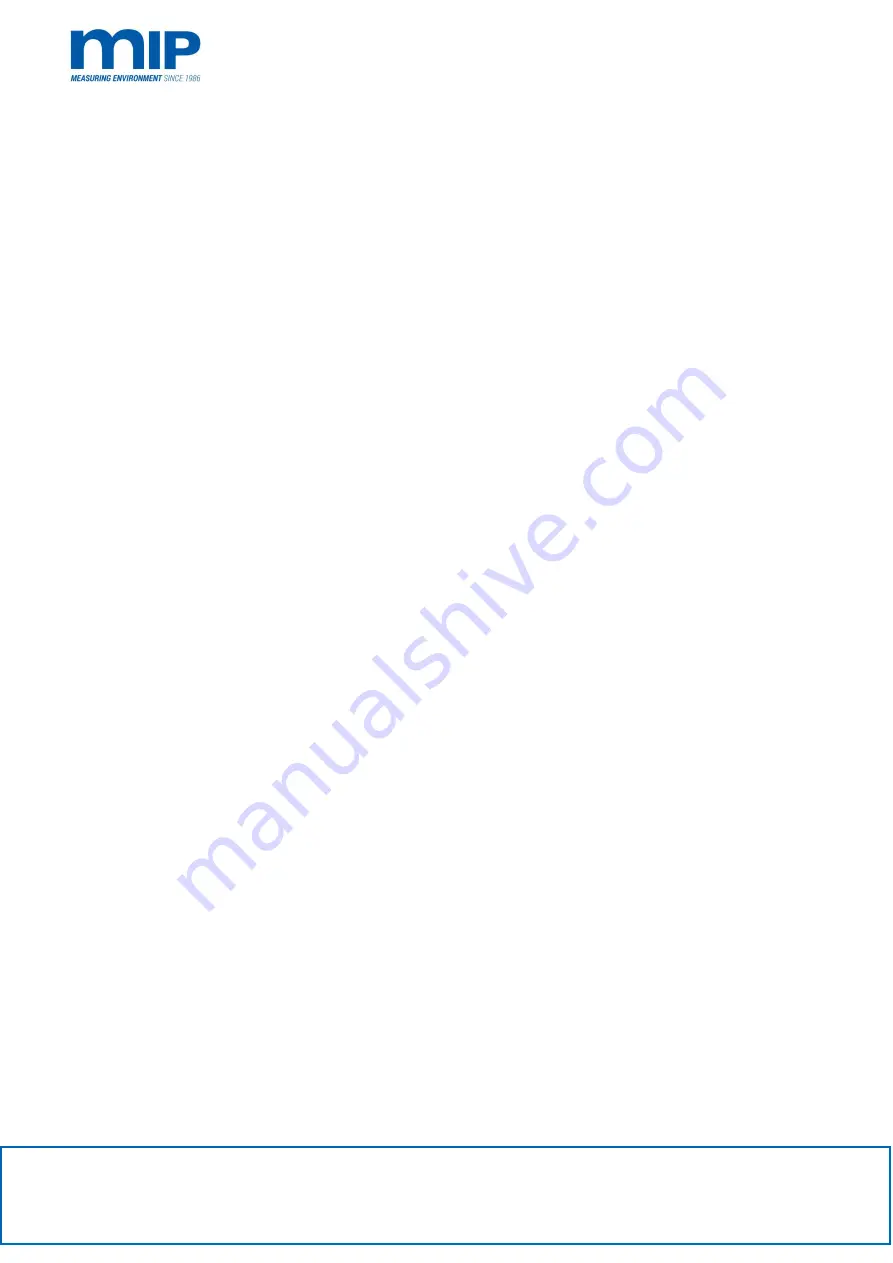
MIP LM 3086 SE/EPA3 manual, rev2
–
16.10.2018
Page 7 / 105
WWW.MIP.FI
Aanitasomittarit.fi
Langatonmittaus.fi
Mikrofonit.fi
Opacitymonitors.fi
MIP Electronics Oy
Palokorvenkatu 2
04250 KERAVA, FINLAND
Business ID: 1627111-2
EU VAT ID: FI16271112
+358 10 3222 631
[email protected]
1.
The clear path response (zero) of the under-fill system is independent of the path-length as the total
laser beam is confined inside the detector at any distance. In the overfill system, the amount of light
intensity decreases as the path-length grows. This means that the over-fill system must be zeroed for
each application and may require different hardware for different distances. The laser under-fill
system does not have an application dependent zero state and is portable to other applications with
different path-lengths.
2.
The response of the under-fill system is more uniform and more tolerant to cross stack alignment.
Small changes in the alignment due to temperature variations or vibrations are normally unavoidable
in stack emissions monitoring. With the under-fill system, any small deviations in cross-stack
alignment are not as critical as in the overfill system. In the under-fill system, alignment changes are
controlled by the size of the laser beam, and the oversized detector. As the laser beam moves due to
alignment shifts, the large detector having a large active surface, contains the laser beam within its
detector area. The detector is manufactured using a time-proven semiconductor process
guaranteeing uniform sensitivity across the entire surface (< 1 % deviation). No non-laser-based
opacity and dust monitor can make this guarantee. Of course, drastic shifts in alignment will affect
monitoring reliability when the laser beam shifts outside the detector area. High vibrations and
temperature shifts should be controlled as best as possible since they will affect the accuracy of the
reading, and the life-span of the monitor. All of these factors make the under-fill system superior to
the overfill system.
1.1.6
MAINTENANCE AND AUDIT PROCEDURE ADVANTAGES
Note: All screws and hex bolts are metric except for the laser 90ºdeflector hold-down bolts (4-40 UNC;
3/32”).
The big advantage of using the laser is that a minimum amount of optics, are needed in a normal monitoring
path. Because of the excellent collimation characteristic of the laser light sources, no collimation lenses are
used. In addition, since a dual-path exists using the zero pipes no retro-reflectors are needed. In fact, after
the small 90º turning mirror on the laser tube, there are no optical surfaces in the measurement path until
the laser beam reaches the receiver lens.
In the laser-based opacity and dust monitor, the only optical surfaces that are likely to accumulate dust are
those in the receiver. This includes the receiver lens, the zero pipe lens, and the two sides of the zero pipe
mirror. Opening can clean all three of which, the swing hinge held by four hex bolts (5 mm) on the receiver
side. The zero pipe mirror can be loosened with a 1.5 mm hex key. This amount of contamination is
constantly measured and compensated for during the zero cycle. Very rarely, the detector surface may need
cleaned. Before opening the hasp side exposing the detector, put the transmitter in audit mode. Sometimes
excessive light on the detector may overload the detector, causing the software to inaccurately report
opacity readings. DO NOT use any solvents to clean the detector, it will be damaged. Since the detector is
isolated from stack gases, it is rather unlikely that this will need to be cleaned, however, it should be checked
periodically. There is no need to remove the laser, transmitter, or the receiver for cleaning. There exists one
other optical surface, which should only be cleaned if a calibration problem occurs. Inside the optical block
(see drawings at end of this manual), there is a chopper mirror. While a blower protects this chopper mirror,
it is possible to get some dirt on the mirror. See the troubleshooting for help in diagnosing calibration
problems, and the appendices for cleaning procedures and guidelines.